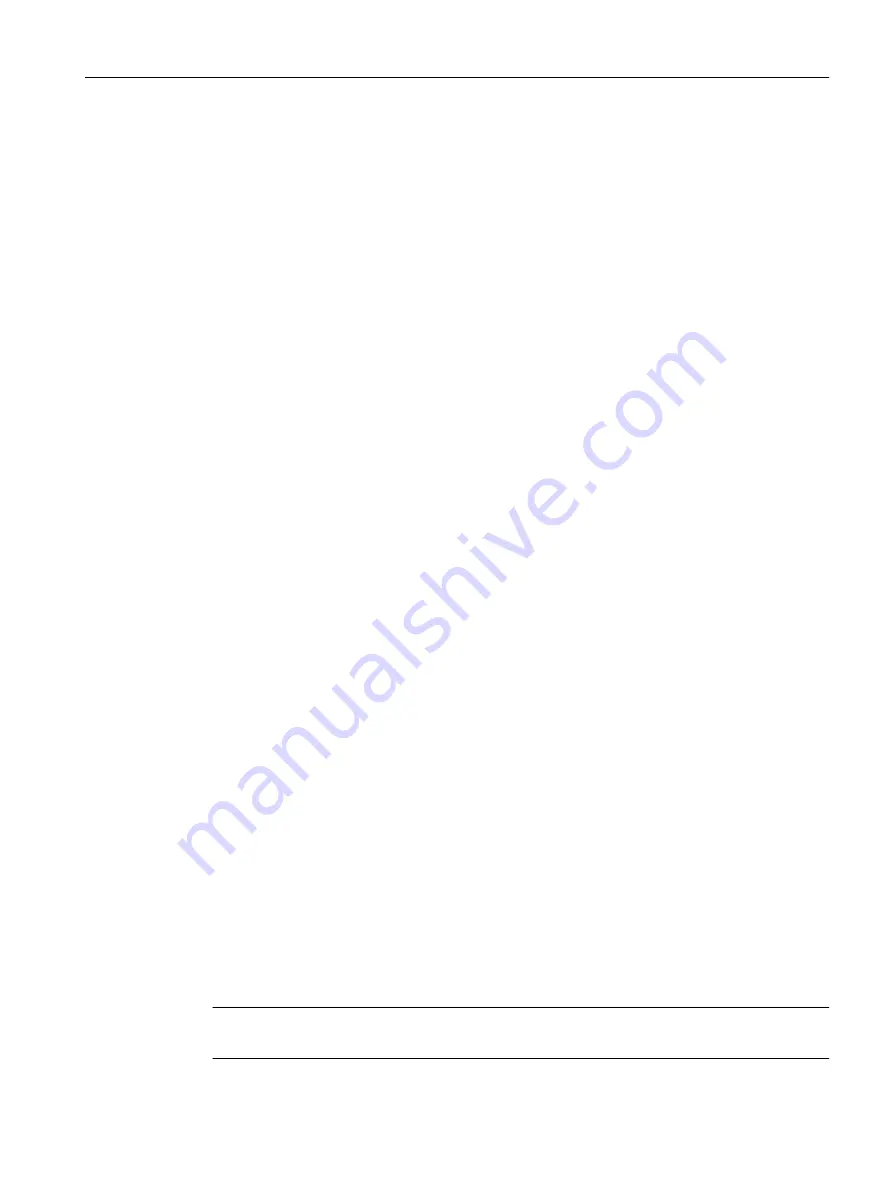
7.1.5
Testing the cooling of the machine
Cooling
● Check that the machine cooling is available for commissioning.
See also
7.1.6
Commissioning an external fan
The external fan ensures that the machine is cooled irrespective of the machine speed or
direction of rotation. The external fan is only suitable for one direction of rotation.
Checks before the first test run
Before the first test run, carry out the following checks:
● The external fan is correctly fitted and aligned.
● The rotor runs freely.
● All of the retaining elements and electrical connections are securely tightened.
● The grounding and equipotential bonding connections to the mains have been correctly
made.
● The air flow is not impeded or shut off by flaps, covers or similar.
● If the cooling air is in open circulation, it has only weak, chemically abrasive properties and
a low dust content.
● All protection measures have been taken to prevent accidental contact with moving or live
parts.
Performing the test run
1. Switch the external fan motor on and off briefly.
2. Compare the direction of rotation of the external fan with the specified direction of rotation.
The direction of rotation of the external fan is indicated with an arrow on the fan cover
specifying the direction of rotation or with a terminal designation on the rating plate of the
external fan unit.
Depending on the version, the fan impeller is visible through the air inlet opening in the fan
cover on the external fan motor.
3. If the direction of rotation is wrong, then interchange two line cables in the external fan motor
terminal box.
Note
Use these operating instructions for motors with external fans.
Commissioning
7.1 Measures before commissioning
1PC134, 1PC136 crane motors SH 132 ... 315
Operating Instructions, 02/2019, A5E43212221A
67