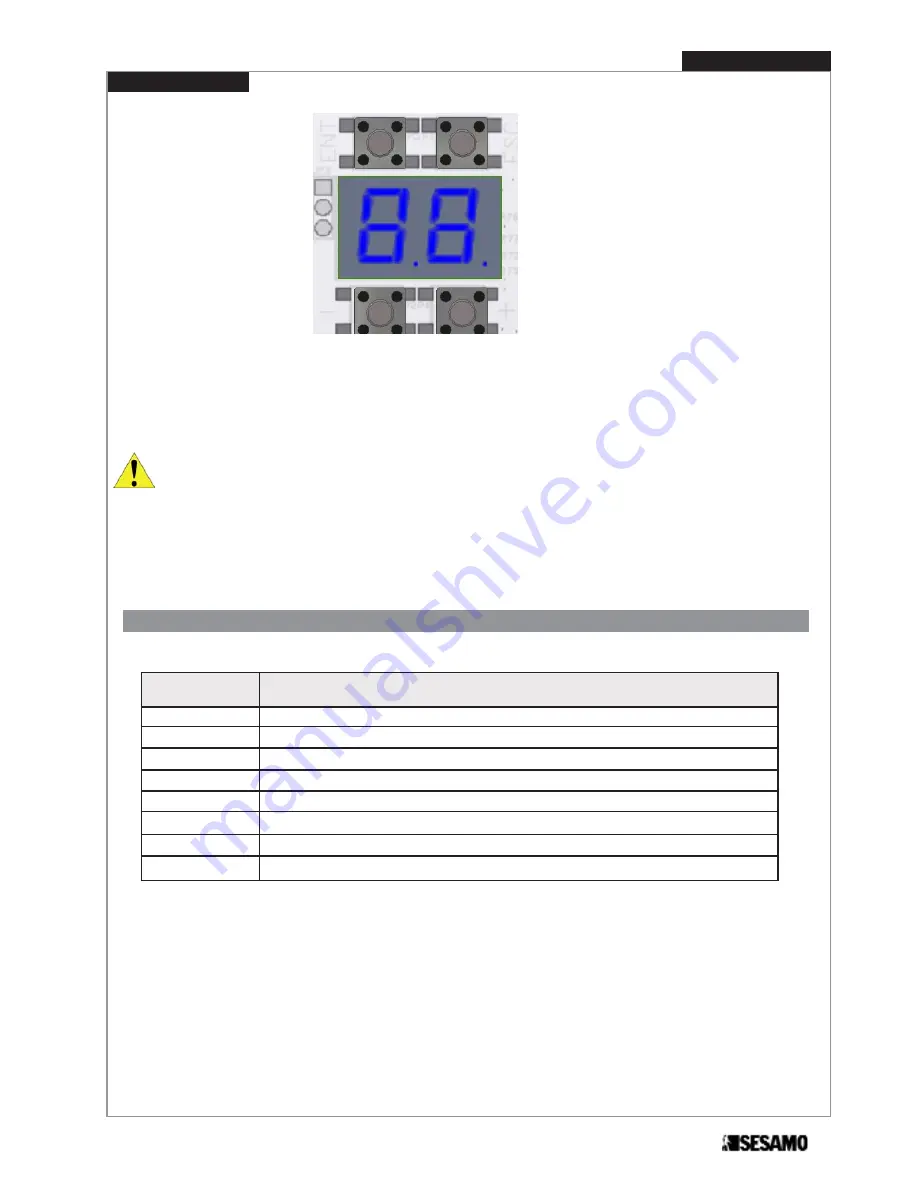
6. Press push buttons [
+
] e [
-
] until
LP
appears; press [
ENT
] until [
--
] appears; press again[
ENT
] for 5 seconds; when
disappears [
--
] release push button [
ENT
].
7. Door will start learning cycle, opening direction.
ATTENTION:
when door reaches desired opening position, stops door in that position: this position will be memori-
zed as max opening. Immediately after, door will close completely at slow speed with display
CL
blinking.
When door is in closed position and
CL
stop blinking, it is possible to check functioning pressing [
ENT
]: door has to
open and close regulary.
During the functioning, max opening angle is reduced as a factory setting. This parameter is modificable through
software MillenniumWare (advanced parameter
→ % reduction opening angle)
.
First cycle (opening/closing), after (RESET) will be at slow speed.
ESC
ENT
+
_
Fig. 32
31
PROSWING(M)
Operating instruction
Code
Description
OP
Fixed
Door opened
OP
Blinking
Door opening
CL
Fixed
Door closed
CL
Blinking
Door closing
E1
Door needs self learning procedure (see Paragraph “Start up”)
E2
Wrong arm selected (DIP 1), or wrong selection automatism (DIP 5)
E3 / E4
Over Current
E8
NO encoder.
Display are also used to show message or error code:
Message or errors code