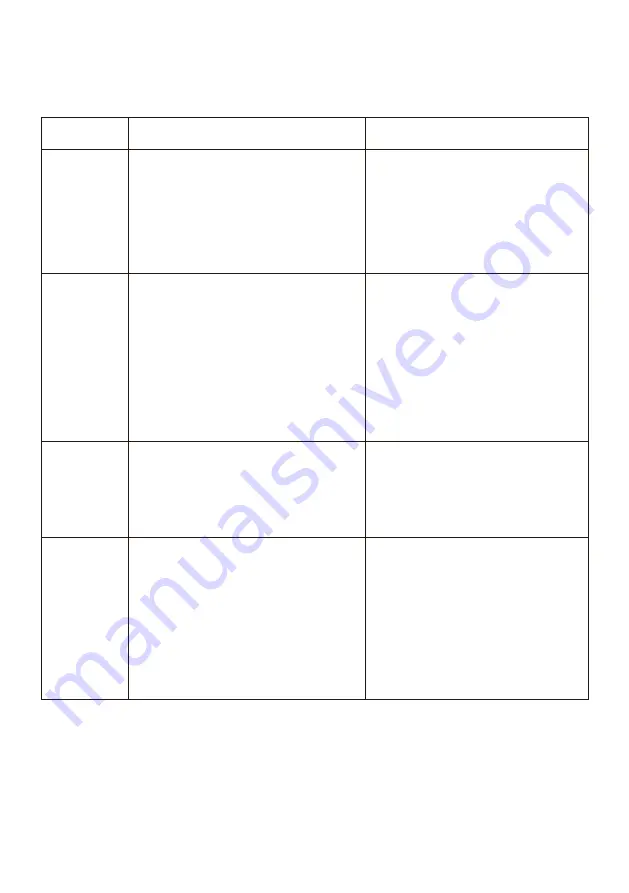
VI. Troubleshooting
Fault
Difficulty in
starting
Causes
Remedy
1. The supply voltage is too low
2. Phase loss
3. The impeller is jammed
4. The voltage drop of cable is too
large
5. Stator winding is burnt out
1. Adjust the voltage to ±10% of the
rated value
2. Check switch outlet and cable
and plug
3. Fix the jammed part
4. Select and use reasonable cable
5. Insert winding again for overhaul
Low water
output
1. The lift is too large
2. The mesh enclosure is blocked
3. The impeller is worn seriously
4. The immersion depth of electric
pump is shallow, with air sucked
5. The impeller reverses
1. Use the pump within the usable
range of lift
2. Clear away water plants and
other foreign matters
3. Replace the impeller
4. Adjust the immersion depth of
electric pump, which shall not be
less than 0.5m
5. Exchange any two of the three
phases
Stop running
suddenly
1. Switch is off, or fuse is burnt out
2. The impeller is jammed
3. Stator winding is burnt out
1. Check whether the lift used or
supply voltage meets
requirements and adjust it
2. Clear away foreign matters
3. Insert winding again for overhaul
Stator
winding is
burnt out
1. Phase loss occurs to electric pump
or the running time is too long
2. Water leaks due to damage of
mechanical seal, resulting in
turn-to-turn or phase-to-phase
short circuit
3. The impeller is jammed
4. Electric pump starts up frequently
or runs out of water too long
5. Electric pump is overloaded
Eliminate the faults, remove the
winding and insert the winding
again according to the original
technical requirements, and apply
insulating paint by impregnating
and drying, or send it to the
maintenance company for repair
Notes:
1. All the figures in this manual are schematic diagrams, and please understand that the
electric pumps and accessories you buy may be different from the diagrams in this manual.
2. The performance of the product is improved constantly, and all products (including
appearance and color, etc.) are subject to physical products; no further notice will be given
in case of any change.