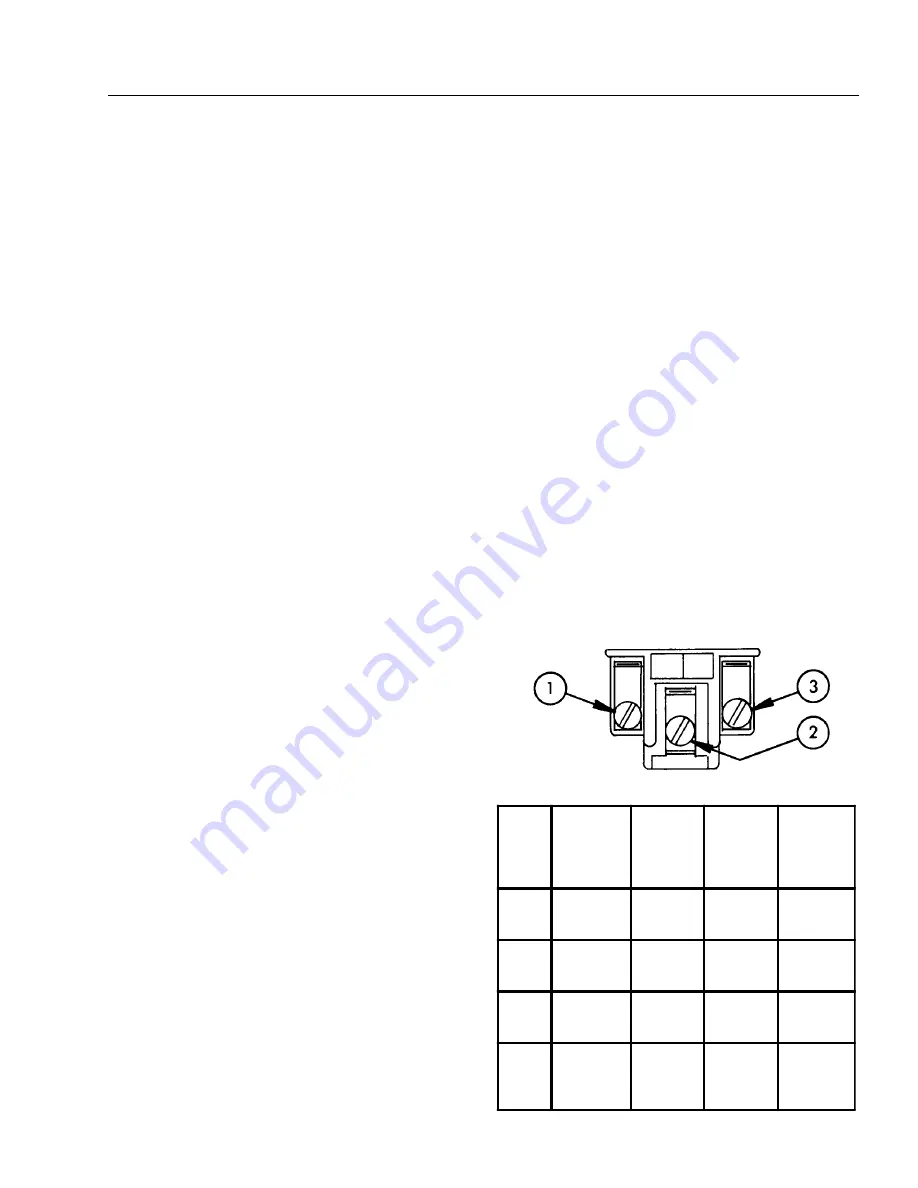
HNG SERIES PRESSURE WASHER
OPERATOR’S MANUAL
15
Gas Pressure Requirements:
All propane fired machines operate on gas phase only.
They are designed to operate at a pressure of 11 w.c.i.
(between 1/3 and 1/2 of one PSI), and are often oper-
ated at even higher pressures when extra heat is needed.
Exterior regulators are needed to control the system. Pro-
pane bottles are not included with the machine. A high
pressure regulator should be installed on the propane
bottle and a low pressure regulator attached to the pres-
sure washer.
Propane Cylinder Capacity:
An important consideration with propane systems is the
capacity of the supply cylinder relative to the needs of
the burner. The burner operates on propane as a gas.
As gas is used from the propane cylinder, the liquid in
the cylinder boils to maintain gas pressure. This boiling
process cools the liquid, and in a heavy, continuous-de-
mand situation, the liquid temperature can fall to the point
at which it cannot provide gas as rapidly as is needed. In
this case, it may be necessary to warm the propane cyl-
inder by directing a warm spray, not over 120°, on the
cold cylinder, or by manifolding two propane bottles to-
gether to increase total vaporization capacity. It is rec-
ommended that a minimum 100 lb. propane bottle be
used on the machine, depending on the length of run-
ning time desired.
BURNER FEATURES
Operated Automatic Valve:
This machine is equipped with a thermopile self-pow-
ered combination gas control. This system is designed
as a constant burning pilot. Lighting of the pilot is ac-
complished by manually lighting the pilot. A thermostat
and flow switch control the main solenoid valve.
Care of Main Burner:
Due to condensation from heater coils dripping down on
the burners, a scale buildup may occur in the burner jet
orifices.
1.
TO REMOVE BURNER MANIFOLD FROM
WATER HEATER COIL:
Turn off the gas at the main burner by turning the
knob to the “OFF” position on the gas valve and main
gas supply.
Disconnect the pilot and ignition lines from the gas
valve. Disconnect union in main burner line. (Remove
the nuts from the U-bolts, item 28 on page 23). Slide
burner manifold out through shell opening.
2.
TO CLEAN BURNER JETS:
Select proper size drill for type of gas involved. Use
vise to hold drill and to ream out each jet orifice.
If the water heater will be exposed to freezing weather,
an antifreeze solution should be circulated through the
coils by whatever means are available for the particular
system the water heater is used on.
BURNER TROUBLESHOOTING
Millivolt System Check:
This machine has a thermopile self-powered combina-
tion gas control. Before checking the millivolt system,
the following operations should be performed and ob-
servations made:
1. Inspect system for proper wiring.
2. The switch leads and all wire connections should be
cleaned and tightened to eliminate all unnecessary
resistance.
3. Clean and/or adjust pilot for maximum flame impinge-
ment on the thermopile.
4. If pilot will not remain lit when gas cock dial is re-
leased, check automatic pilot (Step D).
The millivolt system and individual components may be
checked with a DC millivolt meter having a 0-1000 MV
range. Conduct each check as shown in the chart below
by connecting the meter test leads to terminals as indi-
cated. All readings are closed circuit.
TERM
TERM
TERM
TH
TP
TH
TP
MILLIVOLT
OPERATOR
TERMINAL
PANEL
Check
Test
To Test
Connect
Meter
Leads To
Terminals
Switch
Flow &
Burner
Contacts
Meter
Reading
Should
Be
A
Complete
System
2 & 3
Closed
100 MV or
More
B
Thermopile
Output
1 & 2
Open
Greater
than 250
C
System
Resistance
1 & 3
Closed
Less than
35
D
Auto/Pilot
Dropout
1 & 2
Open
Between
120 - 30
MV
Summary of Contents for HNG-3010
Page 35: ......