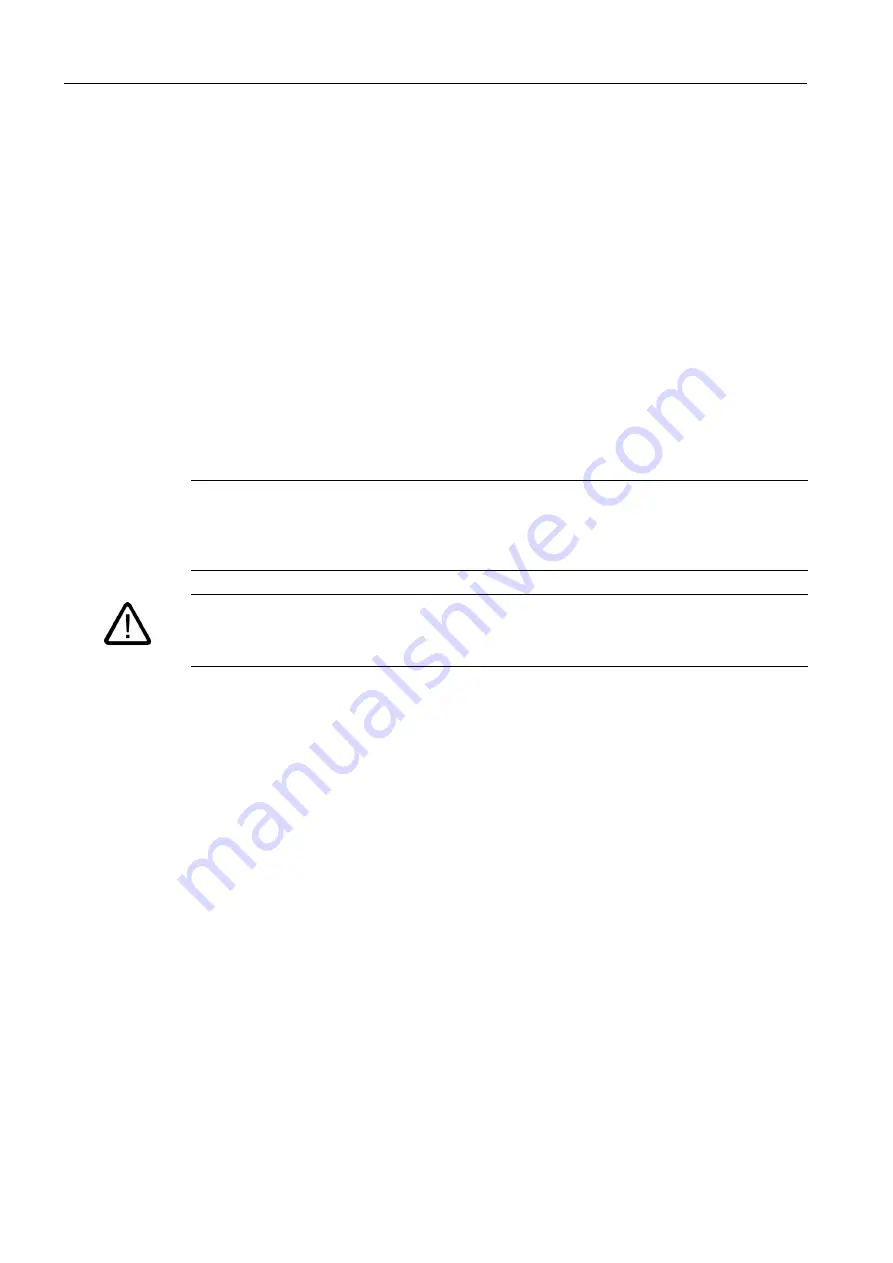
Motor Description
Armature short-circuit braking
1FK7 Synchronous Motors
1-12
Configuration Manual (PFK7), 10/2005 Edition, 6SN1197-0AD06-0BP1
1.6
Armature short-circuit braking
1.6.1
Description of functions
For transistor PWM converters, when the DC link voltage values are exceeded or if the elec-
tronics fails, then electrical braking is no longer possible. If the drive which is coasting down,
can represent a potential hazard, then the motor can be braked by short-circuiting the arma-
ture. Armature short-circuit braking should be initiated at the latest by the limit switch in the
traversing range of the feed axis.
The friction of the mechanical system and the switching times of the contactors must be taken
into account when determining the distance that the feed axis takes to come to a complete
stop. In order to avoid mechanical damage, mechanical stops should be located at the end of
the absolute traversing range.
For servomotors with integrated holding brake, the holding brake can be simultaneously
applied to create an additional braking torque – however, with some delay.
Caution
The drive converter pulses must first be canceled and this actually implemented before an
armature short-circuit contactor is closed or opened. This prevents the contactor contacts
from burning and eroding and destroying the drive converter.
Warning
The drive must always be operationally braked using the setpoint input. For additional infor-
mation, refer to the Drive Converter Configuration Manual.
Summary of Contents for MASTERDRIVES MC 1FK7
Page 1: ... VLPRGULYH PDVWHUGULYHV RQILJXUDWLRQ 0DQXDO GLWLRQ 6 QFKURQRXV 0RWRUV 6 02 5 9 0 67 5 5 9 6 0 ...
Page 2: ......
Page 164: ......
Page 165: ......