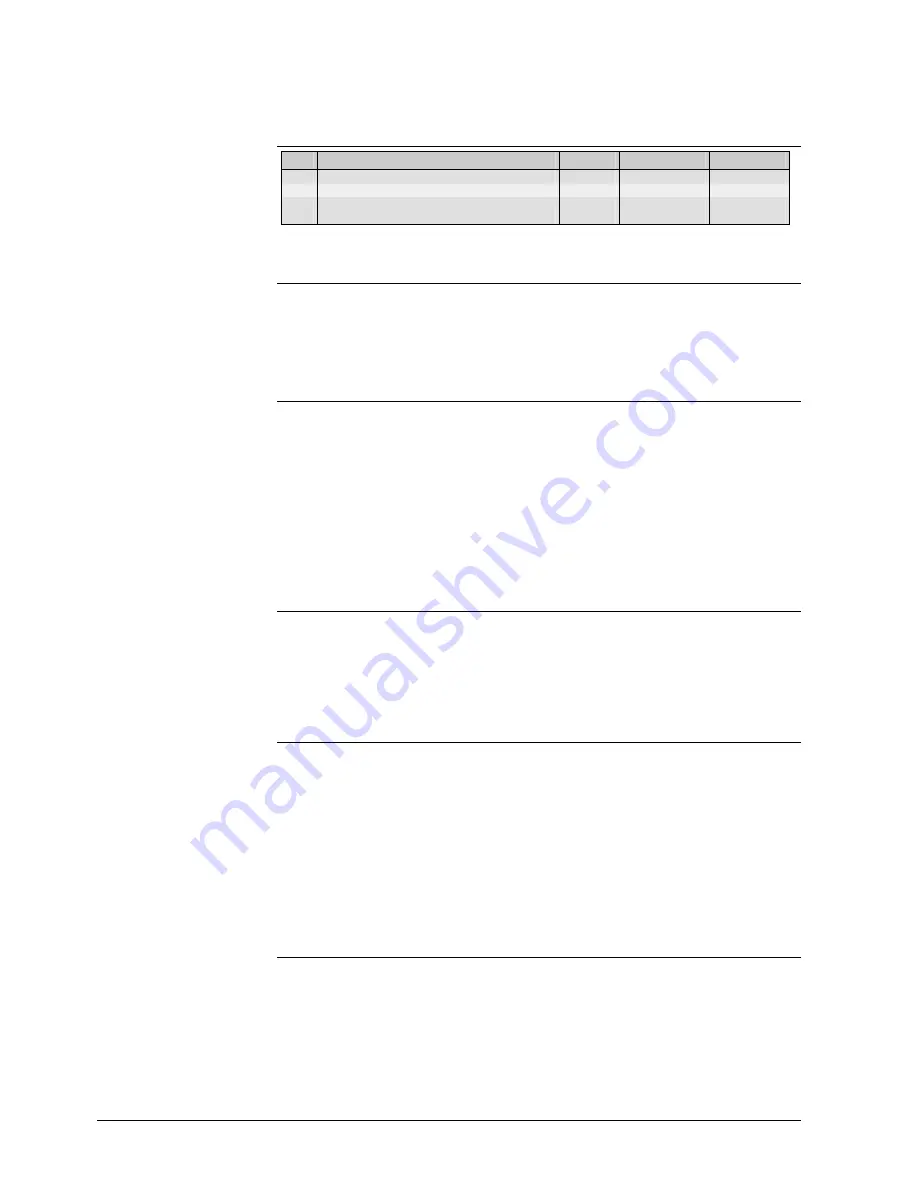
56/94
Siemens Building Technologies
Basic Documentation RVD110, RVD130
CE1P2381E
HVAC Products
17 Function block D.h.w. actuator 2
27.05.2004
17
Function block D.h.w. actuator 2
17.1 Operating lines
Line
Function, parameter
Unit
Factory setting
Range
121 Actuator running time, d.h.w. mixing valve Y7
s
35
10...873
122 P-band d.h.w. control Y7
K
35
1...100
123 Integral action time d.h.w. control Y7
s
35
10...873
124 Load limit when flow switch is actuated
%
25
0...60
17.2 Mode of operation
With plant type no. 5, this function block controls mixing valve Y7 of the secondary
d.h.w. circuit.
For details on this control, refer to section 17.4 ”Instantaneous d.h.w. heating”.
17.3 Control
process
If the actual flow temperature deviates from the setpoint, the mixing valve offsets the
deviation in a stepwise fashion. The controller drives the valve’s electric actuator whose
ideal running time is 30 to 35 seconds.
The actuator’s running time, P-band and integral action time are to be entered on oper-
ating lines 121 through 123, depending on the type of plant. Different times can be
entered for opening and closing, to allow for actuators with asymmetric running times.
17.4 Instantaneous d.h.w. heating
17.4.1 General
Direct d.h.w. heating is covered by plant types no. 4 and 5. In these plants, separate
heat exchangers are used in parallel mode for space heating and d.h.w. heating. Combi
heat exchangers also belong to this category.
The d.h.w. is heated with or without mixing in the secondary circuit.
17.4.2 Location of sensors
Special attention must be paid to the correct location of the sensors in the flow and the
return. Both sensors must be located in the heat exchanger itself, that is, not in the
secondary flow and return. Only then will it be possible to correctly acquire both tem-
peratures.
If the flow temperature sensor is not correctly located,
there is a risk of overtempera-
tures occurring in the heat exchanger.
Reason: D.h.w. heating is always permitted
with these types of plant, but the circulating pump runs only when released (operating
line 102)!
17.4.3 Flow
switch
The d.h.w. is heated directly via the heat exchanger. It is possible to fit a flow switch in
the cold water return to the heat exchanger. For that purpose, the RVD130 has a binary
input H5, which can be configured on operating line 54.
The flow switch is used to enhance the control performance of heat exchanger control.
The existence of flow is an indication that a demand for heat is expected. When there is
no flow, the supply of too hot d.h.w. to the point of consumption will be prevented.
Caution