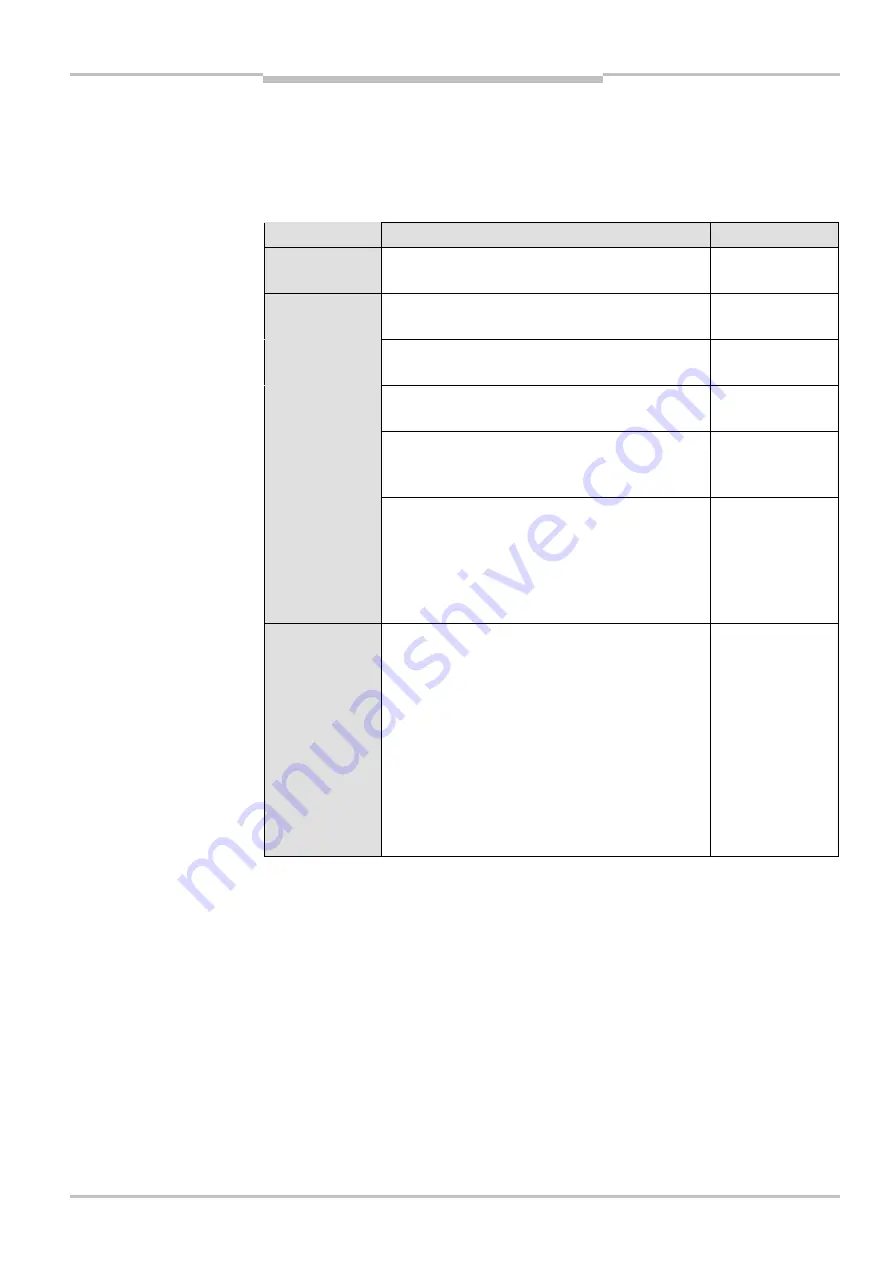
Operating Instructions
Chapter
8
UE4155
8010178/TF82/2010-03-05
© SICK AG • Industrial Safety Systems • Germany • All rights reserved
41
Subject to change without notice
Configuration
8.3.4
Carrying out the PROFIsafe configuration in the FPLC hardware-configuration
program
The parameters to be set depend on the connected field device. If necessary, you must
modify the values for the bus node preassigned by the hardware-configuration program.
General parameters for the PROFIsafe configuration are:
Parameter
Meaning
Setting
F_Check_SeqNr
Influences the consistency check
(CRC calculation) of the PROFIsafe telegram
Check/No check
F_SIL
Bus-node safety class (SIL1 to SIL3)
Depending on
application
F_CRC_Length
Anticipated length of the CRC checksum in the
PROFIsafe telegram
2 Byte CRC
F_Par_Version
Implemented PROFIsafe version. You cannot
change this parameter.
0
F_Source_Add
PROFIsafe source address. Must be unique in
combination with the PROFIsafe destination
address and is assigned automatically
1 to 65 534
F_Dest_Add
PROFIsafe destination address. Must be unique in
combination with the PROFIsafe source address
and is assigned automatically. Note: The
PROFIsafe address of the bus node must
correspond to this value (see chapter 8.6 on
page 45).
1 to 65 534
F_WD_Time
Monitoring time (“Watchdog time”) for the cyclic
service. If no valid PROFIsafe telegram is
exchanged between the bus node and the FPLC
within the set monitoring time, both will proceed
to the safe status, i.e. they assign themselves
failsafe values.
The monitoring time should be sufficiently long to
tolerate minor delays in communication. In the
event of an error, however, it must not unneces-
sarily delay the system response of the bus node
or that of the FPLC.
Depending on the
application from
1 to 65 535 ms
Invoke the FPLC safety program cyclically and with the highest priority. In this way you will
prevent the overall response time from becoming longer.
The planning manuals of the PROFIBUS manager and the PROFIsafe profile that you have
deployed contain more information on the definition and mode of operation of the
PROFIsafe parameters.
4)
The setting depends on the FPLC being used. The setting for a Siemens FPLC must be “No check” here.
Tab. 11: PROFIsafe
parameters to be set
Recommendation