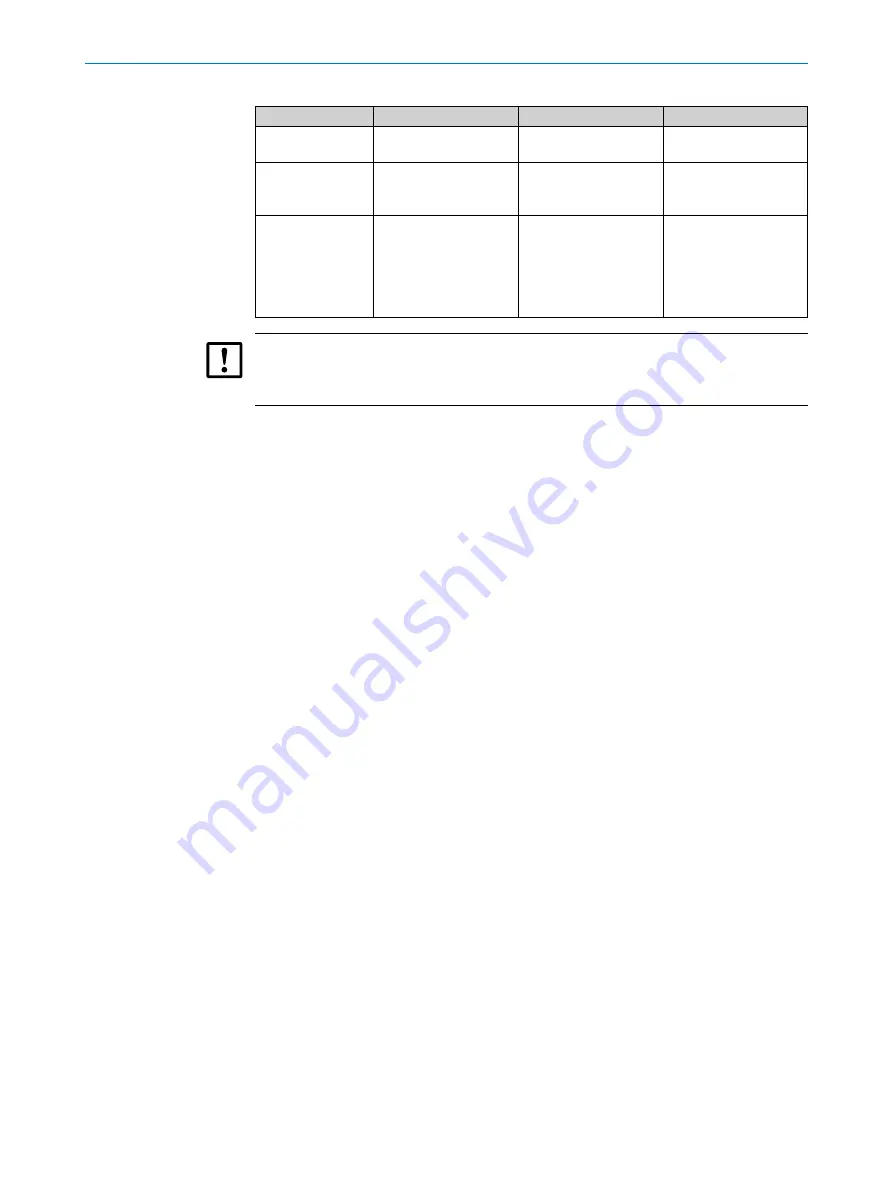
O P E R A T I N G I N S T R U C T I O N S | T - E A S I C
®
8023072/1E22/2022-02-23 | SICK AG
Subject to change without notice
2 6
7
COMMISSIONING
LED
Status on
Status off
Status flashing
PWR
Supply voltage is on
Supply voltage is not on Flashes during IO-Link
communication
S1
Switching output Q1
active
Switching output Q1
inactive
Device in error state
(see displayed mes-
sage)
S2
Switching output Q2
active or High signal
applied at switching
input Q2
Switching output Q2
inactive or Low signal
applied at switching
input Q2 or pulse
output active or analog
output active
Device in error
state (see displayed
message)
IMPORTANT
If the device is in the error state, S1 and S2 flash simultaneously (check displayed
message).
7.2.4
IO-Link
To operate the device via IO-Link, an IODD file, function blocks for common PLCs,
and a description of the available telegram parameters can be downloaded from
7.3
Measurement configuration
The sensor can be configured by means of various measurement parameters.
First of all, you need specify whether the sensor is to be operated in
Velocity
(relative
or
absolute
) or
Volume
( volume flow
or
counter
) mode, or whether it is to be taught-in
(Teach
).
Secondly, you can select from three different medium options (water, oil A, oil B).
There are several ways to configure
Measurement Mode
:
−
Velocity relative (%)
: The velocity is displayed as a percentage of the full scale
value.
−
Velocity absolute
: The velocity is displayed as an absolute measured value in the
unit selected for
Unit Velocity
(see
).
−
Volume flow:
The volume flow is displayed as an absolute measured value in the
unit selected for
Unit Volume Flow
(see
−
Volume counter
: The volume counter is displayed as an absolute measured value
in the unit selected for
Unit Volume
). If this measurement
mode is set, there is an option in the display to reset the volume counter (Reset
Volume). The volume counter is automatically reset each time the device is restart-
ed. To output the volume counter, pulse output must be selected in Q2.
−
Teach relative (%)
: If the medium to be measured differs from the available preset
media (water, oil A or oil B), a teach-in operation can be performed to optimize
the performance of the sensor. The flow rate is then displayed as a percentage
of the flow range between the taught-in maximum and minimum flow. The sensor
gives you the option to teach-in three different media and to store them in the sen-
“Configuring the measurement mode based on the “Teach relative”
).