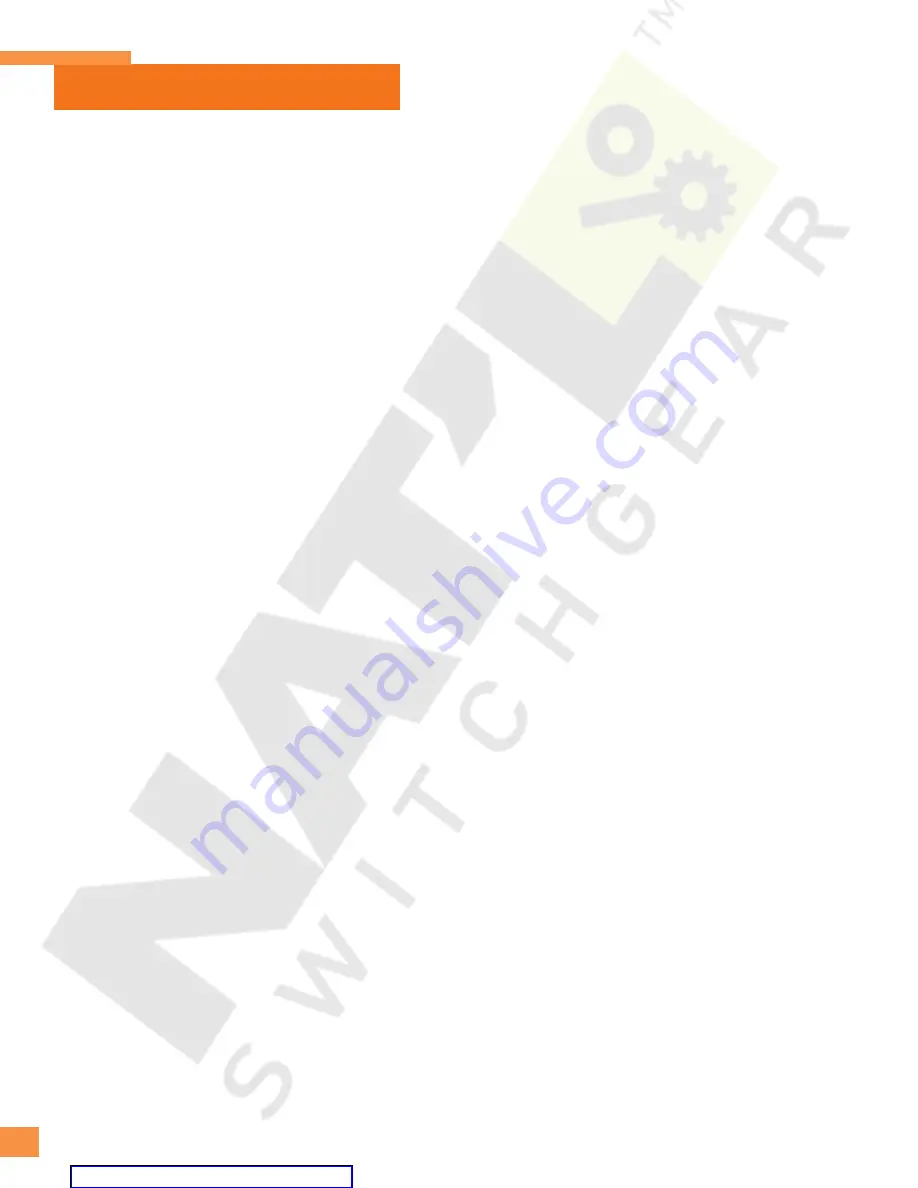
20
Interrupter/Operator Description
springs unless the breaker is either in the Test of
Connected position, or is out of the compartment.
Standard Schematic Diagrams
Note: Figure 28a
and
28b
show typical schematic for a
circuit breaker not provided with a capacitor trip device.
Figure 28c
shows a circuit breaker with capacitor tripping.
These are typical — refer to the specific drawing for your
project.
