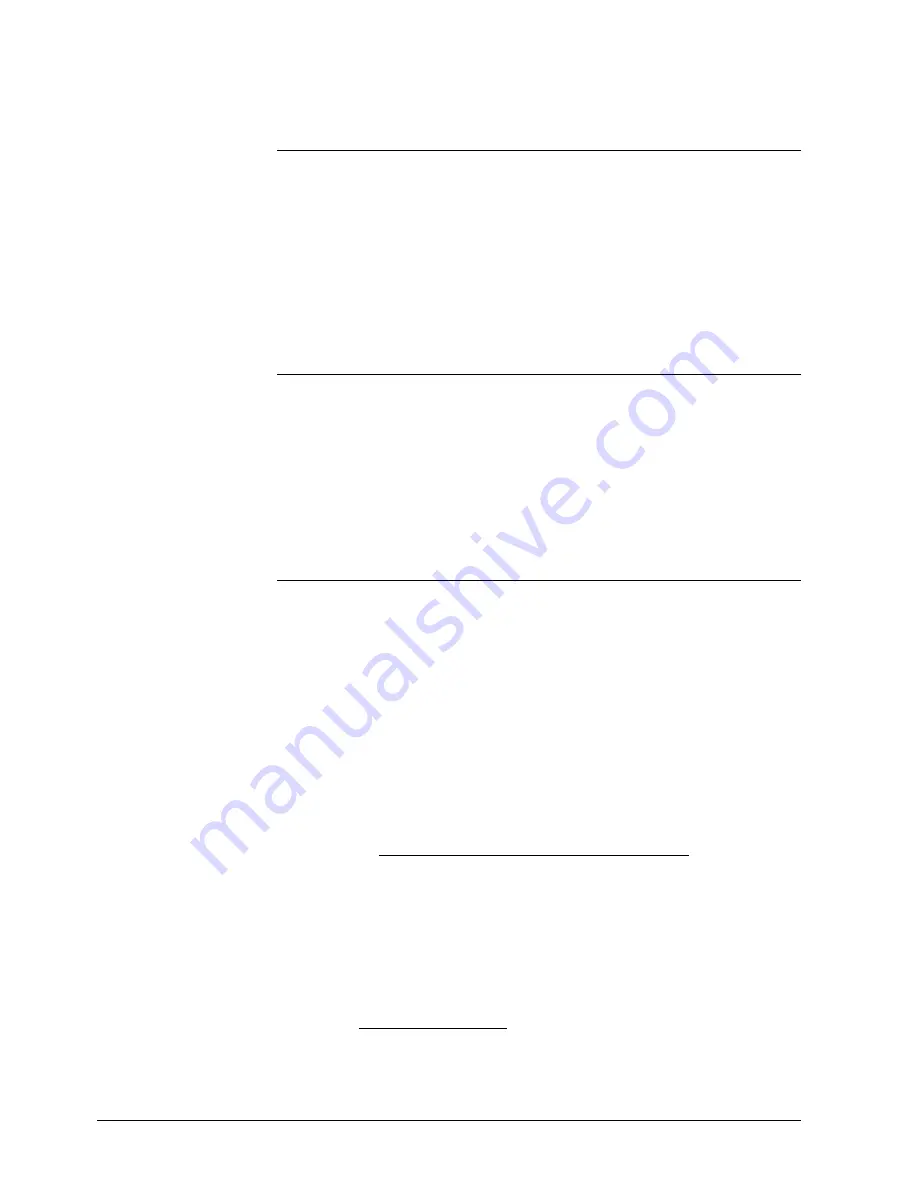
58/94
Siemens Building Technologies
Basic Documentation RVD110, RVD130
CE1P2381E
HVAC Products
17 Function block D.h.w. actuator 2
27.05.2004
The aim is to reach the d.h.w. setpoint and all heat losses are fully compensated. A
circulating pump must be installed.
17.4.5 Cold water sensor B71
By using a temperature sensor in the d.h.w. return, it is possible to achieve a similar
effect as with the flow switch (enhancement of control performance by acquiring the
temperatures before the water returns to the heat exchanger). The use of sensor B71 is
particularly recommended in larger plants. It must be installed after the mixing point of
cold water return and the return of circulation water. It should be installed as close as
possible to the mixing point. It detects temperature changes on the cold water side,
which are then considered by the flow temperature control, thus enhancing the control
performance. If sensor B71 is used in the d.h.w. circuit, maximum limitation of the tem-
perature differential in the heating circuit is not possible.
17.4.6 Adaptation
to
the time of year
To enable the controller to provide stable control of the d.h.w. also when connection
conditions change (summer / winter operation), the control must adjust the actuator’s
running time. This adaptation is accomplished with the
current maximum stroke
.
When the plant is switched on, the assumption is made that the current maximum
stroke is 50 %. If the controller drives the actuator beyond the 50 % position, the stroke
model continually adjusts the current maximum stroke ”towards 100 %”. At midnight,
the current maximum stroke will be reduced by 1 %. The minimum after longer plant off
times is 20 %.
17.4.7 Adjustable load limit
The flow switch delivers fast information, independent of the signal supplied by the
d.h.w. flow temperature sensor. This mode of operation ensures that the entire heat is
exchanged on the heat exchanger’s secondary side before the control of the primary
valve is passed to the d.h.w. control.
When d.h.w. consumption starts, the flow switch opens the primary valve Y5 for a cer-
tain period of time, independent of the flow temperature. This opening time can be set
on operating line 124, using the load limit setting. The setting is to be made as a per-
centage of the current maximum stroke.
Normally, in summer operation, to cope with a load of 100 %, the required d.h.w. actua-
tor position is about 80 %. This percentage is called the design point and must be in-
cluded in the calculation.
The load limit can be calculated with the help of the following formula:
Heat exchanger volume
secondary
Load limit =
Av. d.h.w. volume × opening time × design point
Example: Calculation of the load limit to be set for a heat exchanger with the following
specification:
Secondary water content
= 1.0 liter
Average d.h.w. volume consumed = 0.14 liter / second
Opening time of d.h.w. actuator
= 35 seconds
Design point
= 80 % (0.8)
1.0
Load limit =
0.14 ×
35 ×
0.8
×
100 = 25 %
Setting 3
Mode of operation
Calculation the setting
value