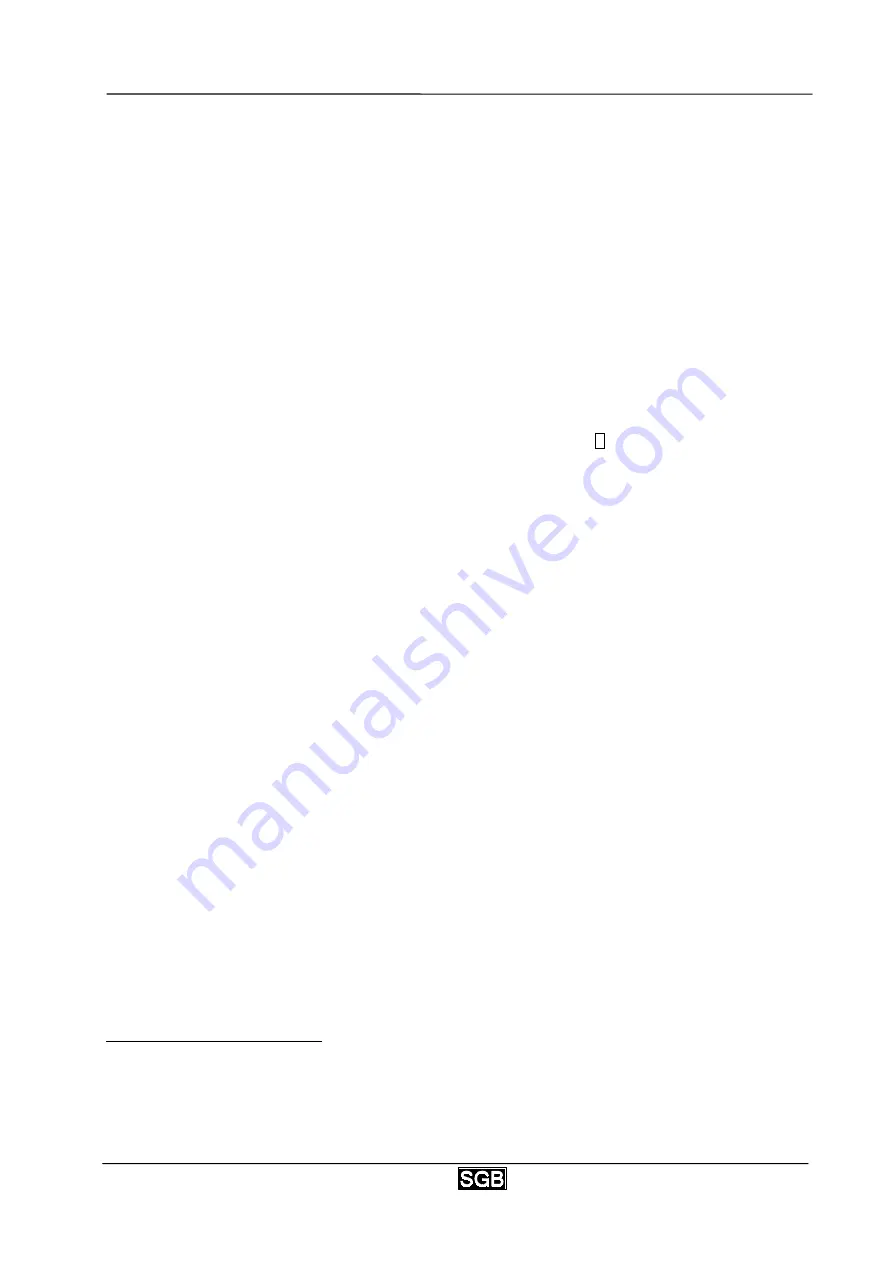
OVERPRESSURE LEAK DETECTOR
DLR-2
18/01/2002 Ihr Partner für Leckanzeigetechnik
Sicherungsgerätebau GmbH, Siegen
- 5 -
(2) In a dry room or in a suitable protective box in the open.
(3) Assembly in the protective box: additional external signal or alarm forwarding via potential-
free contacts to a control room or similar.
(4)
NOT to be assembled in potentially explosive areas.
5.4. Assembly of the connecting pipes (between leak detector and pipework)
(1) Metal (usually copper) or plastic pipes, the pressure resistance of which at least complies
with the testing pressure of the interstitial space, this is also valid for fittings and threaded
fittings. (Heed temperature range, particularly when using plastic).
(2) At least 4 mm clearance, wall thickness at least 1 mm.
(3) Not longer than 50 m, if this is not possible then the cross-section of the pipe must be en-
larged using appropriate transition pieces.
(4) The cross-section must remain intact, indentation and bending
are not allowed.
(5) Plastic pipes laid underground or above ground outside must be in a protective outer pipe.
(6) Seal the protective pipe gas-tight.
(7) Avoid electrostatic charge (e.g. when introducing and pulling through pipes).
5.5. Selection of pressure reducing device
(1) The pressure reducing device must have an integrated safety valve.
(2) The setting range of the pressure reducing device to be used must be chosen in such a
way that it is suitable for the application case concerned.
(3) The maximum pressure which can be set on the pressure reducing device should not ex-
ceed the testing pressure of the interstitial space (SGB recommendation).
5.6. Gas bottle and pressure reducing device (functional test and putting into operation)
(1) Following the secure upright installation of the gas bottle, remove the protective hood.
(2) Mount the pressure reducing device on the bottle.
(3) Close the shut-off valve on the pressure reducing device.
(4) Turn back the pressure regulating valve as far as possible.
(5) Open the bottle shut-off valve.
(6) Set the nominal pressure on the pressure reducing device using the pressure regulating
valve (readjust during pressure build-up if necessary).
7
If necessary, customary fittings (set bending radii) must be used for the plastic pipes