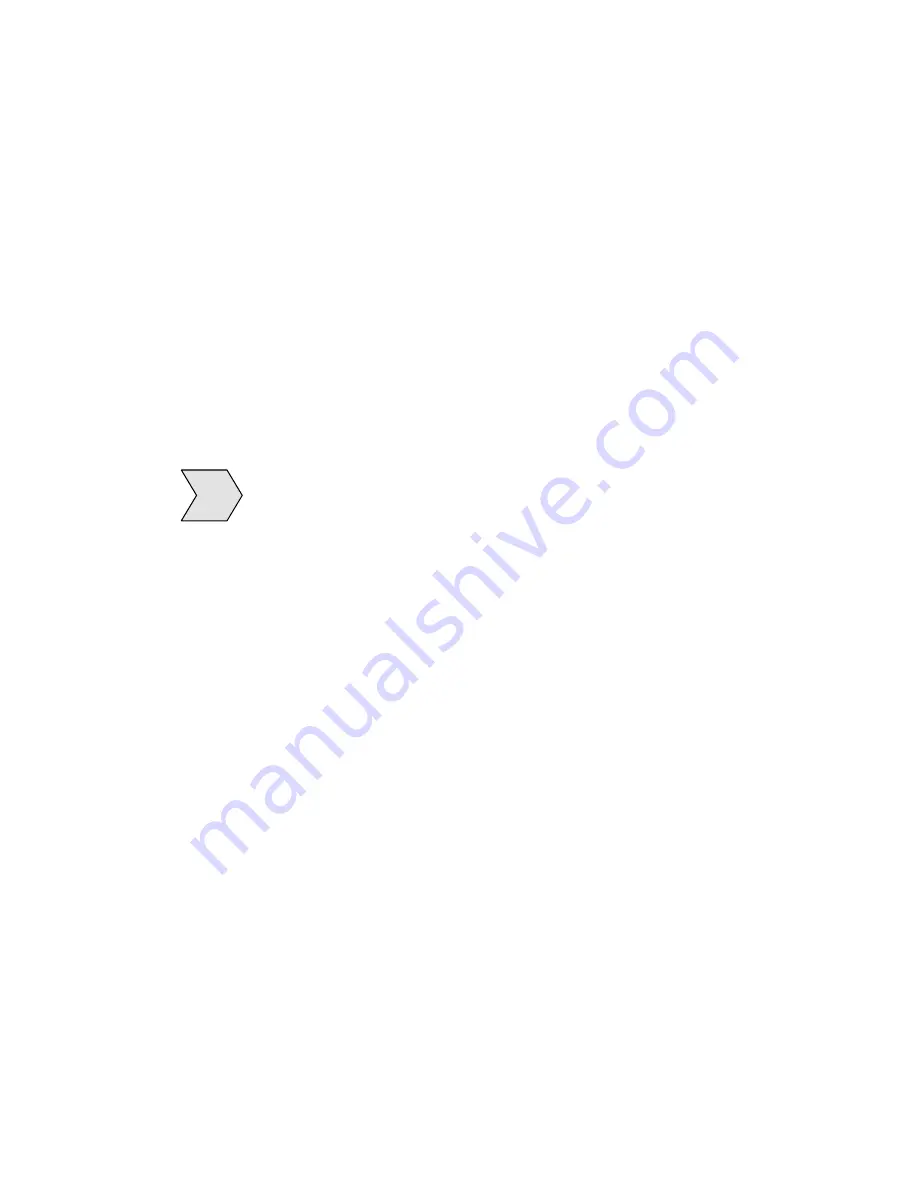
9
4.00 Shut-down
•
Close CO
2
cylinder and CO
2
stopcock at pressure reducer. (Model without membrane pump only)
•
Draw mains plug
.
•
Detach tank connection parts from beverage tank.
•
Employ specialist staff for having the appliance emptied and cleaned.
•
Detach beverage tubing.
5.00 Temperature adjustment
The temperature is adjusted via a thermostat at the lower side of the device.
6.00 Maintenance
6.10 Opening appliances
To open the appliances, unscrew the beer tap and remove the four lateral fastening screws. To open the
appliance, lift the synthetic cover.
Never operate the appliance without the cover in place.
6.20 Cleaning the beverage pump
The minimum requirements for cleaning of beverage pumps are stipulated in DIN 6650-6. Basically cleaning is
stipulated “as and when needed“. “Need” depends on output, type of beer, bar breaks and type of appliance.
Based on these factors, the common practise of cleaning the tubing system every 7 days must be considered
as sufficient in only a few cases. Listed below are notes on possible ways of cleaning as well as their
frequency.
Everywhere inside the beer pump where parts alternately come into contact with beer and air, germs may
grow that as a result of their being present everywhere in the ambient air. Therefore it is necessary to keep
these areas of the beer pump clean by daily cleaning (in particular the tap and drip pan). A germ-free
operation of the beer pump is impossible. However, regular thorough cleaning can prevent that germs multiply
and thus impair product quality (smell and taste) and result in cloudiness. Germ-infested tubing may
contaminate a connected keg that previously has left the brewery in an originally sealed and biologically
immaculate condition. It is of course also necessary to keep the area surrounding the beer pump in a
spotlessly clean condition.
Methods of line cleaning
Deposits are formed inside the beer line due to precipitation of minerals, hop resins and proteins present in
beer (beer scale). These deposits form a coating on all surfaces of the beer pump coming into contact with
beer (tubes, taps, tap heads). Viewed under a magnifier, these deposits look like sandpaper and in the long
run will become equally hard. These coatings will turn into a breeding place for micro organisms if not
removed regularly.
Mineral deposits require removal with the help of acidic detergents whereas hop resins require dissolving and
removing with alkaline detergents. Mechanical means (see below) may be used to cope up to a certain point
with both components.