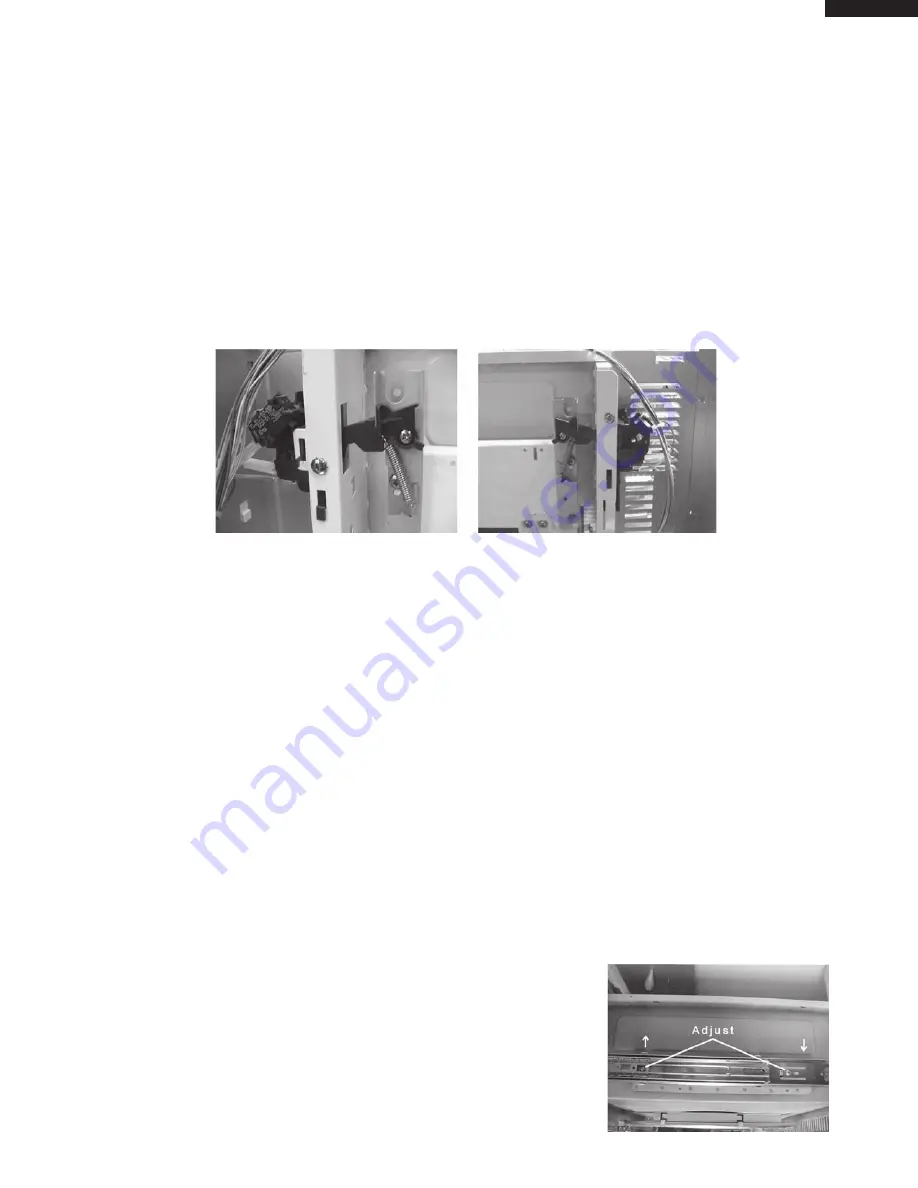
29
KB-6024MS
KB-6024MK
KB-6024MW
2.
Open the drawer and keep it open.
3. To discharge the high voltage capacitor, wait for 60
seconds.
4. Remove the screw holding the latch hook to the oven
flange.
5. Remove the latch hook from the oven flange.
6. Disconnect the wire leads of each switch.
7. Remove each switch from the latch hook by pushing the
one () stopper tab holding each switch.
8. Now, each switch is free.
Re-install
. Re-install each switch in its place. The secondary interlock
switch is in the lower position and the monitor switch is
STOP SWITCH, SECONDARY INTERLOCK SWITCH AND MONITOR SWITCH REMOVAL
. Follow the Microwave Drawer disassembly as previously stated
in the top position, located on the left side of the unit.
The door sensing switch by itself on the right side of the
unit.
2. Re-connect wire leads to each switch. Refer to pictorial
diagram.
3. Secure the latch hooks with mounting screws to oven
flange.
4. Make sure that the monitor switch is operating properly
and check continuity of the monitor circuit. Refer to
chapter "Test Procedure" and "Adjustment procedure".
. Follow the Microwave Drawer disassembly as previously
stated
2.
Open the drawer and keep it open.
3. To discharge the high voltage capacitor, wait for 60
seconds.
4. If the door sensing switch, secondary interlock switch
and monitor switch do not operate properly due to a
misadjustment, the following adjustment should be
made.
6. Loosen the screw holding latch hook to the oven cavity
flange.
7. With drawer closed, adjust latch hook by moving it back
and forth, and up and down. In and out play of the door
allowed by the upper and lower position of the latch hook
should be less than 0.5mm. The vertical position of the
latch hook should be adjusted so that the secondary
interlock switch is activated with the drawer closed. The
horizontal position of the latch hook should be adjusted
so that the monitor switch and drawer sensing switch
are activated with the drawer closed.
8. Secure the screws with washers firmly.
9. Check all of the switches operation. If any switch has
not activated fully, you will need to adjust the slide rail
attached to the Microwave cavity.
0. This is done by following the steps to remove the
"DRAWER/SLIDE RAIL REMOVAL" on page 30. After
you have removed the slide rails, loosen the "2" screws
holding the slide rail to the Microwave cavity and tilt the
front end up and the rear end down, then tighten the
STOP SWITCH, SECONDARY INTERLOCK SWITCH AND MONITOR SWITCH ADJUSTMENT
screws
(Fig. S-1).
.Check and assure that the cap nuts on the Drawer
Support Angles are centered when passing through the
cavity face plate.
After adjustment, check the following.
. In and out play of door remains less than 0.5mm when
in the latched position. First check upper position of latch
hook, pushing and pulling upper portion of drawer toward
the oven face. Then check lower portion of the latch hook,
pushing and pulling lower portion of the door toward the
oven face. Both results (play in the door) should be less
than 0.5mm.
2. The secondary interlock switch interrupts the circuit
before the door can be opened.
3. Monitor switch contacts close when door is opened.
4. Door sensing switch contacts open when door is
opened.
5.
Reassemble the unit
and check for microwave leakage
around door with an approved microwave survey meter.
(Refer to Microwave Measurement Procedure.
Latch Hook Left
Latch Hook Right
Fig. S-1