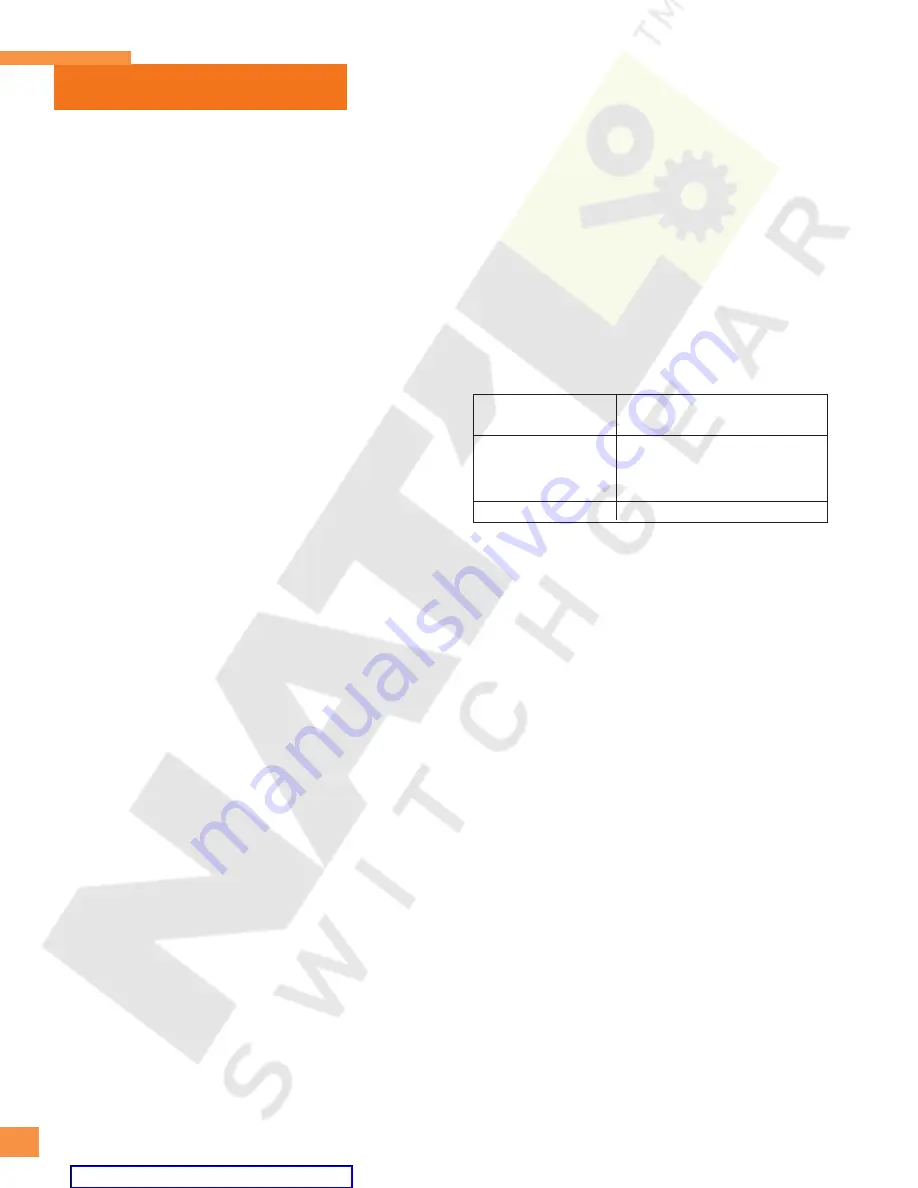
26
Maintenance
Checks of the Stored Energy Operator Mechanism
The stored energy operator checks are divided into
mechanical and electrical checks for simplicity and better
organization. This first series of checks determine if the
basic mechanism is clean, lubricated and operates
smoothly without control power. The contact erosion
check of the vacuum interrupter is also performed during
these tasks.
Maintenance and Lubrication
The operator mechanism shown in
Figure 35
with the
front cover and the operator control panel removed to
show construction details. Both the tripping spring and the
two closing springs are shown. The movable end of each
closing spring is connected to a crank arm. The movable
end of the opening spring is connected to the jack shaft by
a pull rod. The dashpot is connected to the jack shaft oper-
ating shaft by a pushrod linkage.
Clean the entire stored energy operator mechanism with a
dry, lint-free cloth.
Check all components for evidence of excessive wear. Place
special attention upon the closing spring cranks and the
various pushrods and linkages.
Lubricate all non-electrical moving or sliding surfaces with
a light coat of synthetic grease or oil. Lubricants composed
of diester oils and lithium thickeners will be compatible.
Shell (drawn cup) needle bearings: Use either Beacon
(Exxon) 325 (reference 18-658-676-422 and part number
15-337-131-001), or Supermil (Amoco) A-72832 (refer-
ence 18-758-676-423), or Anderol 732.
Pivots, sliding, and/or rolling surfaces and general lubrica-
tion: Use Anderol 732 aerosol synthetic fluid grease
(reference part number 15-172-816-058).
In addition to lubricating the stored energy operating mech-
anism, use Anderol 732 to lubricate both the OD of the
bushing and the ID of the wheel for the four floor wheels.
6. The circuit breaker can be located either on the floor
or on a pallet. Each circuit breaker has handles and
four wheels to allow one person to maneuver the unit
on a level surface without assistance.
Checks of the Primary Power Path
The primary power path consists of the three vacuum
interrupters, the three upper and the three lower primary
disconnects. These components are checked for cleanliness
and condition. The vacuum interrupters are also checked
for vacuum integrity.
Some test engineers prefer to perform the contact erosion
check during the manual spring charging check of the
operator, since charging of the springs is necessary to
place the contacts in the closed position.
Also, the vacuum integrity check is usually performed in
conjunction with the High Potential tests.
These instructions follow the recommendation that these
tests (contact erosion/manual spring charging check, and
vacuum integrity/high potential tests) will be combined as
described.
Cleanliness Check
Figure 33
is a side view of the GMI circuit breaker with the
outer insulating barriers removed to show the vacuum
interrupter, and the upper and lower primary disconnects.
All of these components must be cleaned and free of dirt
or any foreign objects. Use a dry lint-free cloth. For
stubborn dirt, use a clean cloth saturated with denatured
alcohol.
Inspection of Primary Disconnects
Figure 34
shows the primary disconnect contact fingers
engaged. When the contacts are mated with the
switchgear’s primary stud assembly, there is forceful
contact distributed over a wide area. This maintains low
current flow per individual contact finger.
Inspect the contact fingers for any evidence of burning or
pitting that would indicate weakness of the contact finger
springs.
Inspect the primary disconnect arms for physical integrity
and absence of mechanical damage.
Inspect the flexible connectors that connect the bottom
movable contacts of the vacuum interrupters to the lower
primary disconnect arms for tightness and absence of
mechanical damage, burning, or pitting.
Using a clean cloth saturated with denatured alcohol,
clean old lubricant from primary disconnects, and apply
Siemens contact lubricant (reference 15-172-791-233) in a
very thin layer.
Table 2: Maintenance and Lubrication Intervals
ANSI C37.06 Table 8 - Usual Service Conditions
Maintenance Based Upon Number of Circuit Breaker
Closing Operations
1
Five year interval for GMI circuit breakers manufactured January,
1992, or later.
One year interval for units manufactured earlier.
Circuit Number
of
Breaker Type
Years/Closing Operations
5-GMI-350
5-GMI-50
5 years
1
/ 1,000 operations
15-GMI-1000
15-GMI-50
All others
5 years
1
/ 2,000 operations