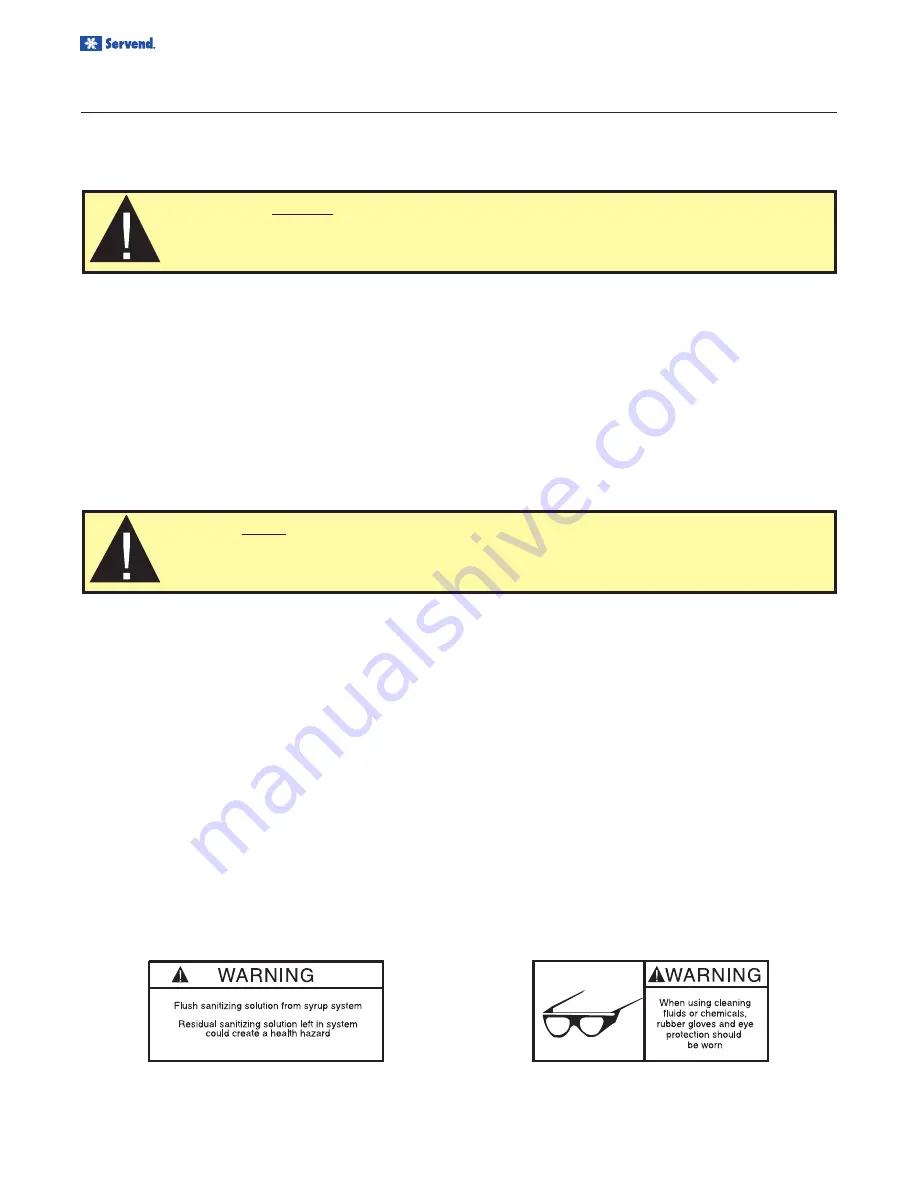
16
Installation and Service Manual
Note:
Cleaning and sanitizing is not required for potable water circuits. Potable water lines should remain con-
nected and operational during the cleaning and sanitizing procedures for syrup circuits.
CLEANING THE DISPENSING VALVES
1.
Disconnect each syrup container from its product line,
tank connector, or bag-in-box connector. Remove
product from the lines by purging with clean warm
tap water until syrup has been fully purged from the
product lines and valves.
2.
Clean all lines and fittings with cleaning solution and
rinse with clean, room temperature water to remove
all traces of residual product.
3.
For the A&W pre-mix valve, clean dispense nozzle in
place with sanitizing solution and nozzle brush, up to
internal shut off port.
CLEANING THE PRODUCT LINES
1.
To clean each valve product line, attach the valve
product lines to the pressure tank containing the
cleaning solution or place the bag-in-box connector
in cleaning solution. Remove branch port cover on
bag-in-box connector to allow suction of cleaning
solution. Make sure each line is completely filled.
Pressurize the lines by pulsing the valves.
PRESSURIZING THE PRODUCT LINES
1. For 15 seconds turn dispensing valve
“on”
,
“off”
,
and then immediately
“on”
again for 15 cycles.
2. Allow the valve to remain flowing for 3 minutes.
3. Repeat pulsing and flowing the valves again until all
cleaning solution has been used.
4. Flush the cleaning solution from the lines with clean
water after a minimum of 3 minutes, by pulsing the
valves as described above.
5. Attach each valve product line to the pressure tank
containing the sanitizing solution or place the bag-in-
box connector in sanitizing solution. Remove branch
port cover on bag-in-box connector to allow suction
of sanitizing solution. Be sure all connections are
cleaned and sanitized before connecting to each prod-
uct line.
6. Pressurize and fill the lines with sanitizing solution.
Make sure lines are completely filled. Allow the sani-
tizing solution to flow through each valve while acti-
vating the valves for 15 cycles (as described in “Pres-
surizing the product lines”).
a.
Leave valves
“off”
and allow to stand pressur-
ized for 30 minutes.
b.
Activate the valves for two (2) cycles (as de-
scribed in “Pressurizing the product lines”). Flush
remaining sanitizer continuously through the
valves.
7. Reconnect the syrup containers to their respective
circuits. Prepare the unit for operation.
8. Draw drinks to refill lines and flush the sanitizing
solution from the dispenser. Taste the beverage to
verify that there is no off-taste (chlorine).
BEVERAGE SYSTEM CLEANING
USER MAINTENANCE
CLEANING AND SANITIZING PROCEDURE
Caution:
It is required
that the Carbonated Water Lines should remain connected and opera-
tional during cleaning and sanitizing of the syrup circuits. Sanitizing of the valve without the
Carbonated Water side operation may leave bacteria in the nozzle, diffuser, and syrup tube.
Caution:
Do not allow cleaning and sanitizing solutions to remain in syrup systems longer than
recommended contact time. Exceeding contact time will result in damage to valve components.
Sanitize the beverage system at initial start-up as well as regularly scheduled cleaning. The drain pan must be in
place under soda valves, to carry away detergent and sanitizing agents that will be flushed through valves.