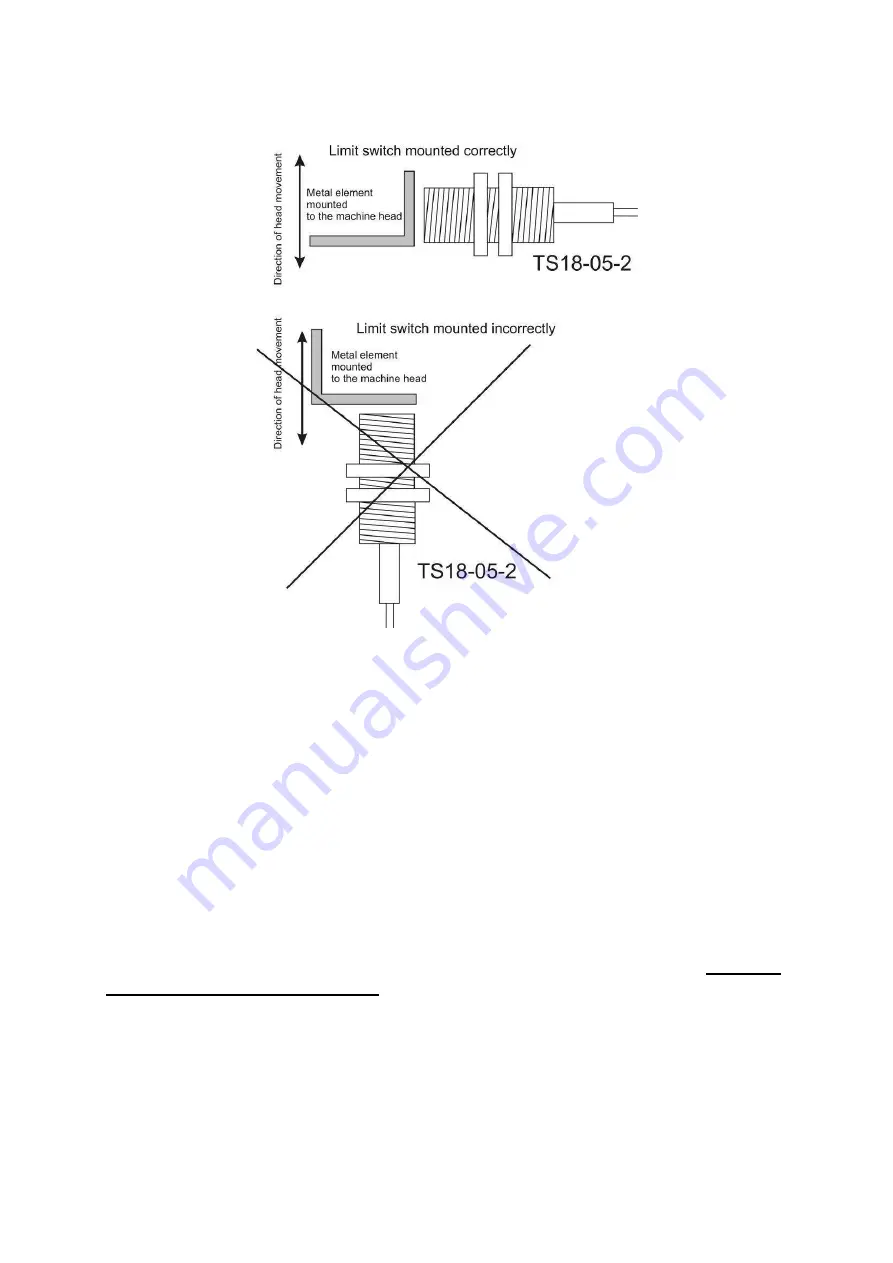
www.selbit.pl
- 8 -
Figure 6
Electrical connections of external components to the adjuster.
Before connecting the wires, it is absolutely necessary to turn off the power supply of the
converter and the ISP-12F adjuster!
Connection of control inputs of the frequency converter
For connection, use an 8-core screened control cable with a cross-section adapted to the
connection terminals.
The isolated ends of the individual conductors should be tightened in collets appropriate for
the given cross section; the use of collets improves electrical contact and prevents breaks in
connections. The screen (braid) of the cable should be connected to the connection only from
the side of the frequency converter!
Connection of cables from the adjuster to the converter should be made according to the
following description:
Summary of Contents for ISP-12F
Page 12: ...www selbit pl 12 Figure 11 Block diagram for rotary encoder...
Page 27: ...www selbit pl 27...
Page 29: ...www selbit pl 29...