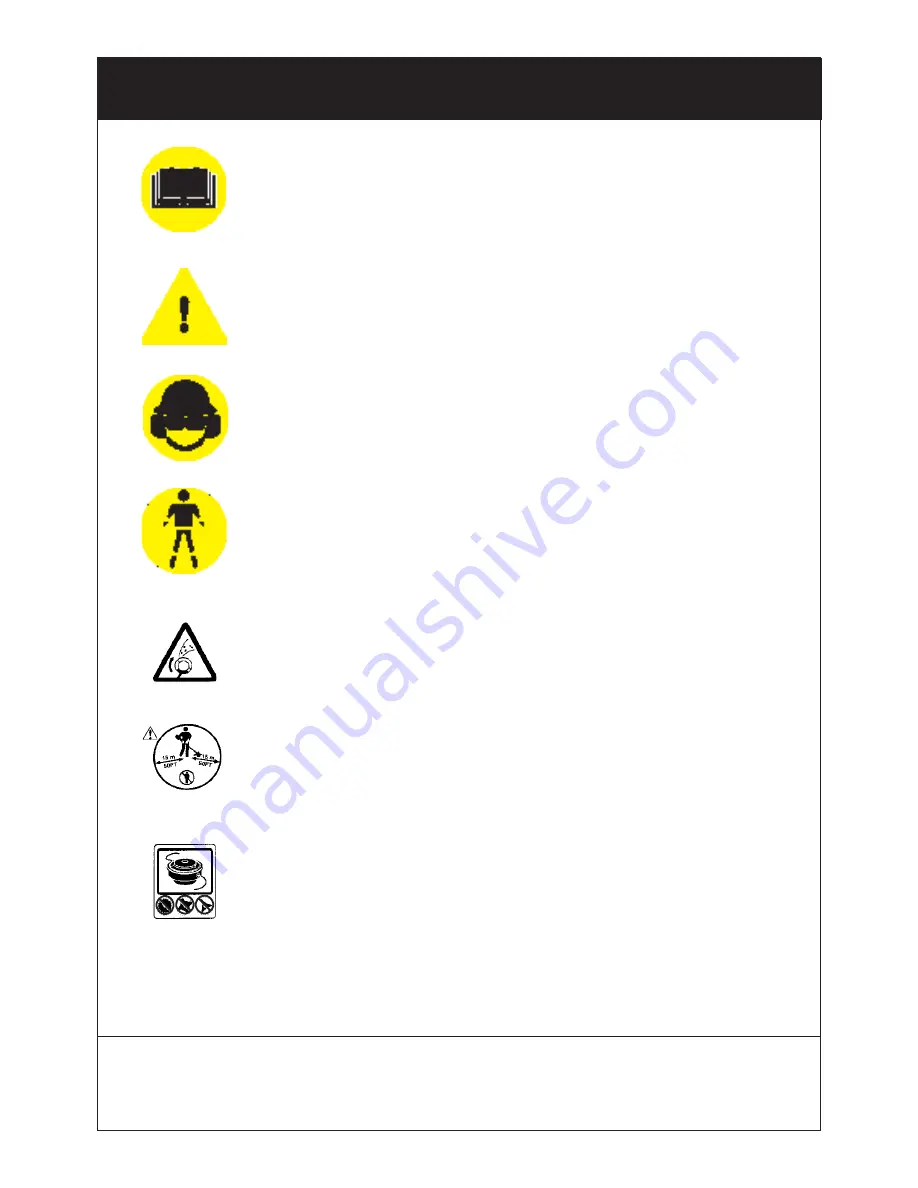
PAGE 4
FOR SAFE OPERATION
Read operator’s instruction book before
operating this machine.
Read, understand and follow all warnings.
Wear head, eye and ear protection.
Use suitable work-wear to protect yourself.
Watch out for thrown objects & ricochets
The operator of the machine must ensure,
while working, that no persons or animals
come closer than 50 feet (15 meters).
Only use non--metallic, flexible
cutting attachments, i.e. trimmer
heads with trimmer line.
WWW.SGS-ENGINEERING.COM
CALL FOR ASSISTANCE:
01332 576 850