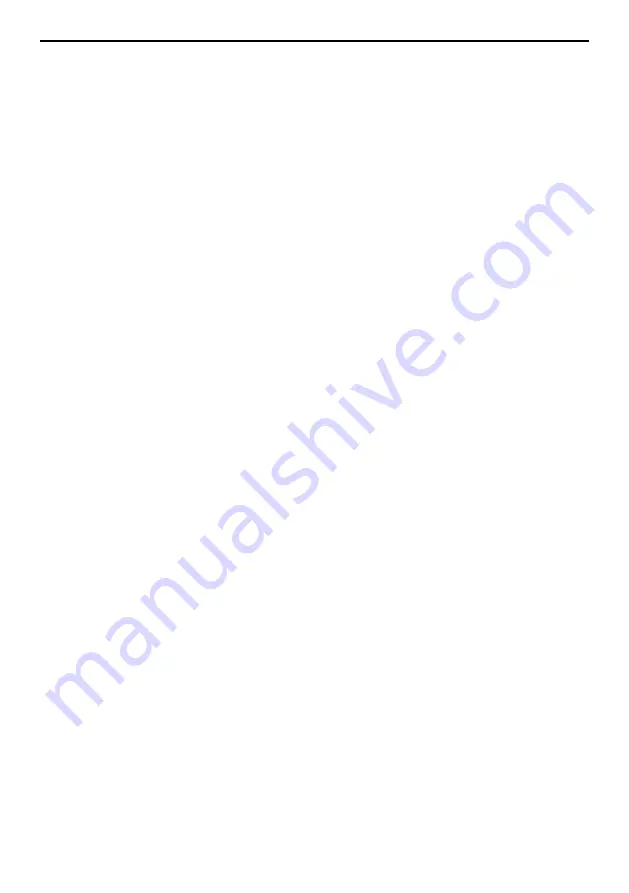
Automatic well sounder “DUA-1”
18
2.5.8. Testing the product
When the power is turned on, the product performs a self-diagnosis
and may detect malfunctions. At the same time, the "Power" LED starts
flashing red (if no malfunction is detected, the LED lights up green). The
number of flashes per second equals the fault number. After ten seconds,
the flashing cycle is repeated.
1 - loss of setting factors. At short pressing of the power button, the
setting factors (sensitivity of the pressure sensor, etc.) are filled with the
initial values. Usually this malfunction is displayed at the factory when the
product is put into operation for the first time;
2 - ferromagnetic memory malfunction;
3 - analog-to-digital converter malfunction;
4 - no response from the radio channel module;
5 - clock fault;
6 - clock malfunction;
7 - flash memory malfunction.
When highlighting faults 2, 3, 4, 6, 7, send the product for repair.
2.6. Well sounder disassembly
Turn off the device.
Close the gate valve of the technological branch.
Open the device outlet valve and bleed excess pressure from the
working volume.
Unscrew the product and remove it from the branch pipe. Drain the
condensate from the working volume, clean the threaded part and put the
product in a regular bag.
Close the branch pipe with the technological plug.