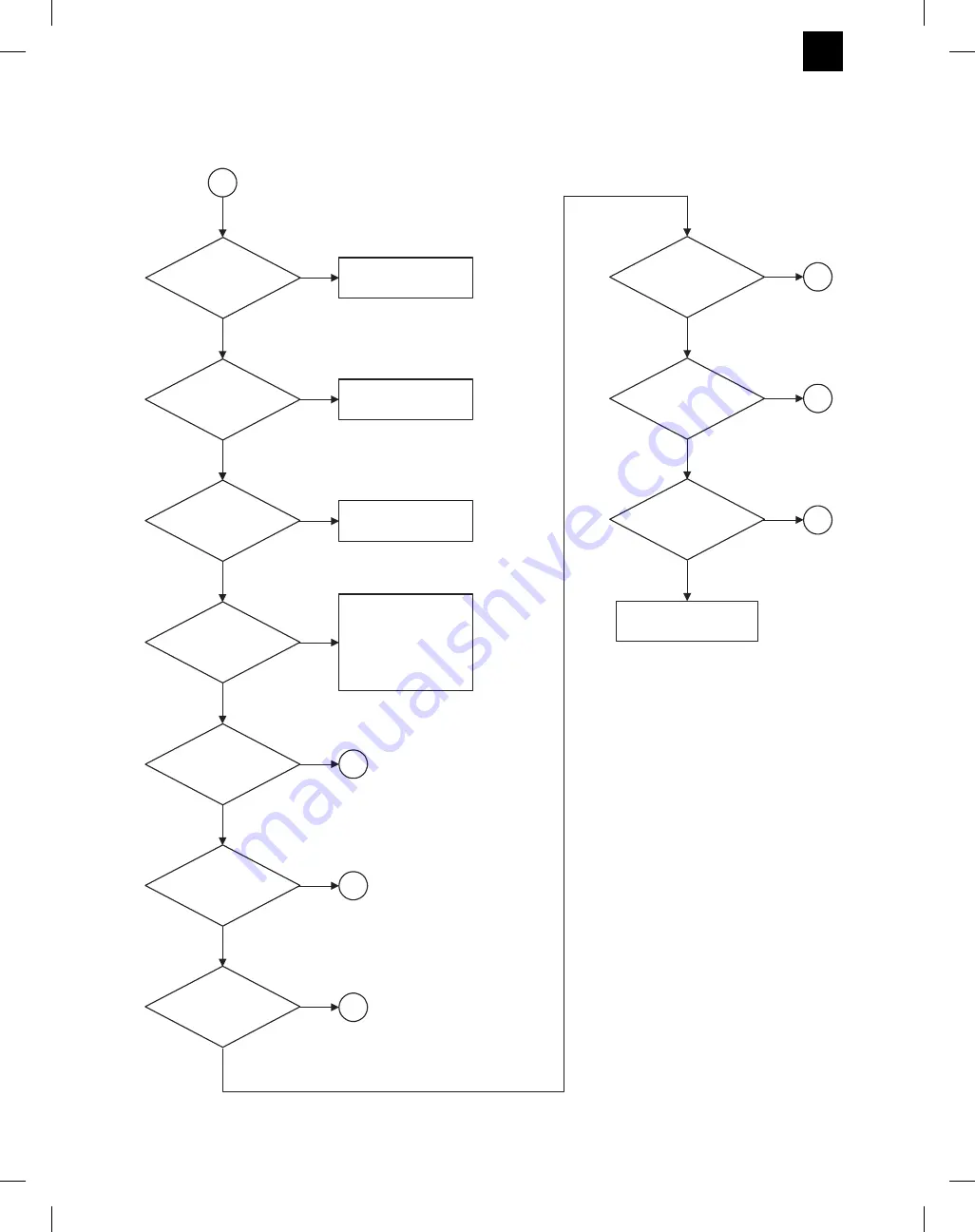
(1) Finisher does not operate. (excluding JAM
state)
1
NO
YES
NO
YES
NO
YES
NO
NO
2
YES
YES
YES
NO
3
NO
NO
4
YES
YES
YES
NO
NO
YES
Is connection
cable properly
connected?
+5V between
CNA-6 and CNA-5 of
main PWB?
+24V between
CNA-1 and CNA-3 of
main PWB?
Are
DSW1, 2, 3
signals of main PWB
OK?
Transfer motor
rotates normally?
Elevator motor
rotates normally?
Off-set motor
rotates normally?
Connect connection
cable to body properly.
Check or replace harness
or check supply voltage.
Check or replace harness
or check supply voltage.
Check connections.
Check harnesses at
upper and lower surfaces
and harness leading to
upper transfer switch for
connections, and replace
if necessary.
Staple unit
moving motor rotates
normally?
Pusher motor rotates
normally?
Jogger motor rotates
normally?
Check main PWB and
replace if necessary.
4
4
3
AR-FN3
8 – 2
8/19/1999
Summary of Contents for AR-FN3
Page 20: ...15 15 15 15 16 AR FN3 8 19 1999 5 7 ...
Page 27: ... Rollers Paper guides AR FN3 7 2 8 19 1999 ...
Page 28: ...AR FN3 8 19 1999 7 3 ...
Page 29: ... Gears Others Sensors Belts AR FN3 7 4 8 19 1999 ...
Page 51: ...3 Main PWB page arrangement 1 2 AR FN3 10 9 8 6 1999 ...
Page 52: ...Main PWB page arrangement 2 2 AR FN3 8 6 1999 10 10 ...