Inspection of the schematic diagrams shown in
Figures
28a-28c
provides a clear picture of the logic states of the
various devices for the three basic control functions.
These are: 1) automatic charging of the closing springs; 2)
electrical closing of the primary contacts; and 3) electrical
tripping of the primary contacts.
Automatic spring charging by charging motor occurs when
secondary control power is available, and motor cutoff
switch LS1 has not operated. The springs are automatically
recharged after each closing operation.
Electrical closing occurs with closing control power applied
and when all of the following conditions exist: 1) External
control switch CS/C is closed; 2) Anti-pump relay 52Y is not
energized; 3) Auxiliary switch 52b indicates the breaker is
in open position; 4) Limit switch LS3 shows that the trip
latch has been reset and the circuit breaker is in the Test or
Connected position, or is out of the compartment; and 5)
Limit switch LS2 indicates that the closing springs are
charged. Electrical tripping occurs with tripping control
power applied and when the auxiliary switch 52a shows
the circuit breaker is closed, and a trip signal is provided by
the control switch CS/T or the protective relays. While
external control power is required for either electrical
closing or tripping, the circuit breaker can be manually
charged, closed and tripped without external control
power.
Capacitor Trip Device (Optional)
The capacitor trip device is an auxiliary tripping option
providing a short term means of storing adequate
electrical energy to ensure circuit breaker tripping.
This device is applied in circuit breaker installations lacking
independent auxiliary control power or station battery. In
such installations, control power is usually derived from
the primary source. In the event of a primary source fault,
or disturbance with attendant depression of the primary
source voltage, the capacitor trip device will provide short
term tripping energy for circuit breaker opening due to
relay operation.
Refer to
Figure 28c
. An electrolytic capacitor resides across
the tripping supply voltage connected through a half wave
rectifier and resistor. The rectifier allows the capacitor to
assume a charge approximating the peak voltage of the AC
tripping supply voltage. The series resistor limits the
magnitude of charge current flowing into the capacitor.
The charged capacitor is then connected across the circuit
breaker trip coil circuit through an external contact which
closes upon trip command.
The capacitor size and charge current magnitude are tuned
to the inductance and resistance of the tripping solenoid,
an RLC series circuit, to produce a discharge current
through the solenoid, which emulates the magnitude of
current and current duration which the solenoid would
experience if operated from a DC tripping supply voltage.
Undervoltage Release (Optional)
The undervoltage release is used for continuous
monitoring of the tripping supply voltage. If the trip supply
voltage falls significantly, the undervoltage release will
provide for automatic tripping of the circuit breaker.
Description of Operation
The undervoltage release consists of a spring stored
energy mechanism, a latching device and an
electromagnet. These elements are accommodated in a
single assembly as shown in
Figure 29
.
The stored energy spring (1), spring charging arm (2) and
latch face are arranged in a cylindrical assembly concentric
with the trip latch shaft (3). The cylindrical assembly is re-
tained by the support bracket (4), yet remains free to
rotate. The cylindrical assembly is supported by the trip
latch shaft which rotates freely on the trip shaft supported
by needle bearings.
The stored energy torsion spring (1) has one tail bearing
on a lug fixed to the cylindrical assembly, and an opposite
tail fixed on a lug of the support bracket. Thus, the
torsional tension of the spring will cause the cylindrical
assembly (5) to be forcibly rotated relative to the support
bracket.
The cylindrical assembly is notched at the end nearest the
mechanism side sheet with the notch engaging a spring
pin (6) driven into the trip latch shaft. The notch has suffi-
cient arc width to permit the trip latch shaft to rotate
normally in response to the circuit breaker receiving a trip
command.
The circuit breaker jackshaft (7) is fitted with an arm and
track roller (8) which bears on the charging arm (2) of the
cylindrical assembly. Whenever the circuit breaker is
opened, the arm and roller cause the charging arm to be
rotated charging or winding up the stored energy torsion
spring.