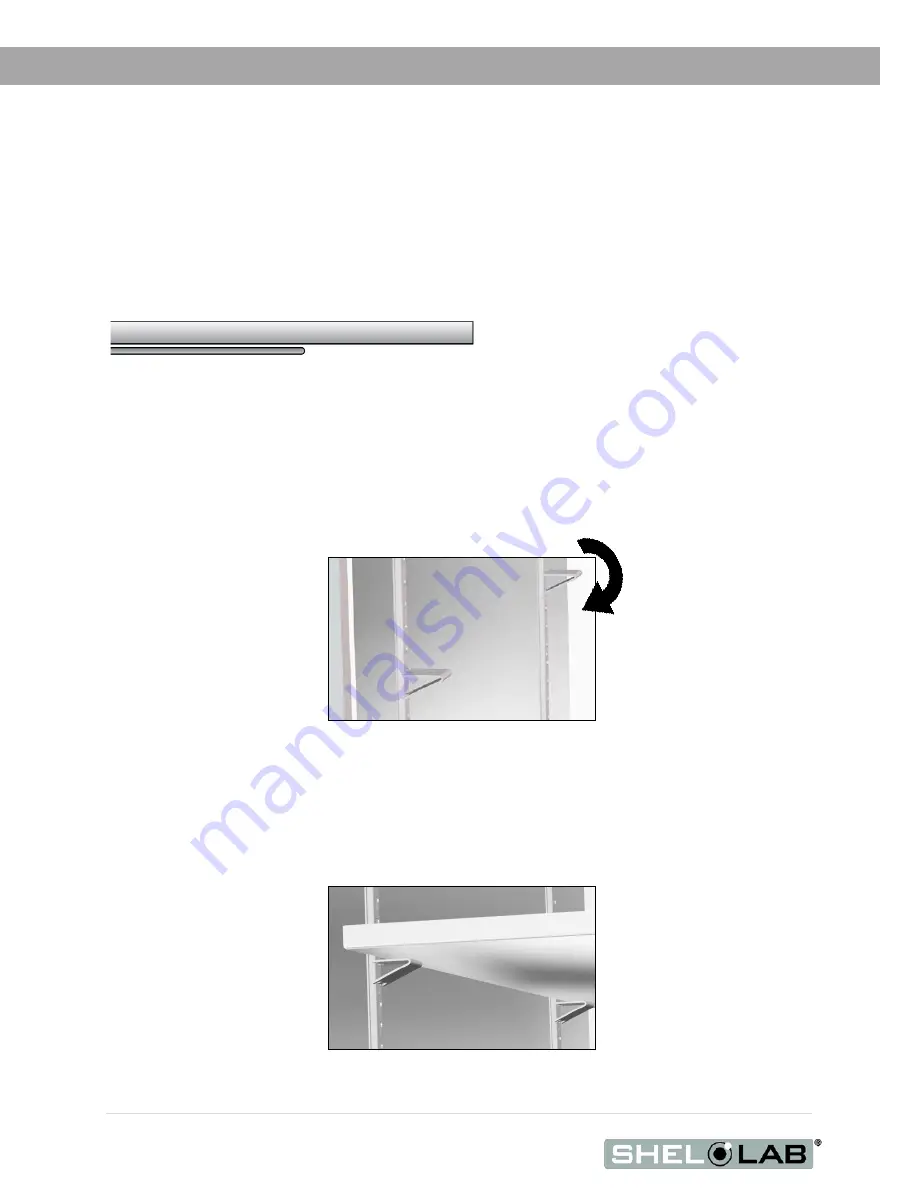
18 |
P a g e
INSTALLATION
I
NSTALL THE
S
HELVING
To ensure accurate temperature measurement,
one shelf bottom must be in close proximity to the
oven temperature probe
extending out from the chamber back wall. Do not place the shelf in direct
contact with the probe.
1.
Install the shelf clips in the slots of the shelf standard mounting rails located on the sides of
the chamber interior, four clips (4) per shelf.
a.
Squeeze each clip, insert the top tab first, and then the bottom tab using a
rocking motion.
2.
Set the shelves on the clips.
a.
Make sure the shelves are level.
Installing Shelf Clips
Rocking Motion
Probe
Shelf
Summary of Contents for SVAC9-2
Page 1: ...Installation Operation Manual SVAC9 2 Vacuum Oven 230 Voltage...
Page 8: ...8 P a g e INTRODUCTION...
Page 12: ...12 P a g e RECEIVING...
Page 22: ...22 P a g e GRAPHIC SYMBOLS...
Page 26: ...26 P a g e CONTROL OVERVIEW...