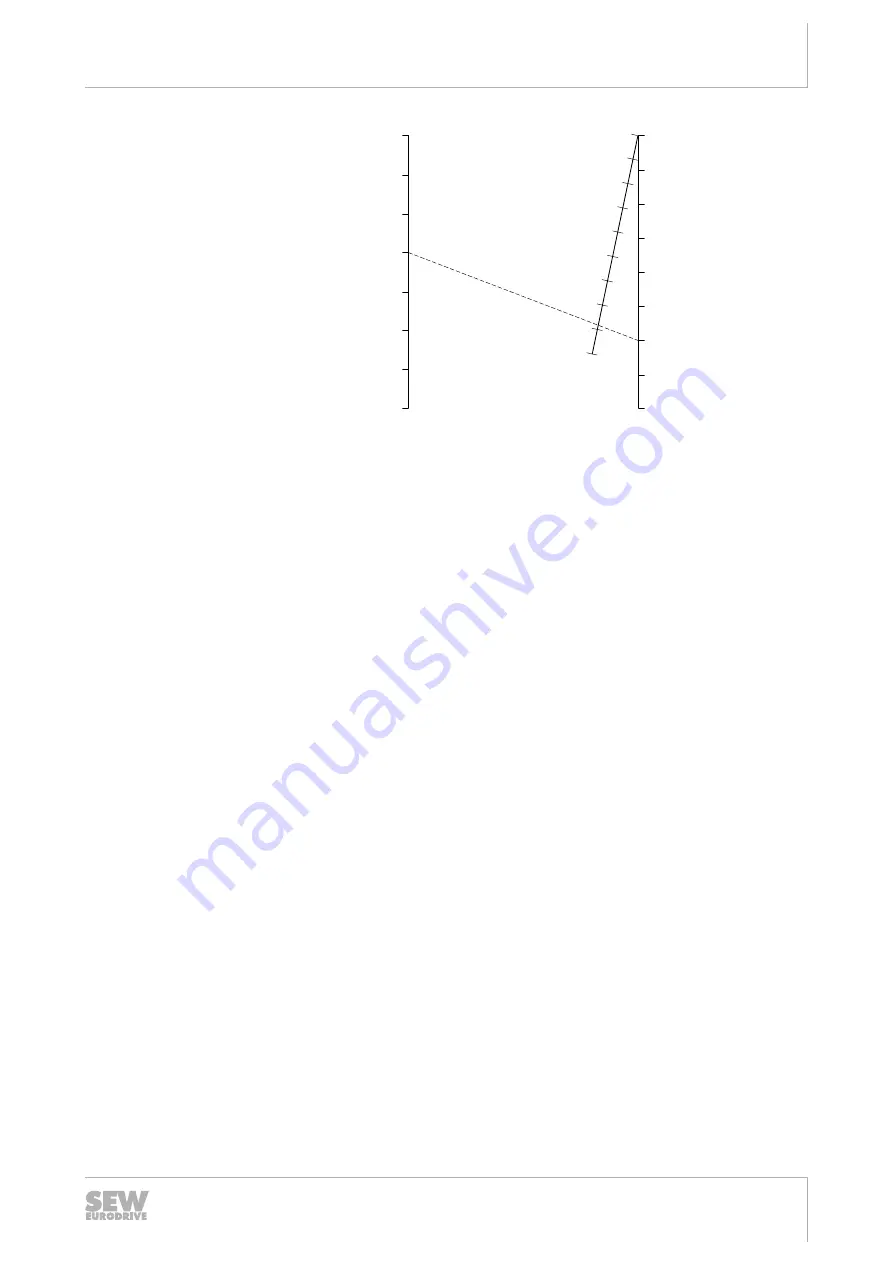
5
Installation/assembly
Oil heater
Assembly and Operating Instructions – M1..N Series Single-Stage Helical Gear Units
65
°C
°C
[C]
[B]
[A]
30
10
9
8
7
6
5
4
3
2
10
9
8
7
6
5
4
3
2
1
25
20
15
10
5
0
-5
5-16-7_figure2: Nomogram of the included differential
25544698507
[A]
Setting range
[B]
Obtained differential
[C]
Differential setting
29203856/EN – 03/2020