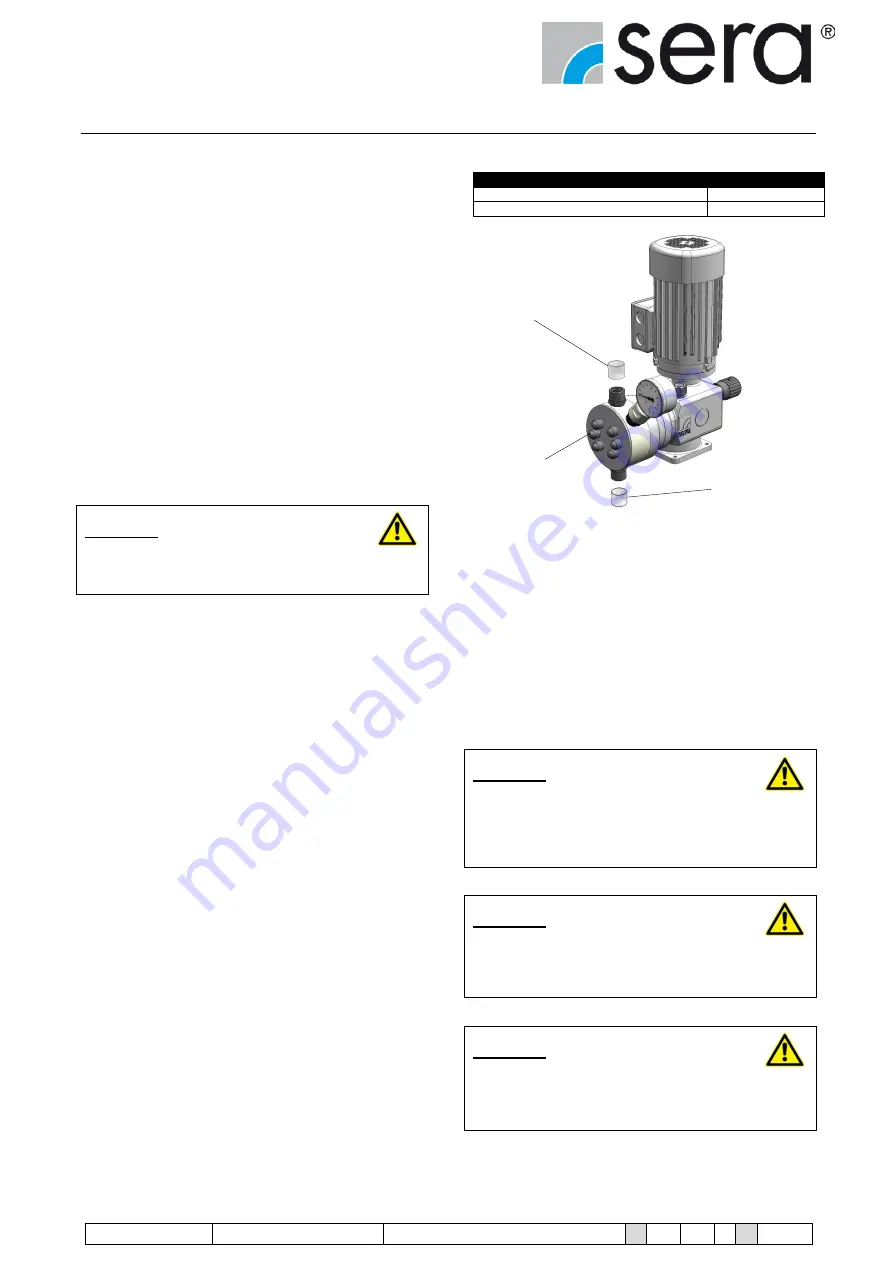
Multi-layer diaphragm pump
Serie 409.2 ML
Operating instruction
18
www.sera-web.com
Technical modifications reserved!
TA 431
Rev.
8 en
06/2015
7.3.6
Maintenance of the drive motor
The electric motor should always be kept clean so that neither
dust, dirt, oil nor other contaminates may affect the correct op-
eration.
In addition, we recommend to ensure that:
•
the motor does not produce strong vibrations
•
suction and blowing openings for the supply of cooling air
are not closed or restricted (may lead to unnecessary
high temperatures in the windings).
The ball bearings inserted in the motor are lubricated for life.
7.3.7
Restart
Restart the system as described in Chapter 7.3.4 after mainte-
nance work of after longer periods of standstill.
8
Installation
CAUTION!
In case of operation in explosion-hazardous areas, the
instructions in Chapter 9 must also be followed!
8.1
Installation instructions
•
The standard model of the pump is only approved for in-
stallation in dry rooms in a non-aggressive atmosphere,
at temperatures b2°C and +40°C and at permit-
ted humidity until approx. 90%, altitude 1000 m above
sea level. (For operation in explosion-harzardous areas,
see Chapter 9).
•
For dimensions of the pump connections and fixing holes,
see Fig. 04, Table 02.
•
Install the pump in such a way that there is no vibration
and no tension and that it is aligned precisely.
•
Install the pump at the optimum possible operating height.
Mount the pump in such a way that the valves are verti-
cal.
•
Ensure that there is sufficient space around the pump
body and the suction and pressure valve so that these
parts may be easily dismantled, if required.
•
The stroke length adjustment, indicator scale and visual
diaphragm rupture signalling must be easily accessible
and readable.
•
Design the nominal diameters of the downstream pipes
and of the connections built into the system to be the
same size or larger than the inlet / outlet nominal widths
of the pump valves.
•
To check the pressure ratios in the pipe system, we rec-
ommend to provide for connections for pressure gauges
(e.g. manometers) near the suction and pressure attach-
ments.
•
Provide evacuation fittings
•
Prior to connecting the pipes, remove the plastic caps on
the suction and pressure attachments of the pump.
•
Check that the fixing screws for the pump body are tightly
fitted and, if necessary, retighten.
Torque for tightening the fixing screws
Pump body
without
mounting plate
15 NM
Pump body
with
mounting plate
15 NM
Plastic cap
Fixing screws
Plastic cap
Fig. 19 Multi-layer diaphragm pump with plastic caps
•
For models with a built-on actuator, ensure sufficient
space for removal of the cover
(see Chapter 6.1 “Dimensions“)
•
Connect pipes to the pump in such a way that there are
no forces acting on the pump, such as e.g. misalignment,
weight or stress of the pipe.
•
Keep the suction lines as short as possible.
•
Use pressure- and medium-resistant hoses / pipes.
•
All pipes and containers connected to the pump must
comply with the regulations and must be cleaned, ten-
sion-free and intact.
CAUTION!
Where toxic, crystal-forming or corrosive liquids are being
delivered, the pipe system must have equipment to enable
it to be emptied, cleaned and, if necessary, rinsed with a
suitable medium.
CAUTION!
In the case of operation on the 60Hz network it is essential
to consider the possible higher stroke frequency when
designing the pipe geometry.
CAUTION!
The multi-layer diaphragm pump must be installed in such
a way that no damage can be caused if the medium leaks
out.