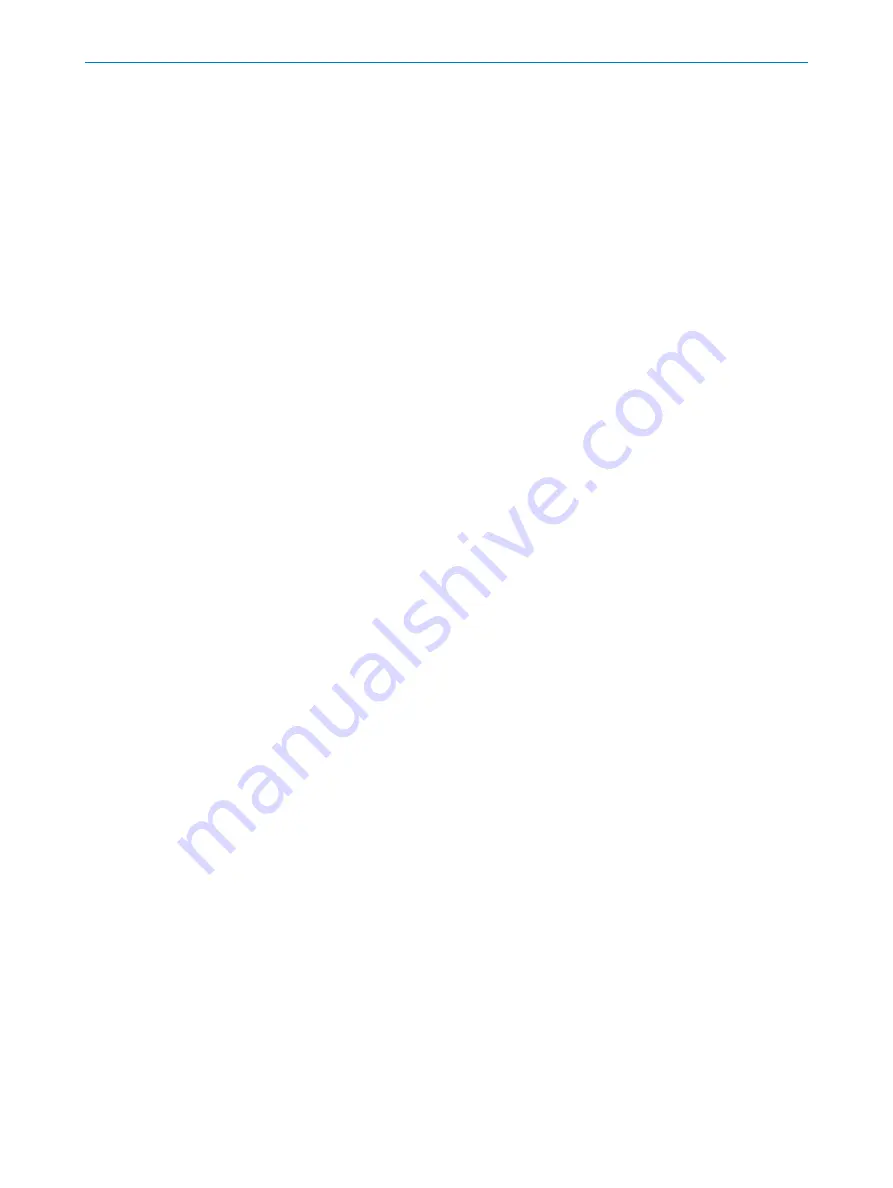
5.6.5.1
Removing the transport safety device of the
GMP measuring probe............................................
5.6.5.2
Removing the transport safety device of the GPP
measuring probe.....................................................
5.6.6
Fitting the measuring probe on the flange with tube............
5.6.7
Putting the purge air unit into operation................................
5.6.8
Fitting the flange fixture on the measuring probe.................
5.6.9
Fitting the control unit.............................................................
5.6.9.1
Fitting the control unit at a greater distance
(option)....................................................................
6
Electrical installation........................................................................ 31
6.1
6.2
6.3
Overview of electrical connection steps..................................................
6.4
Connection overview................................................................................
6.4.1
Lines overview.......................................................................... 34
6.4.2
Laying lines..............................................................................
6.5
Electrical connection of the control unit.................................................
6.5.1
Correct connection of the CAN bus line.................................
6.5.2
Connecting the control unit electrically..................................
6.5.3
Connecting the grounding conductor on the control unit.....
6.6
Connecting the connection unit (option).................................................
7
Commissioning.................................................................................. 40
7.1
7.2
7.3
7.4
Material required......................................................................................
7.5
Commissioning steps overview................................................................
7.6
Removing the transport safety device of the sender/receiver unit.......
7.7
Fitting the sender/receiver unit on the flange fixture............................
7.8
Connecting the sender/receiver unit with measuring probe.................
7.9
Fine optical alignment..............................................................................
7.10 Fitting the weather hood (option)............................................................
7.11 Starting measuring operation..................................................................
7.11.1
Operating states......................................................................
8
Operation............................................................................................ 47
8.1
Operating and display elements..............................................................
8.2
Control unit menu tree.............................................................................
8.2.1
Menu tree, Measuring.............................................................
8.2.2
Menu tree, Diagnosis..............................................................
8.2.3
Menu tree, Parameters...........................................................
8.2.4
Menu tree, Calibration.............................................................
8.2.5
Menu tree, Maintenance.........................................................
CONTENTS
4
O P E R A T I N G I N S T R U C T I O N S | GM35
8009389/147I/V4-0/2021-03 | SICK
Subject to change without notice