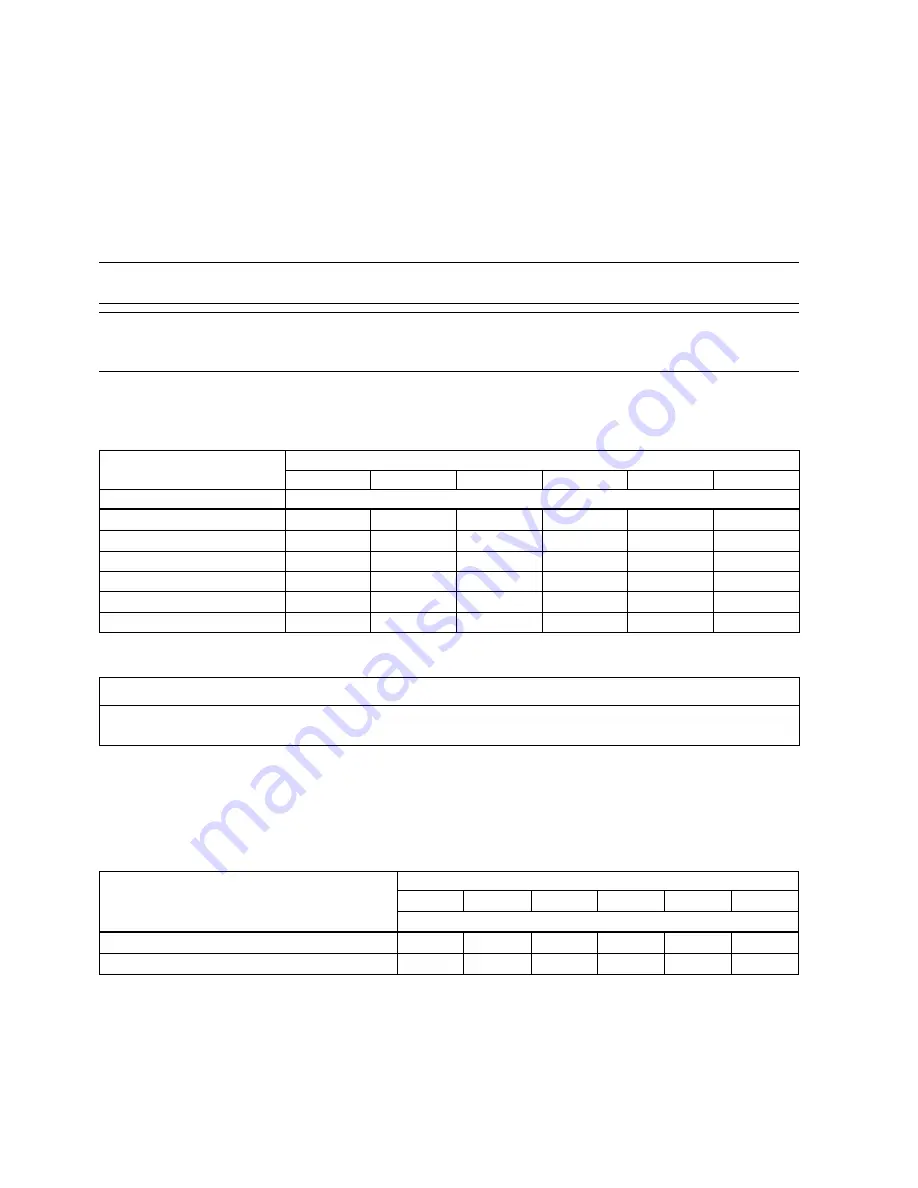
BA 2510
6
A5E38121849A/RS-AB, 10/2016
2.2
Lubrication
In normal operating conditions and with low loads, the lubrication of the bearings is sufficient for approximately 25,000 to
30,000 operating hours.
For higher loads due to speed and / or temperature, schedule regreasing at shorter intervals.
2.2.1
Regreasing intervals
The regreasing interval is valid for a temperature of +70 °C, measured on the surface of the housing in the vicinity of the
bearing.
Note
For temperatures above +70 °C, the regreasing interval must be reduced by half for each temperature increase of 15 K.
Note
For moderate shock loading and vibration, the regreasing interval must be reduced by 20 %.
For heavy loading, the regreasing interval must be reduced by half.
Regrease the bearing after the following number of operating hours.
Table 2-1
Regreasing intervals in operating hours for agitator flange
Output speed n
2
Operating hours for size
68
88
108
128
148
168
[rpm]
[h]
≤ 30
29 000
29 000
29 000
29 000
29 000
18 000
31 … 50
29 000
29 000
29 000
29 000
14 000
14 000
51 … 100
29 000
29 000
16 000
16 000
10 000
10 000
101 … 150
29 000
29 000
14 000
12 000
9 000
7 000
151 … 250
18 000
16 000
10 000
9 000
5 000
5 000
251 … 400
14 000
12 000
7 000
7 000
4 000
4 000
2.2.2
Roller bearing grease
NOTICE
When regreasing do not mix greases with different soap bases
For regreasing, use lithium-saponified roller bearing grease NLGI 3/2.
Using a grease gun, inject the grease into the bearing point via the lubricating nipples provided.
The grease quantities listed in the table are guide values.
Table 2-2
Grease quantities for regreasing the agitator flange
Regreasing interval
Grease quantity for regreasing for size
68
88
108
128
148
168
[g]
After 6 months
20
20
50
60
70
70
After several years without operation
50
60
120
160
170
200