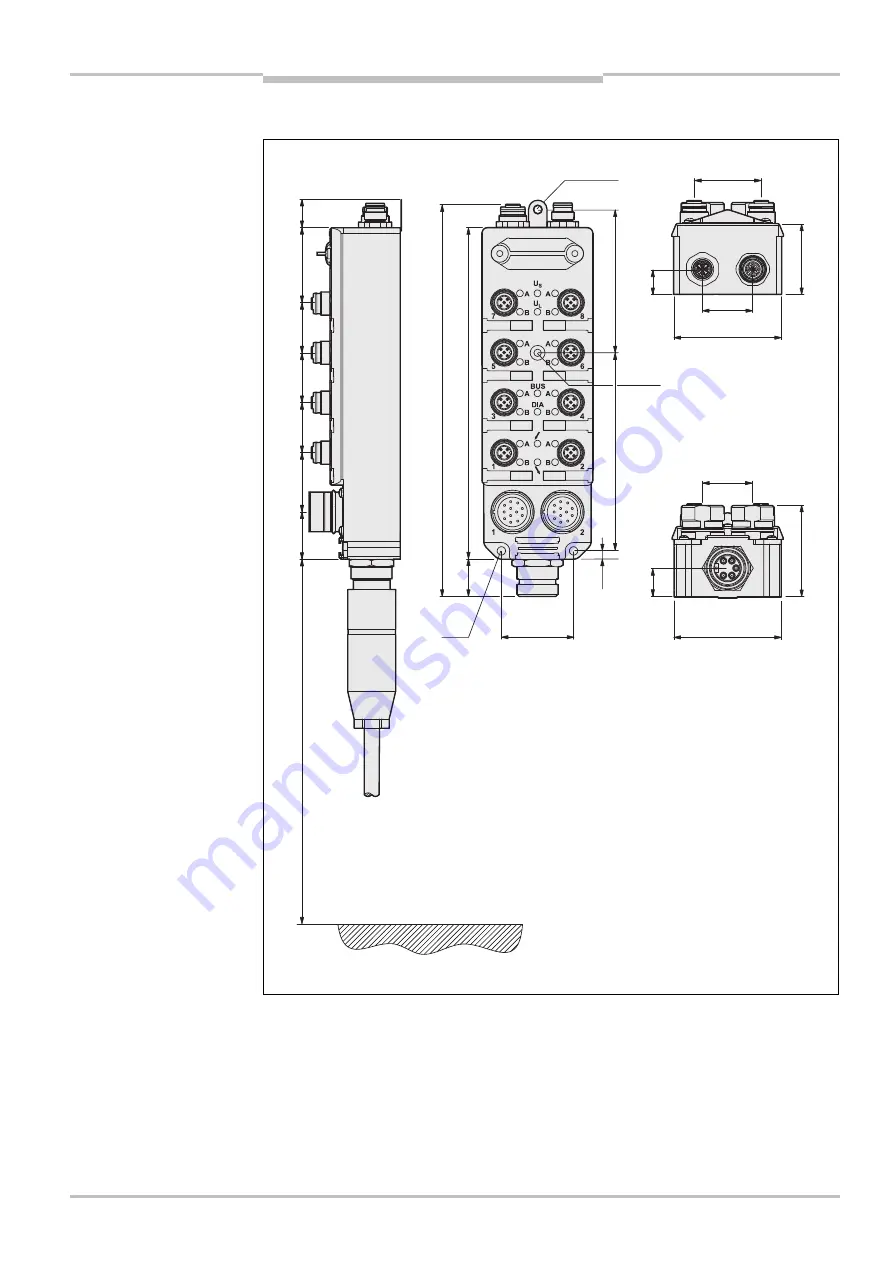
Operating Instructions
Chapter
10
UE4155
8010178/TF82/2010-03-05
© SICK AG • Industrial Safety Systems • Germany • All rights reserved
61
Subject to change without notice
Technical specifications
10.5
Dimensional drawing bus node UE4155
Fig. 16: Dimensional drawing
bus node UE4155 (mm)
1
0
7
39
36
1
7
9
2
1
1
.6
3
2
4
9
.3
2
7
2
7
2
7
4
0
.5
1
4
2
5
.5
4
.5
2
0
.1
7
7
27
27
60
60
3
8
1
3
.5
1
5
.5
5.1
4.5
4
C
on
ne
ct
or
ra
ng
e
ca
.1
2
5