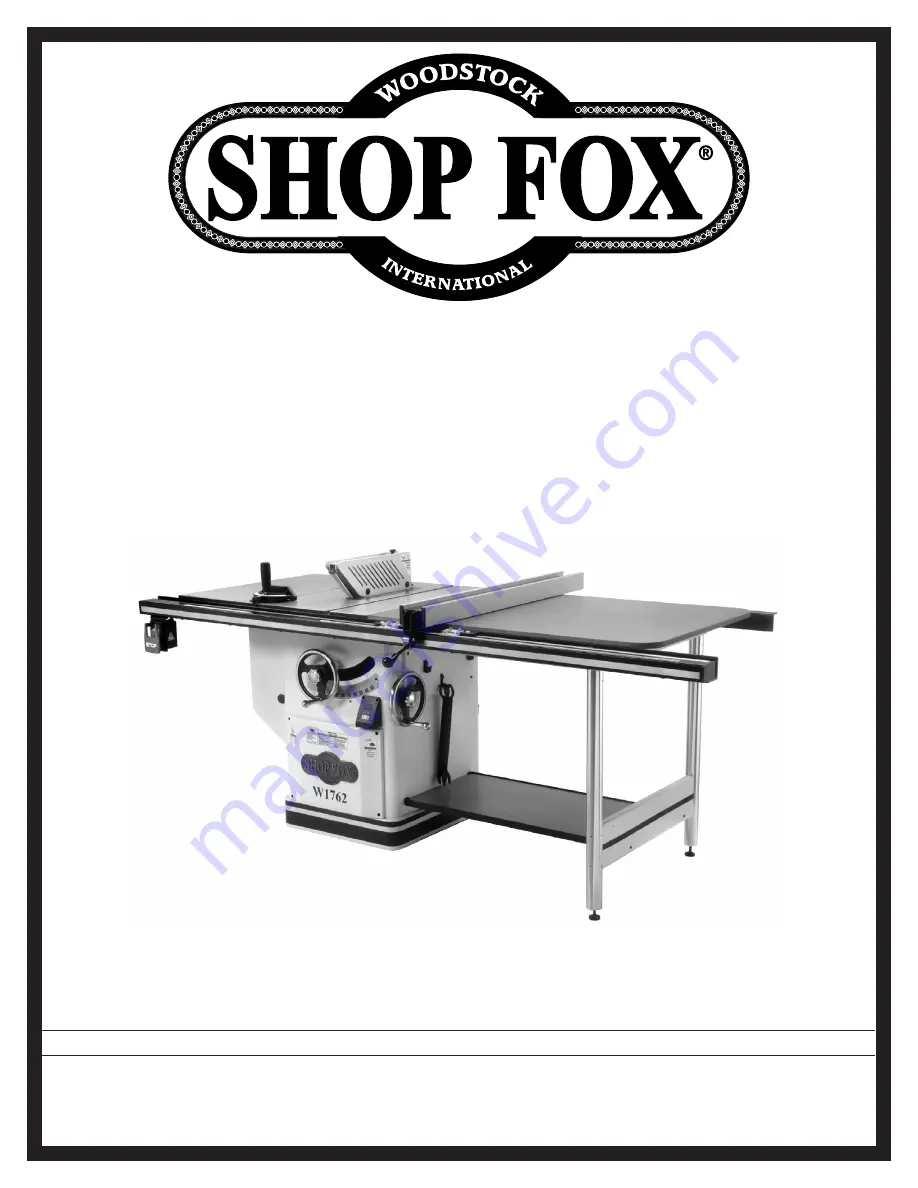
OWNER'S MANUAL
MODEL W1761/W1762
12" TABLE SAW WITH
RIVING KNIFE
Phone: (360) 734-3482 • Online Technical Support: [email protected]
COPYRIGHT © SEPTEMBER, 2007 BY WOODSTOCK INTERNATIONAL, INC.
WARNING: NO PORTION OF THIS MANUAL MAY BE REPRODUCED IN ANY SHAPE OR FORM WITHOUT
THE WRITTEN APPROVAL OF WOODSTOCK INTERNATIONAL, INC.
Printed in Taiwan
#9077BL
Summary of Contents for W1761
Page 14: ......
Page 17: ...3 W1761 W1762 12 Table Saw with Riving Knife INTRODUCTION...
Page 18: ...4 W1761 W1762 12 Table Saw with Riving Knife INTRODUCTION...
Page 77: ...63 W1761 W1762 12 Table Saw with Riving Knife PARTS Main Table Motor Cabinet...
Page 83: ......
Page 84: ......
Page 87: ......
Page 88: ......