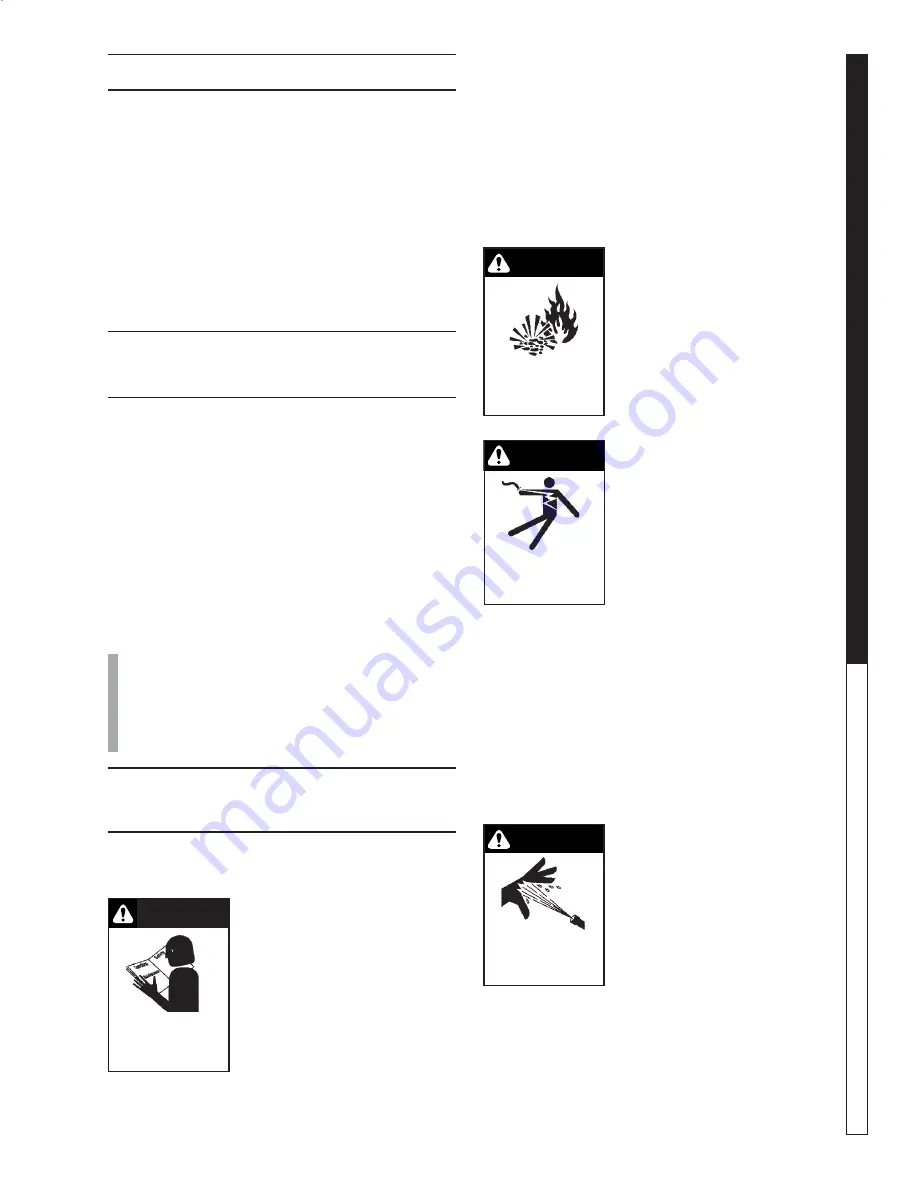
97-610, 97-6152 • REV. 7/04
5
PRESSURE
W
ASHER
OPERA
T
OR’S MANU
AL
INTRODUCTION
Thank you for purchasing our Pressure Washer.
This manual covers the operation and maintenance of
the 301001D, 301007D, 352001A, 352007A, 402001A,
402007A, 402001B, 402007B, 402001C, 402007C,
502001A, 502007A, 502001B, 502007B, 502001C,
502007C, 353001A, 353007A, 353001B, 353007B,
353001C, 353007C, 503001B, 503007B, 503001C and
503007C model washers. All information in this manual
is based on the latest product information available at
the time of printing.
We reserve the right to make changes at any time with-
out incurring any obligation.
This machine was designed for
maximum use of 4 hours per day,
5 days per week.
Owner/User Responsibility:
The owner and/or user must have an understanding
of the manufacturer’s operating instructions and warn-
ings before using this pressure washer. Warning infor-
mation should be emphasized and understood. If the
operator is not fluent in English, the manufacturer’s
instructions and warnings shall be read to and dis-
cussed with the operator in the operator’s native lan-
guage by the purchaser/owner, making sure that the
operator comprehends its contents.
Owner and/or user must study and maintain for future
reference the manufacturers’ instructions
This manual should be considered a permanent
part of the machine and should remain with it if
machine is resold.
When ordering parts, please specify model and
serial number.
IMPORTANT SAFETY
INFORMATION
WARNING: When using this machine basic precau-
tions should always be followed, including the fol-
lowing:
CAUTION: To reduce the risk of
injury, read operating instruc-
tions carefully before using.
1. Read the owner's manual
thoroughly. Failure to follow
instructions could cause mal-
function of the machine and
result in death, serious bodily
injury and/or property dam-
age.
2. All installations must comply with local codes. Con-
tact your electrician, plumber, utility company or
the selling distributor for specific details.
To comply with the National Electrical code (NFPA
70) and provide additional protection from risk of
electric shock, this pressure washer is equipped
with a UL approved ground fault circuit interrupter
(GFCI) power cord for machines rated 250V 30
amp or less, single phase.
3. Know how to stop the machine and bleed pres-
sures quickly. Be thoroughly familiar with the con-
trols.
4. Stay alert. Watch what you are doing.
WARNING: Flammable liquids
can create fumes which can ig-
nite causing property damage
or severe injury.
5. Risk of explosion - Do not
spray flammable liquids or
operate in an explosive loca-
tion. Operate only where
open flame or torch is permit-
ted.
WARNING: Keep water spray
away from electrical wiring or
fatal electric shock may result.
Read warning tag on electrical
cord.
6. To protect the operator from
electrical shock, the machine
must be electrically
grounded. It is the responsi-
bility of the owner to connect
this machine to a UL grounded receptacle of proper
voltage and amperage ratings. Do not spray wa-
ter on or near electrical components. Do not touch
machine with wet hands or while standing in wa-
ter. Always disconnect power before servicing.
WARNING: Spray gun kicks back. Hold with both
hands.
7. Grip cleaning wand securely with both hands be-
fore starting the cleaner. Failure to do this could
result in injury from a whipping wand.
WARNING: Equipment can pro-
duce a high pressure stream of
fluid that can pierce skin and its
underlying tissues, leading to
serious injury and possible
amputation.
8. High pressure developed by
these machines can cause
personal injury or equipment
damage. Use caution when operating. Do not di-
rect discharge stream at anyone or at any part of
the body, or severe injury or death will result. This
machine is to be used only by qualified operators.
READ OPERATOR’S
MANUAL
THOROUGHLY
PRIOR TO USE.
CAUTION
WARNING
RISK OF INJECTION
OR SEVERE INJURY
TO PERSONS. KEEP
CLEAR OF NOZZLE.
WARNING
RISK OF EXPLOSION:
DO NOT SPRAY
FLAMMABLE
LIQUIDS.
WARNING
KEEP WATER SPRAY
AWAY FROM
ELECTRICAL WIRING.