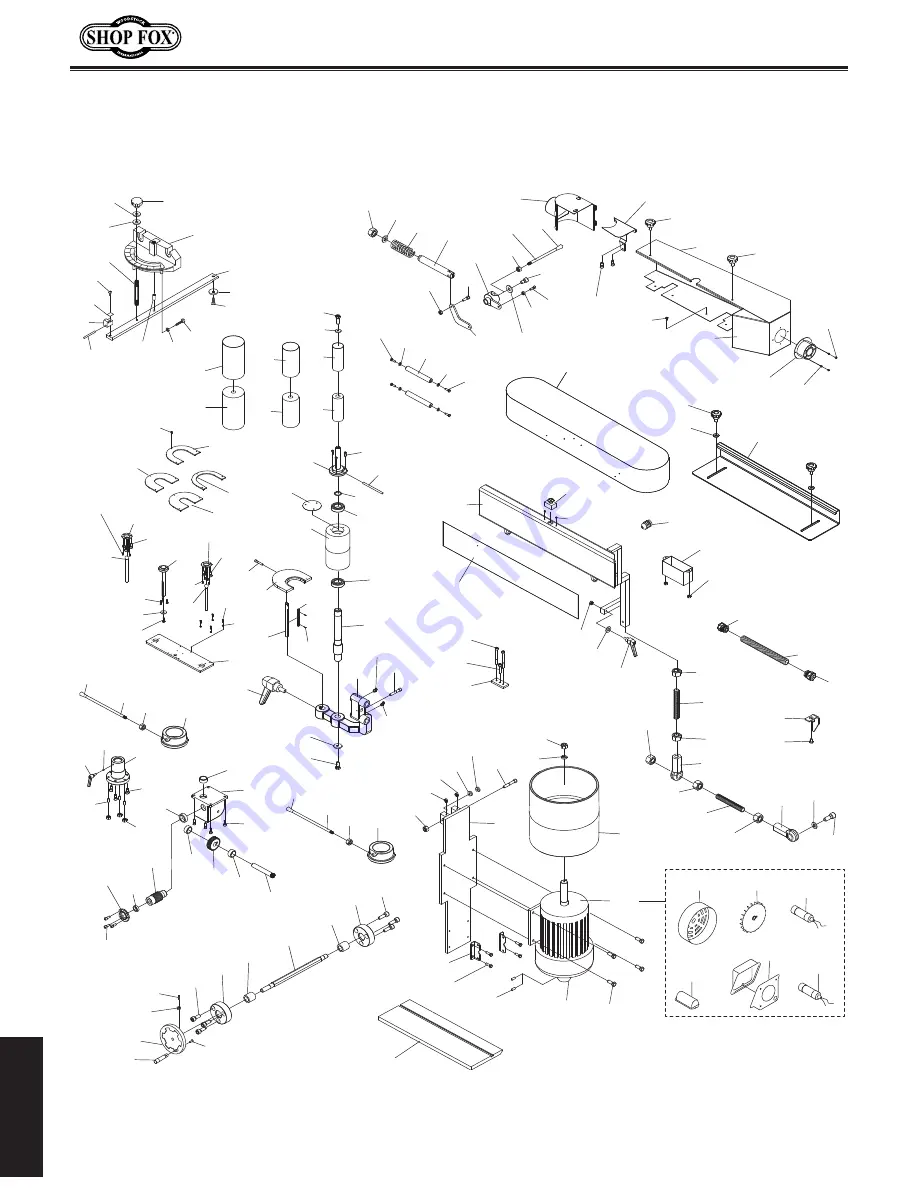
-38-
Model W1845 (For Machines Mfd. Since 6/17)
PA
RT
S
57
163
164
34
31
40
104
32
52
138
33
105
99
36
100
112
30
31
92
163
109
116
34
29
113
111
114
195
110
106
107
108
170
101
102
186
35
166
117 116
115
106
119
120
107
170
195
191
100
121
118
169
102
93
186
103
35
162
92
165
161
167
41
39
38
42
62
59
61
64
168
60
58
170
169
68
85
149
108
66
141
138
172 175
171
37
168
159
150
47
66
151
148
27
78
139
146
147
142
143
144
86
87
84
177
49
25
173
190
189
190
173
174
179
178
180
181
188
176
155
154
179
182 187
185
184
180
186
183
56
109
67
82
84
84
83
83 81
65
84
82
84
152
70
100
65
156
157
157-1
153
145
10
160
156
53
46
147-2
147-1
147-4
147-3
147-6
147-5
90
75
60
45
30
30
45
60
75
24
10
11
12
13
14
15
16
17 18
19
20
21
22
23
140
66
66
159
55
187
156
77
199
201
201-1
200
PARTS
Sanding.Head/Table
Summary of Contents for W1845
Page 45: ...Model W1845 For Machines Mfd Since 6 17...
Page 48: ......