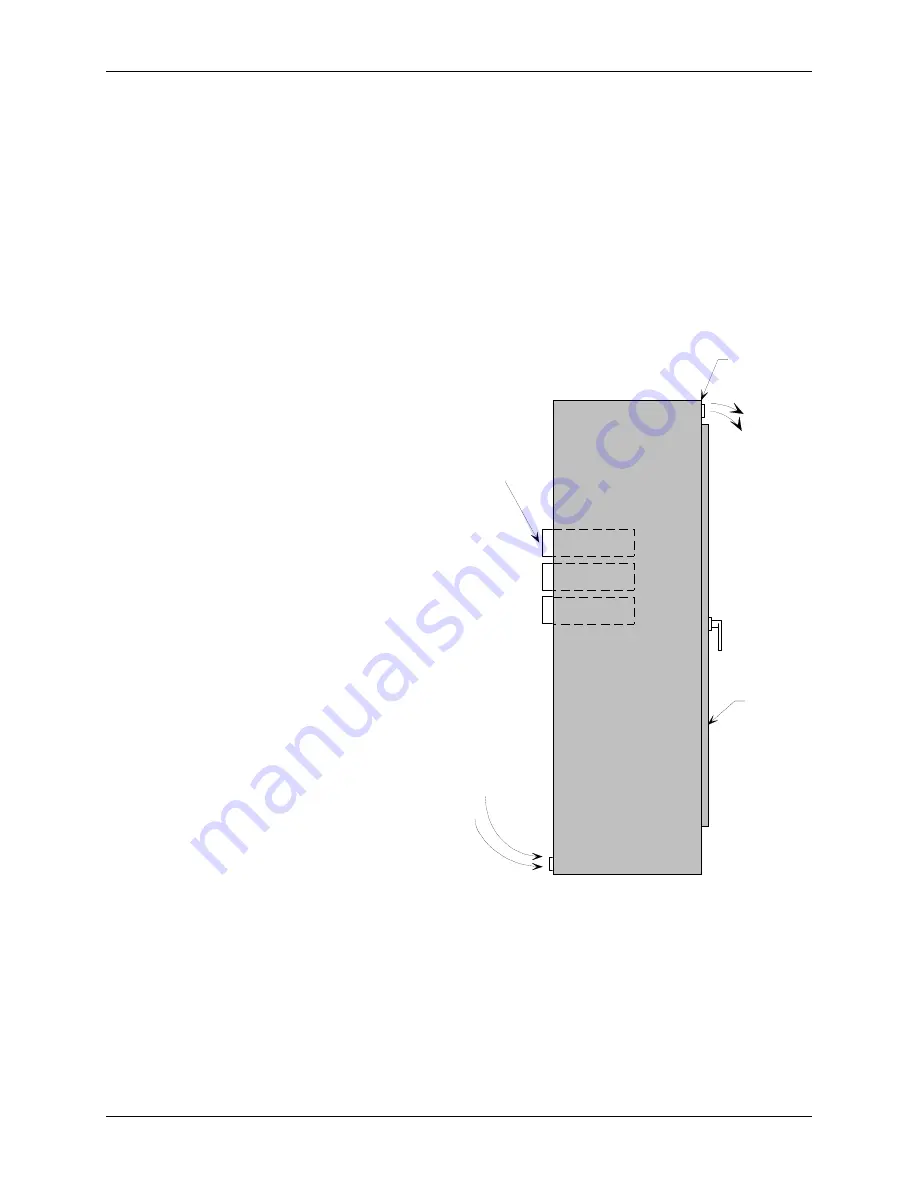
Installation
UM353-1
March
2003
8-2
TEMPERATURE
Keep the air surrounding an operating controller below 50
°
C (122
°
F). Check air temperature periodically to
ensure that this specification is not being exceeded.
CAUTION
Exceeding the specified operating temperature limits can adversely affect
performance and may cause damage to the controller.
Forced air ventilation is recommended when controllers are mounted in a partially or completely enclosed panel or
cabinet (e.g. NEMA 1); as shown at right. When clean air is present, exhaust fans are often mounted across the top
of a panel and louvers formed in the panel bottom. Air is then drawn upward between the station cases. When air
contains particulate matter, fans and filters are generally located at the panel bottom and louvers at the top. Filtered
air is now forced upward between the station cases. Filters must be serviced periodically.
Only high quality, quiet running fans should be used.
Also, the fans should not generate electrical noise
which could interfere with electronic instruments.
A sealed cabinet (e.g. NEMA 12 or 4X) containing
equipment that does not generate significant heat
should contain a recirculating fan for forcing air flow
around equipment and throughout the cabinet
preventing hot spots from developing. Forced air
conditioning may be required in very high density
panels or consoles. Periodically change or clean air
filters.
CONTAMINANTS
The controller case is slotted to permit circulation of
clean cooling air. Liquids and corrosive gases must
not be allowed to enter the case. Whether the
controller is in a control room or field mounted it must
be protected from rain, air conditioning condensate,
and plant and process related fluids and gases.
Extended exposure to contaminants can result in
malfunctions.
Industrial environments often contain airborne
particulate contaminants. Particulate matter, usually
dust and dirt, is abrasive and can cause intermittent
connections. A layer of dust on circuit boards can
interfere with component heat dissipation and can
absorb other airborne contaminants. Extended
exposure to these contaminants may result in
malfunctions.
Although 353 boards have a protective coating, the
following steps can reduce contaminant related
equipment malfunctions:
Forced Air Ventilation for Enclosed Panels
Instrument
Air Inlet
Enclosed
Panel
Air Outlet
Fan with
Finger
Guard
No. of Fans: One for each 16 stations or 3 ft. of panel width.
Air Inlet: 30 in² for each fan. If filters are used, they must
be changed periodically (increase inlet to 50 in²).
X03102S0
StockCheck.com
Summary of Contents for Moore 353
Page 2: ...S t o c k C h e c k c o m ...
Page 14: ...Contents UM353 1 xii March 2003 S t o c k C h e c k c o m ...
Page 24: ...Introduction UM353 1 March 2003 1 10 S t o c k C h e c k c o m ...
Page 152: ...LonWorks Communications UM353 1 March 2003 5 4 S t o c k C h e c k c o m ...
Page 164: ...Network Communications UM353 1 6 12 March 2003 S t o c k C h e c k c o m ...
Page 246: ...Operation UM353 1 March 2003 9 8 S t o c k C h e c k c o m ...
Page 254: ...Controller and System Test UM353 1 March 2003 10 8 S t o c k C h e c k c o m ...
Page 282: ...Circuit Description UM353 1 March 2003 13 4 S t o c k C h e c k c o m ...
Page 298: ...Model Designation and Specifications UM353 1 March 2003 14 16 S t o c k C h e c k c o m ...
Page 302: ...Abbreviations And Acronyms UM353 1 15 2 March 2003 S t o c k C h e c k c o m ...
Page 304: ...Warranty UM353 1 W 2 March 2003 S t o c k C h e c k c o m ...