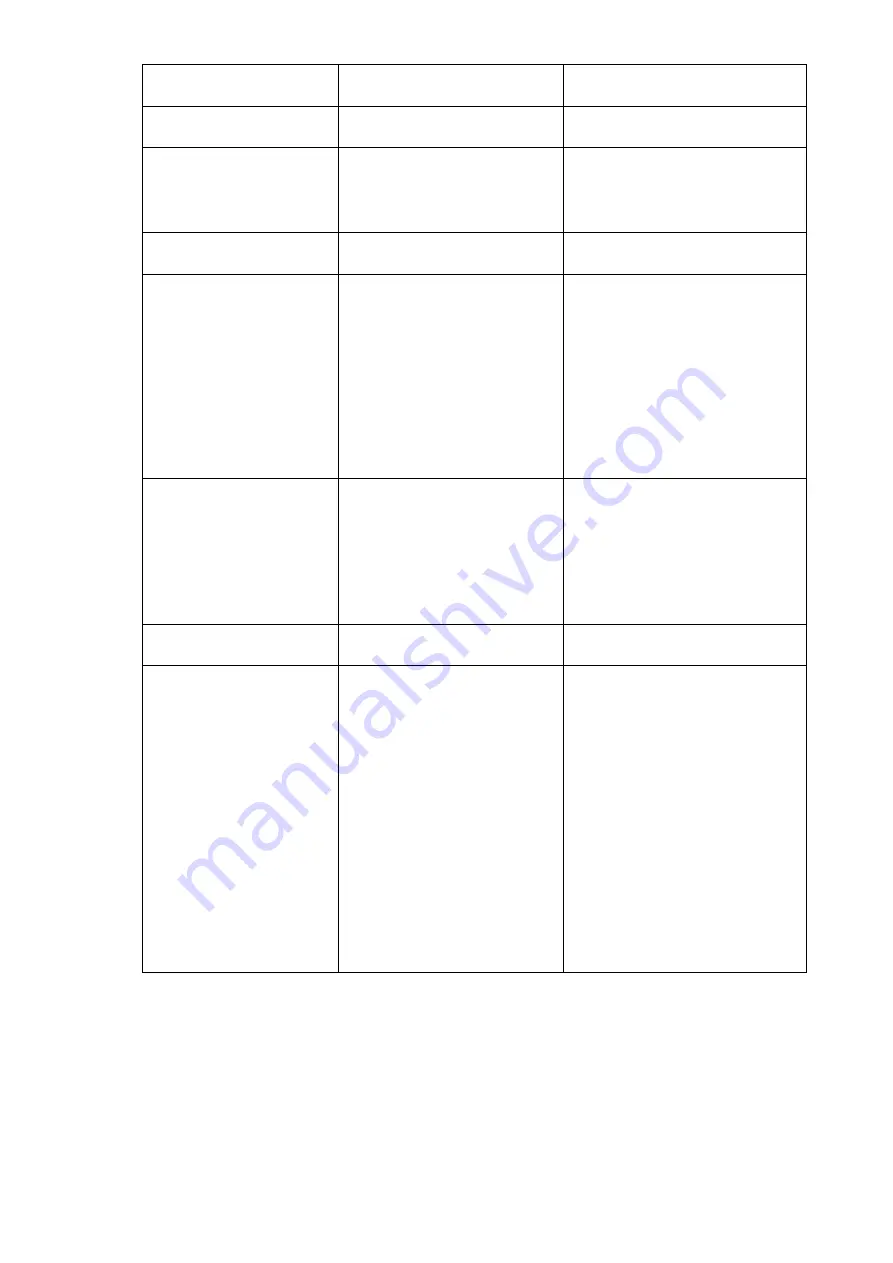
BA 5060 EN 04/2011
Faults
Remedy
Causes
Gear unit is oiled up.
Inadequate sealing of housing
covers and/or joints.
Seal joints.
Oil leakage from the gear unit.
Inadequate sealing of housing
covers and/or joints.
Radial shaftsealing rings
defective.
Check and, if necessary, replace
sealings. Seal joints.
Check radial shaftsealing rings and,
if necessary, replace.
Grease escaping at the
output shaft.
Radial shaftsealing rings
defective.
Check radial shaftsealing rings and,
if necessary, replace.
Oil foaming in the gear unit.
Preservation agent not completely
drained.
Gear unit too cold in operation.
Water in oil.
Oil too old
(defoaming agent used up).
Unsuitable oils mixed up.
Oil change.
Shut down gear unit and have oil
degassed. Restart without cooling
water.
Test the oil, change oil if necessary.
Test the oil, change oil if necessary.
Test the oil, change oil if necessary.
Oil foams in sump.
Water in oil.
Gear unit exposed to cold air from
machineroom ventilator: Water
condensing.
Protect gear unit with suitable heat
insulation. Close air outlet or alter its
direction by structural measures.
Wetair filter changes colour
from top to bottom.
Water in oil.
Contact Customer Service.
- Change oil.
Increased operating
temperature.
Oil level in housing too high.
Oil too old.
Oil badly contaminated.
Seriously contaminated oil filter.
Oil pump defective.
On gear units with fan: Suction
opening in airguide cover and/or
gearunit housing badly
contaminated.
Check oil level and, if necessary,
adjust.
Contact Customer Service.
- Check date of last oil change.
Contact Customer Service.
- Change oil.
Clean the oil filter.
Contact Customer Service.
- Check that oil pump is functioning
correctly.
- Repair or replace oil pump.
Clean airguide cover and gearunit
housing.