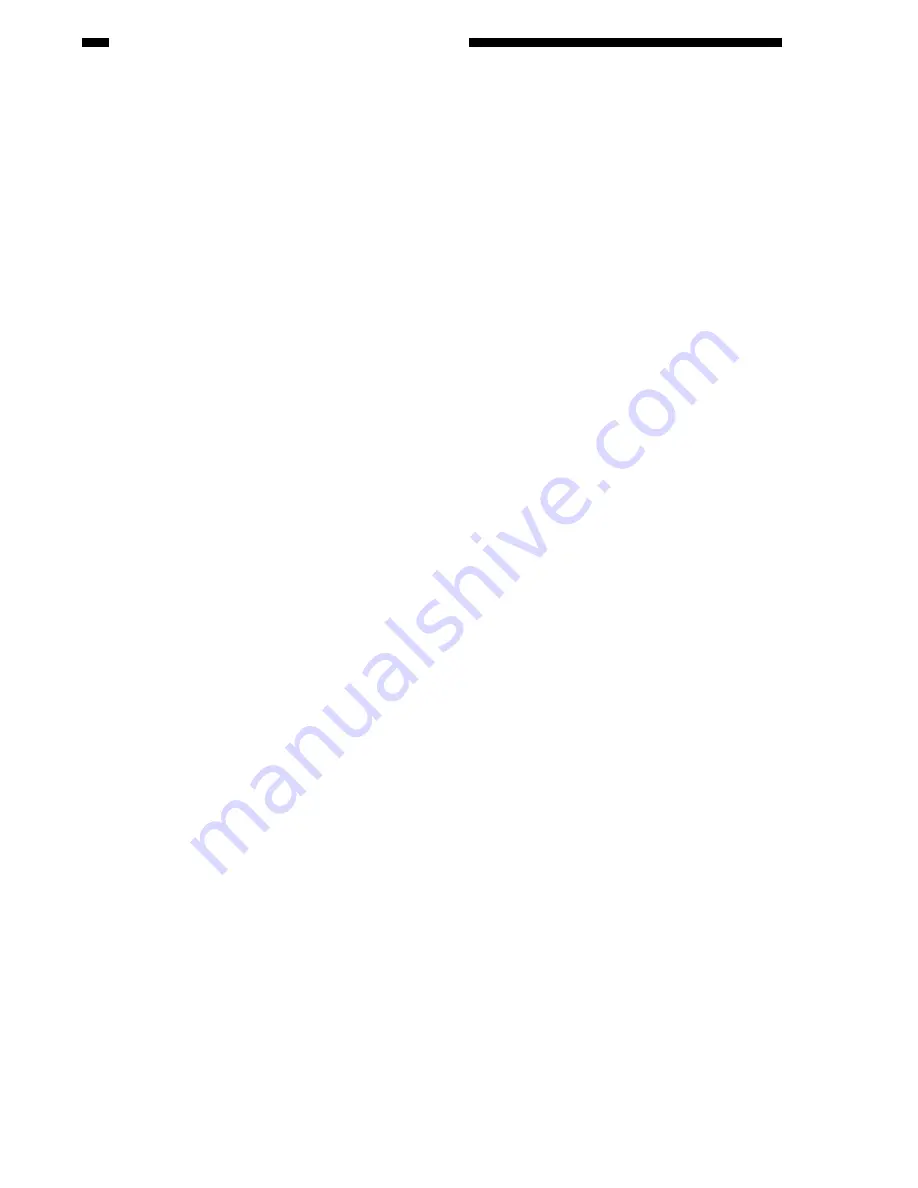
2-38
CHAPTER 2 FINISHER UNIT BASIC OPERATION
G.
Tray Operation
The finisher has two delivery trays-upper tray 1 and lower tray 2. The upper and lower trays
move up and down independently.
Tray 1 is moved up and down by the tray 1 lift motor (M5), and tray 2 by the tray 2 lift motor
(M10).
The tray 1 position is detected by counting the clock pulses of tray 1 lift motor clock sensors 1
and 2 (PI9 and PI19) in relation to the tray 1 home position sensor (P18). The tray 2 position is
detected by counting the clock pulses of tray 2 lift motor clock sensors 1 and 2 (PI23 and PI24) in
relation to the tray 2 home position sensor (PI25).
When the tray is already at the home position, it is moved away from the home position once,
then returned to that position.
When both tray 1 and tray 2 are at the home position, the above operation is performed for tray
1 and tray 2 in this order.
The finisher controller PCB moves up and down the tray selected by the host machine so that it
is positioned at the delivery slot.
The upper limit of the tray is detected by the tray coming close detecting switch (MS9). The
finisher controller PCB stops the drive (up) of the tray 1 lift motor (M5) as soon as the tray upper
limit detecting switch turns on.
The height of the stack on the tray is identified by the height sensor (PS1), which measures its
distance from the top of the stack. The tray is moved down when the distance between the top of the
stack and the delivery assembly drops to a specific measurement.
The finisher controller PCB cuts off the +24V power of the tray 1 lift motor (M5) as soon as the
safety zone switch (MS3) turns on while the shutter and the swing guide are open, stopping the
operation of the finisher.
Summary of Contents for AR-F15
Page 8: ......
Page 36: ......
Page 77: ...2 41 CHAPTER 2 FINISHER UNIT BASIC OPERATION Height sensor PS1 Paper Figure 2 240 ...
Page 94: ......
Page 110: ...3 16 CHAPTER 3 SADDLE STITCH UNIT BASIC OPERATION Figure 3 302 ...
Page 124: ...3 30 CHAPTER 3 SADDLE STITCH UNIT BASIC OPERATION Cam Mount Figure 3 404 ...
Page 138: ...3 44 CHAPTER 3 SADDLE STITCH UNIT BASIC OPERATION ...
Page 140: ......
Page 156: ......
Page 202: ......
Page 214: ......
Page 223: ...7 9 CHAPTER 7 TROUBLESHOOTING II ARRANGEMENT OF ELECTRICAL PARTS A Finisher Unit ...
Page 260: ...7 46 CHAPTER 7 TROUBLESHOOTING ...
Page 262: ......
Page 273: ...A 11 APPENDIX Q500 FF3 4071 SADDLE RELAY BUNDLE WIRE ...
Page 276: ...Memo ...
Page 277: ...Memo ...