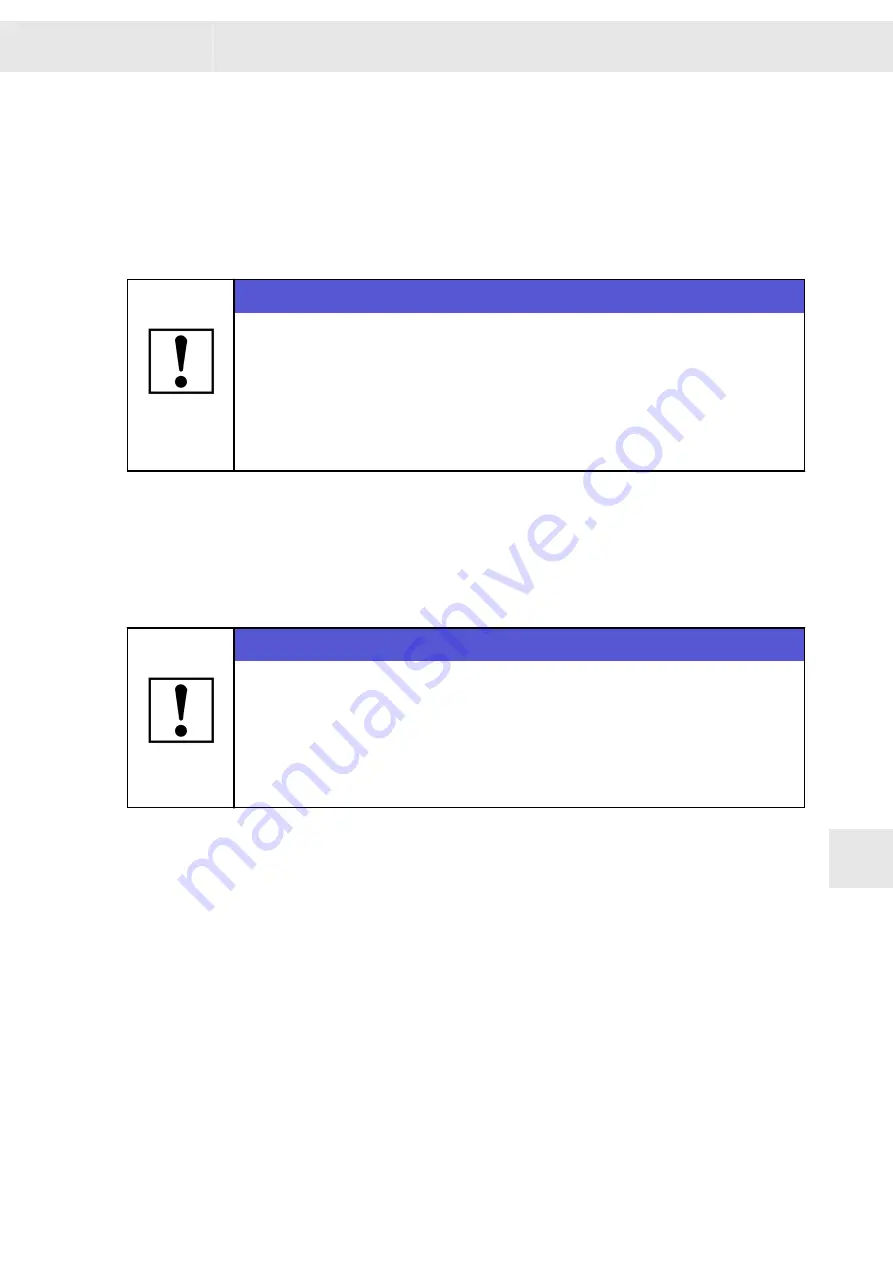
12
General Information Regarding the
Wiring
12.1
Mains Connection
NOTICE
Property damage due to incorrect mains connection
Direct connection to ungrounded / asymmetrically grounded mains (IT mains with
start point / IT delta mains) can destroy the devices.
Connecting the device to this mains type is only possible with isolating transformer.
Also consider the manual "Unit Assembly Complying to EMC", chapter "Connec‐
tion to Different Supply System Types".
12.2
Cable Requirements
The cables described in this chapter meet the SIEB & MEYER requirements to cables
and connectors in order to ensure their proper function.
NOTICE
Risk of cable damage due to mechanical loads
Cables that are exposed to mechanical loads, e.g. trailing chains or similar, must
be suited for this purpose. Otherwise, damage may occur. SIEB & MEYER cables
are not suitable for trailing chains!
The machine manufacturer must ensure that only cables are used that are suitable
for this purpose.
In general, the following principles apply for the cables (see also documentation “Unit
Assembly Complying EMC”)
▶
Motor and signal cables must not be wired in the same cable protection hose!
▶
Motor cables must have a wire-meshed shield. They must be wired separately
from signal cables.
▶
Signal lines must have a wire-meshed shield. Differential signals should only be
transmitted with twisted-pair lines. They must be wired separately from motor
cables.
▶
The cable shields must be connected to the connector shell inside of the connec‐
tors. In the switch cabinet they should be connected to a ground bus.
▶
Cable shields not ending in a connector inside of the switch cabinet such as motor
cables must be connected to the ground bus.
▶
Both ends of the shield of shielded cables must generally be connected to the
shell.
The line cross-sections should be selected carefully: The maximum admissible current
should not be exceeded at the maximum ambient temperature (see technical data).
DIN VDE 0298-4 defines the admissible values for the individual line cross-sections
which must absolutely be taken into account.
W
General Information Regarding the Wiring
Drive System SD3 - Hardware Description
71
12
Summary of Contents for Drive System SD3 Series
Page 1: ...Drive System SD3 Hardware Description P TD 0000486 3 2017 03 30 SIEB MEYER W...
Page 4: ...Chapter Overview W 4 Drive System SD3 Hardware Description...
Page 8: ...Content W 8 Drive System SD3 Hardware Description...
Page 20: ...Safety Instructions W 20 Drive System SD3 Hardware Description 3...
Page 22: ...Unit Assembly Complying EMC W 22 Drive System SD3 Hardware Description 4...
Page 28: ...Description of the Device W 28 Drive System SD3 Hardware Description 5...
Page 60: ...9 3 X19 Encoder 1 Connection Examples W 60 Drive System SD3 Hardware Description 9...
Page 66: ...Connection Examples W 66 Drive System SD3 Hardware Description 9...
Page 68: ...Status Display and Error Messages W 68 Drive System SD3 Hardware Description 10...
Page 70: ...Battery Change W 70 Drive System SD3 Hardware Description 11...
Page 76: ...General Information Regarding the Wiring W 76 Drive System SD3 Hardware Description 12...
Page 82: ...Safety Circuit Restart Lock STO W 82 Drive System SD3 Hardware Description 13...