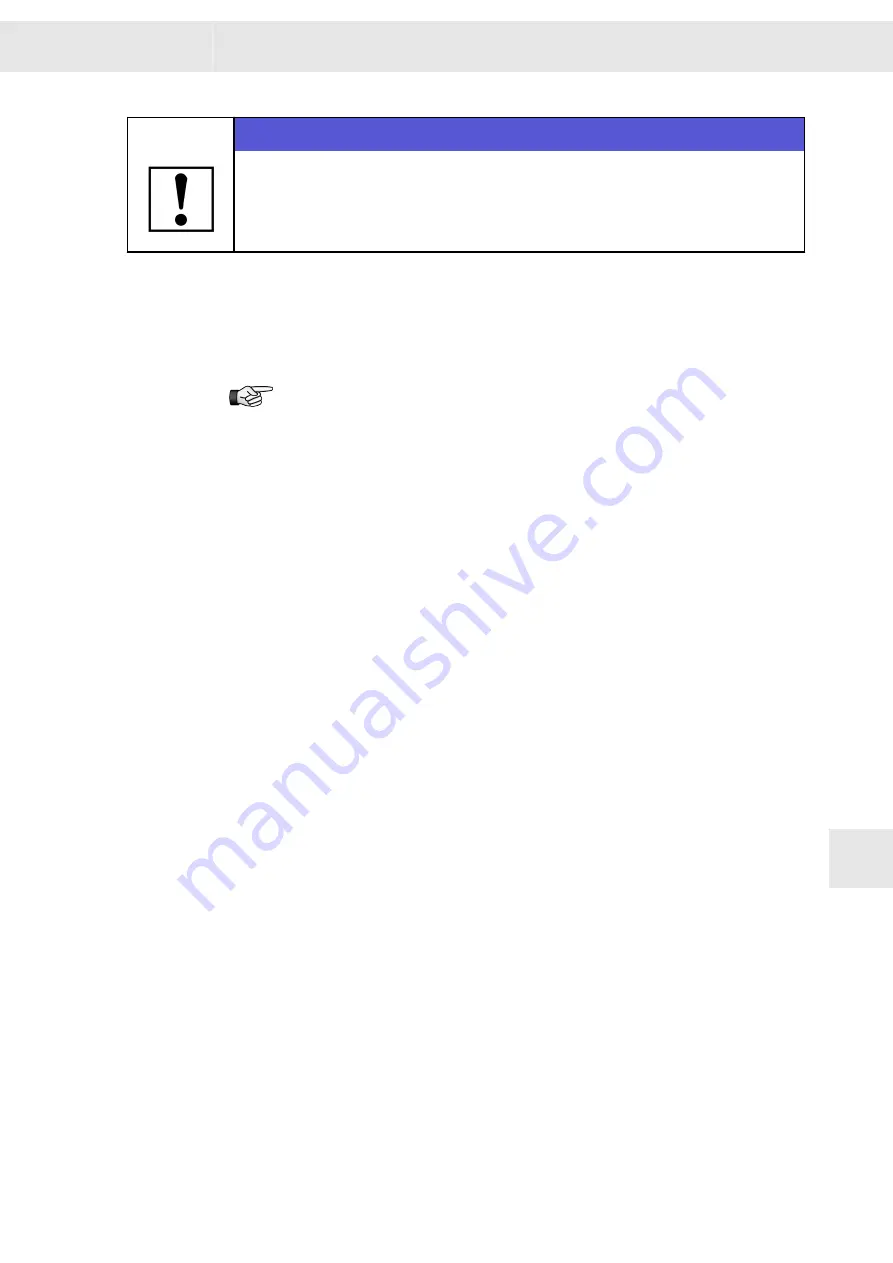
NOTICE
Ungrounded test setups
So-called "flying test systems" that are not or not sufficiently grounded can cause
damage to the communication interfaces or to the connected devices.
USB
The USB cable must have a maximum length of 5 m according to the USB regulations.
We recommend high-quality cables with integrated ferrite cores (available at
SIEB & MEYER).
Trouble-free USB communication is also highly dependent on the quality of
the USB interface at the used PC/laptop.
RJ45
Use only high-quality RJ45 cables.
Low priced RJ45 cables can damage the female RJ45 connector. The dimensions of
the cable connectors deviate frequently from the standard dimensions. Thus, they
cause problems with the electrical contact after only few connecting cycles.
12.2.3
Cables for the Rotor Position Detection
Use shielded lines and shielded Submin D shells for wiring the different measuring
systems. The shield must be connected to the Submin D shell at the servo module side
and to the housing of the measuring system.
Examples for the use of conductors:
▶
Motors with resolver
LIYCY 3 x 2 x 0.14 or 4 x 2 x 0.14 for motors with integrated thermal contact.
Conductors: shielded, twisted in pairs. Twist mode: sine/sine, cosine/cosine, rotor/
rotor and, if necessary, thermal contact/thermal contact.
For delicate applications we recommend to additionally shield the separate pairs.
▶
Motors with incremental encoder
LIYCY 5 x 0.14 or 7 x 0.14 for motors with integrated thermal contact.
▶
Motors with Hall effect sensors and tachometer generator
LIYCY 9 x 0.14 or 12 x 0.14 for motors with integrated thermal contact.
12.2.4
Cables for the External Ballast Resistor
The cables of the external ballast resistor of R
EX
and +UB must be twisted. If the cable
is longer than 20 cm, you must use a shielded cable.
W
General Information Regarding the Wiring
Drive System SD3 - Hardware Description
75
12
Summary of Contents for Drive System SD3 Series
Page 1: ...Drive System SD3 Hardware Description P TD 0000486 3 2017 03 30 SIEB MEYER W...
Page 4: ...Chapter Overview W 4 Drive System SD3 Hardware Description...
Page 8: ...Content W 8 Drive System SD3 Hardware Description...
Page 20: ...Safety Instructions W 20 Drive System SD3 Hardware Description 3...
Page 22: ...Unit Assembly Complying EMC W 22 Drive System SD3 Hardware Description 4...
Page 28: ...Description of the Device W 28 Drive System SD3 Hardware Description 5...
Page 60: ...9 3 X19 Encoder 1 Connection Examples W 60 Drive System SD3 Hardware Description 9...
Page 66: ...Connection Examples W 66 Drive System SD3 Hardware Description 9...
Page 68: ...Status Display and Error Messages W 68 Drive System SD3 Hardware Description 10...
Page 70: ...Battery Change W 70 Drive System SD3 Hardware Description 11...
Page 76: ...General Information Regarding the Wiring W 76 Drive System SD3 Hardware Description 12...
Page 82: ...Safety Circuit Restart Lock STO W 82 Drive System SD3 Hardware Description 13...