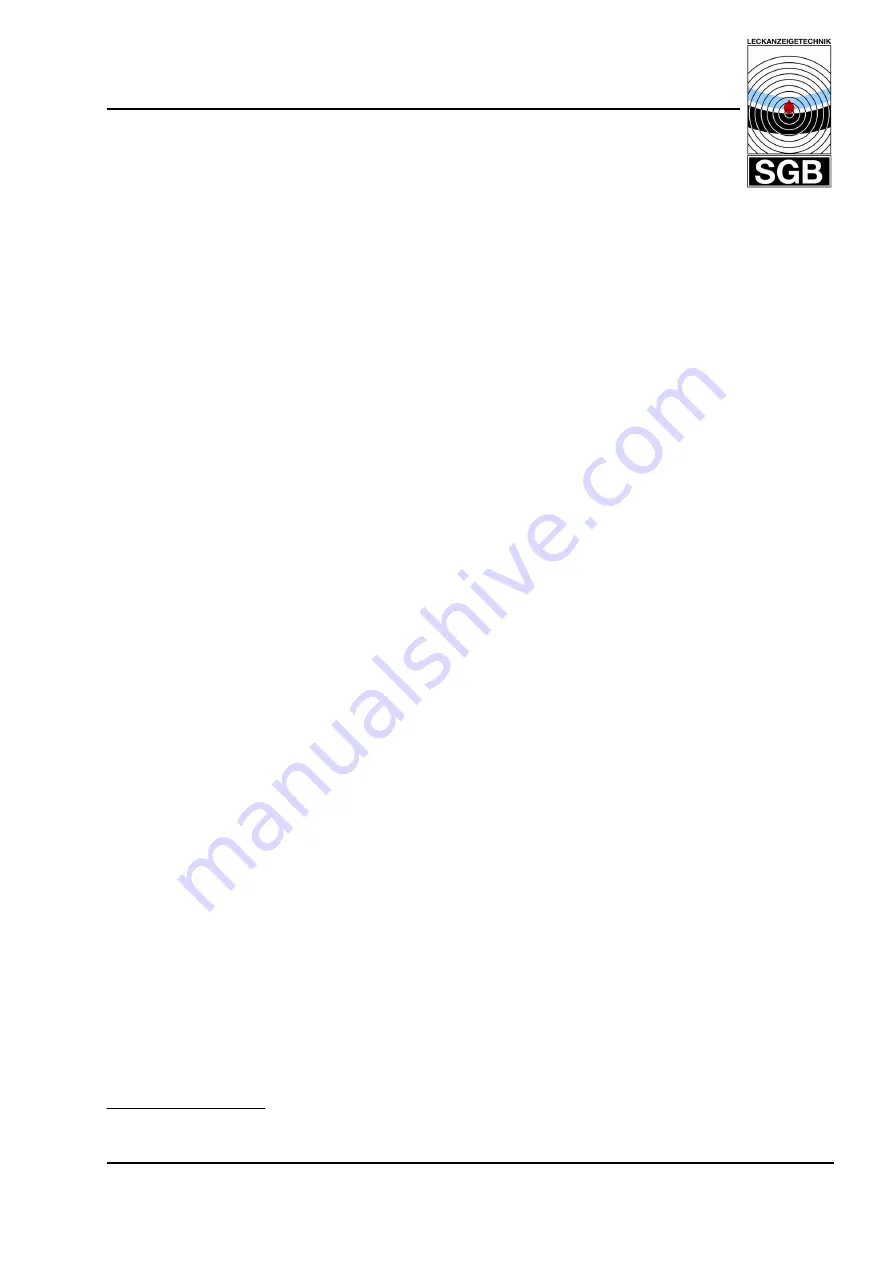
DECLARATION OF CONFORMITY
\\SGBUNIX\VERKAUF\ÜBERSETZUNGEN\DOKUMENTATIONEN\ENGLISCH\D-FFL 10\11-DLR-8, D-FFL 10, DLR-S,DLR-2, DLV-
WKK-2003-07-03.DOC
This declaration applies for
PRESSURE LEAK DETECTORS
DLR-8, D-FFL 10, DLR-S, DLR-2, DLV-WKK
from the Company
Sicherungsgerätebau GmbH
Hofstraße 10
D- 57076 Siegen
With this declaration, SGB confirms that the leak detectors specified above fulfill the protection
requirements established in
EC Directive 89/336/EEC for
alignment of the legal regula-
tions of the member states
regarding electro-magnetic
compatibility and in the German
law on electromagnetic com-
patibility (EMC) dated
9 November 1992 (§ 4 Para. 1).
This declaration applies for
appliances produced according
to the documentation (technical
description, drawing(s) – which
are constituents of this declara-
tion.
The following declarations were
used for evaluation of the prod-
ucts in terms of its electromag-
netic compatibility:
•
EN 50 082-1: 1992
•
EN 55 014: 1993
•
EN 61 000-3-2: 1995
•
EN 61 000-3-3: 1995
EC Directive 73/23/EEC for
alignment of the legal regula-
tions of the member states
regarding electrical operating
equipment for use within certain
voltage limits and defined in the
1
st
Code on the Equipment
Protection Law dated 11 June
1979.
This declaration applies for
appliances produced according
to the documentation (technical
description, drawing(s) – which
are constituents of this declara-
tion.
The following declarations were
used for evaluation of the prod-
ucts in terms of use within cer-
tain voltage limits:
•
EN 60 335-1:1988
•
EN 61 010-1:1993 (IEC
1010-1:1990 + A1:1992,
modified)
EC Directive 94/9 EEC for
alignment of the legal regula-
tions of the member states for
equipment and protective sys-
tems for intended use in explo-
sion hazard areas or in the 2
nd
Code on the Equipment Protec-
tion Law dated 12 December
1996.
The leak detector may be con-
nected with its pneumatic com-
ponents to monitoring cham-
bers of tanks requiring equip-
ment regarding category 3.
This declaration applies for
appliances produced according
to the documentation in accor-
dance with internal QM docu-
mentation (technical description
with drawings) – which are con-
stituents of this declaration.
Evaluation of the product was
accomplished. The following
documents were used for this
purpose:
•
EN
1127-1:1997
•
EN
13463-1:2001
•
EN
13160-1:2003
The ignition hazard analysis / risk
evaluation indicated no further
hazards.
Siegen, 4 July 2003
Martin Hücking, Development, Explosion protection representative