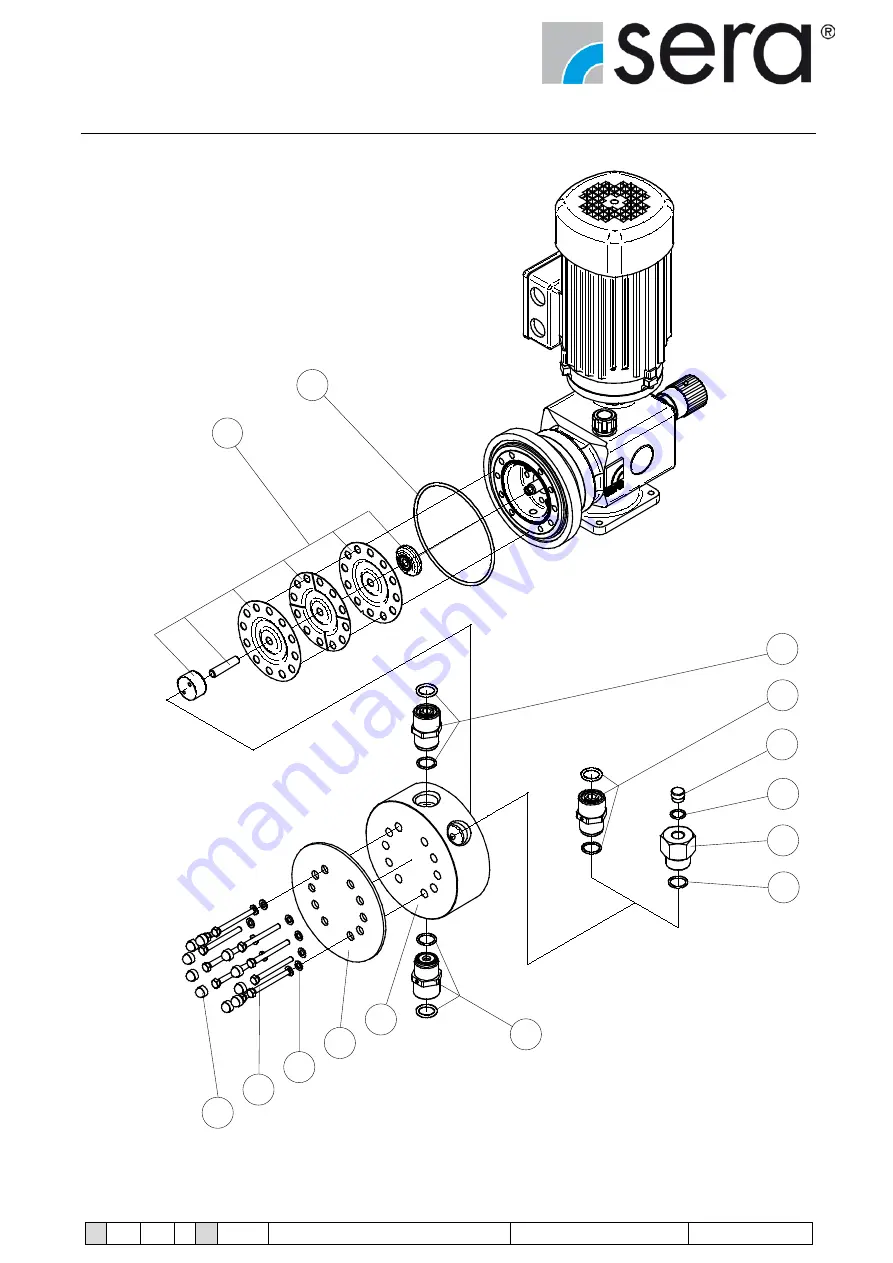
Multi-layer diaphragm pump
Serie 409.2 ML
Operating instruction
TA 431
Rev.
8 en
06/2015
Technical modifications reserved!
www.sera-web.com
27
10.3 Spare- and wearing parts
...409.2 – 11 ML
...409.2 – 17 ML
...409.2 – 30 ML
...409.2 – 45 ML
...409.2 – 72 ML
...409.2 – 110 ML
...409.2 – 150 ML
...409.2 – 220 ML
Fig. 34 Spare- and wearing parts
3
4
11
12
13
2
5
6
7
8
14
9
10
1
1.1
1.2
1.3
1.4
1.5
1.6