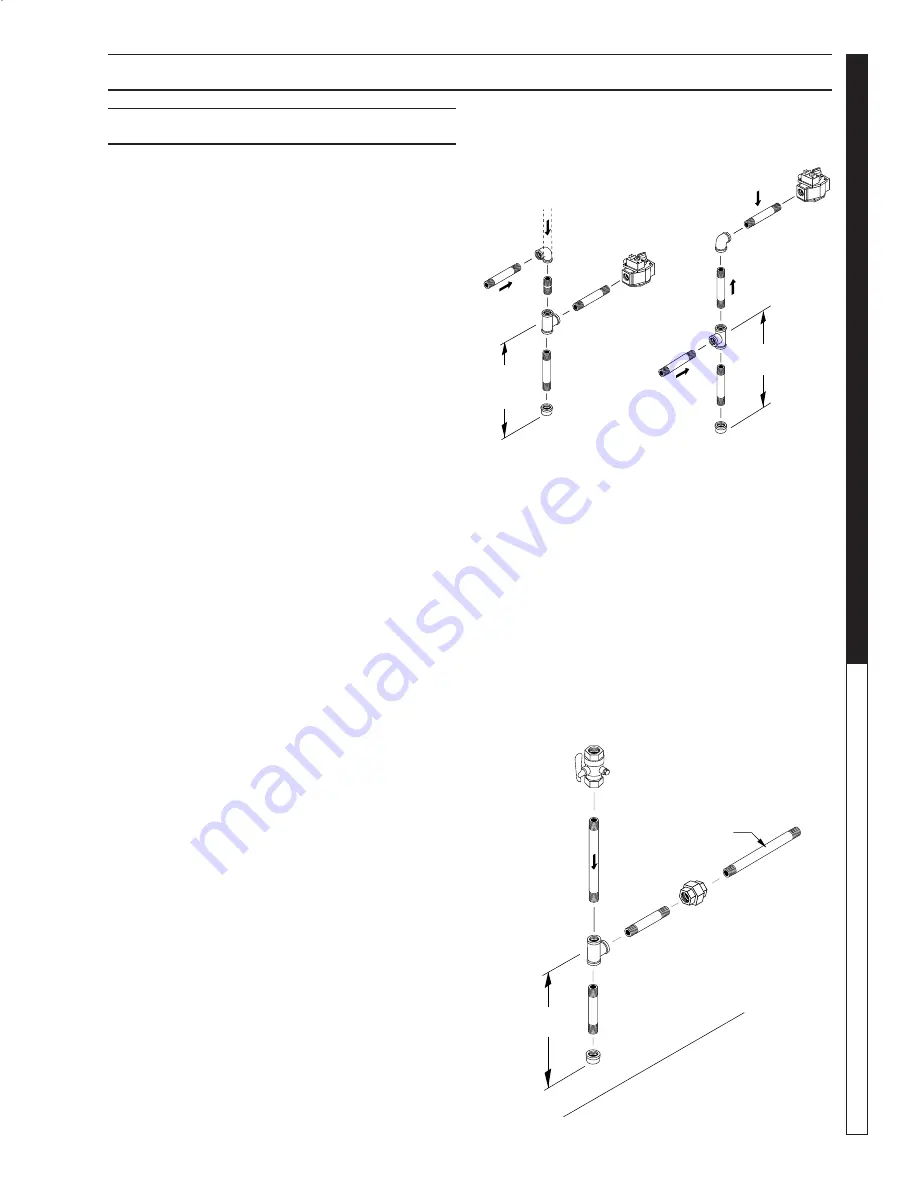
97-610, 97-6152 • REV. 7/04
9
PRESSURE
W
ASHER
OPERA
T
OR’S MANU
AL
INSTALLATION
INSTALLATION
Place machine in a convenient location providing ample
support, drainage and room for maintenance (see page
6).
Location:
The location should protect the machine from damaging
environmental conditions, such as wind, rain and freez-
ing.
1. The machine should be run on a level surface
where it is not readily influenced by outside sources
such as strong winds, freezing temperatures, rain,
etc. The machine should be located considering
accessibility for the replacing of components and
the refilling of detergents, adjustments and main-
tenance. Normal precautions should be taken by
the operator of the machine to prevent excess
moisture from reaching the power unit or electri-
cal controls.
2. It is recommended that a partition be made be-
tween the wash area and the machine to prevent
direct spray from the spray gun from coming in
contact with the machine. Excess moisture reach-
ing the power unit or electrical controls will reduce
the machine’s life and may cause electrical shorts.
3. During installation of the machine, beware of poorly
ventilated locations or areas where exhaust fans
may cause an insufficient supply of oxygen. Suffi-
cient combustion can only be obtained when there
is a sufficient supply of oxygen available for the
amount of fuel being burned. If it is necessary to
install a machine in a poorly ventilated area, out-
side fresh air may have to be piped to the burner
and a fan installed to bring the air into the area.
4. Do not locate near any combustible material. Keep
all flammable material at least 20 feet away.
Allow enough space for servicing the machine.
Local code will require certain distances from floor
and walls. (Two feet away should be adequate).
WARNING: Avoid small areas or near exhaust fans.
Gas Codes:
Confer with local gas company and with proper mu-
nicipal officials regarding any specific code or regula-
tions governing the installation. The installation must
conform to local codes.
Electrical:
The machine, when installed, must be electrically
grounded in accordance to local codes. Check for
proper power supply using a volt meter; check the se-
rial plate for the correct requirements.
Gas Piping:
Figure 1: DRIP LEG
Sediment trap (drip leg) must be
installed in the supply line.
Install a union in the gas line adjacent to and upstream
from the control manifold and downstream from the
manual main shut-off valve. A 1/8" NPT plugged tap-
ping accessible for test gauge connection shall be in-
stalled immediately upstream of the gas supply con-
nection for the purpose of determining the gas supply
pressure to the burner, and to prevent damage to gas
valve.
If a manual gas shut off valve is not in the gas supply
line within six feet of the machine and in an accessible
location, one shall be installed.
Figure 2: UNION LOCATION
Manual
Shut-Off Valve
1/8" NPT Plugged
Pressure Gauge
Port Location
Union
Control Manifold
Tee
Flow
3" (7.62 mm)
Minimum
Floor Level
Pipe
Cap
To
Gas Valve
1/4" Test Port
(6" - 14 W.C.
or 1/2" PSIG)
Gas
Valve
Gas
Valve
Drop
3" (7.62 mm)
Minimum
3"
(7.62 mm)
Minimum