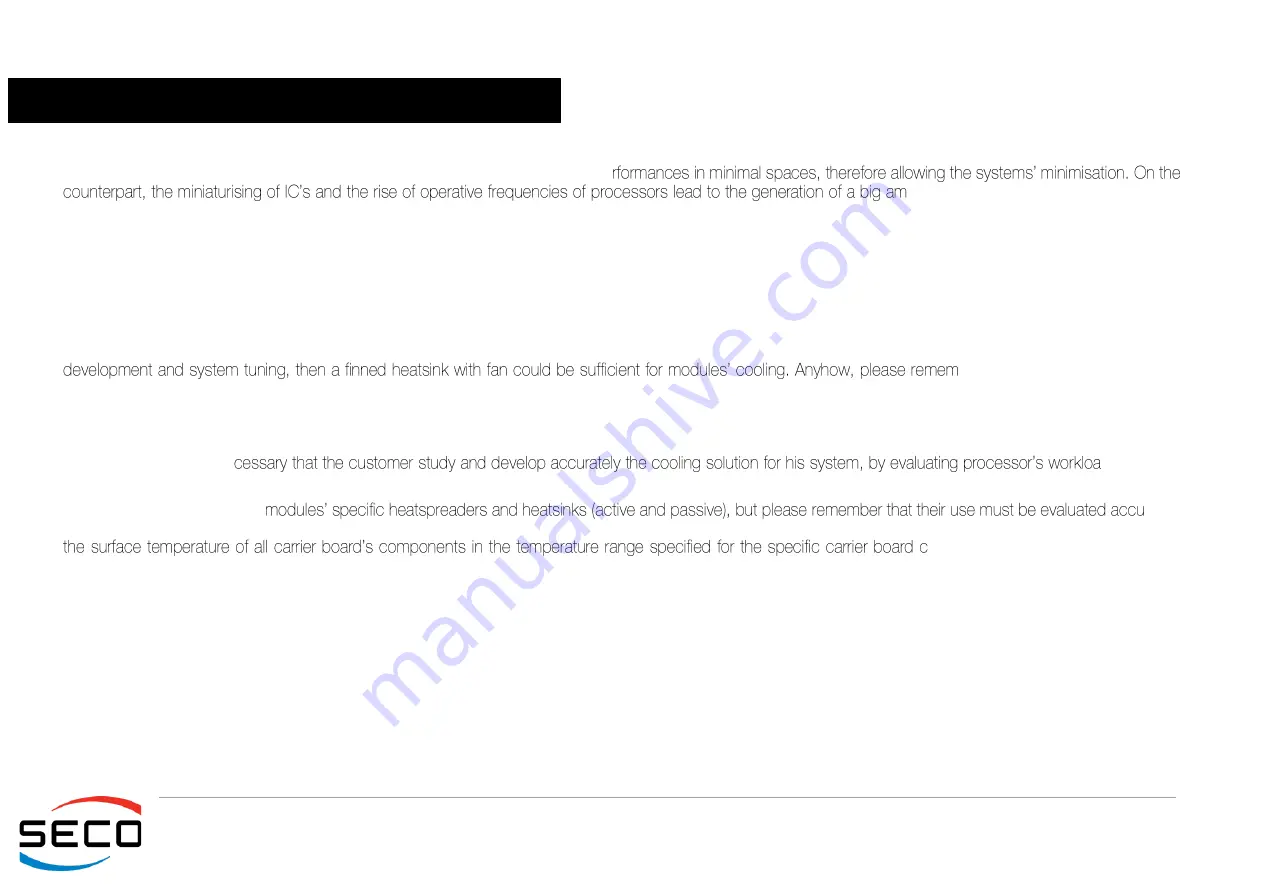
SM-B79
SM-B79 User Manual - Rev. First Edition: 1.0 - Last Edition: 1.0 - Author: A.R - Reviewed by M.B. - Copyright © 2021 SECO S.p.A.
77
4.1
Thermal Design
A parameter that has to be kept in very high consideration is the thermal design of the system.
Highly integrated modules, like SMARC
®
modules, offer to the user very good pe
ount of heat, that must be dissipated to
prevent system hang-off or faults.
SMARC
®
specifications take into account the use of a heatspreader, which will act only as thermal coupling device between the SMARC
®
module and an external
dissipating surface/cooler. The heatspreader also needs to be thermally coupled to all the heat generating surfaces using a thermal gap pad, which will optimise the
heat exchange between the module and the heatspreader.
The heatspreader is not intended to be a cooling system by itself, but only as means for transferring heat to another surface/cooler, like heatsinks, fans, heat pipes
and so on.
Conversely, heatsinks in some situation can represent a cooling solution. Until the modules are used on a development Carrier board, on free air, just for software
ber that all depends also on the
workload of the processor. Heavy computational tasks will generate much heat.
Indeed, when using SM-B79 carrier board with any SMARC
®
module, it is necessary to consider carefully the global heat generated by the system, and the scenario
of utilisation.
Therefore, it is always ne
d, utilisation
scenarios, the enclosures of the system, the air flow and so on. This is particularly needed for industrial grade modules.
SECO can provide SMARC
®
rately
inside the final system (elect mechanics), and that they should be used only as a part of a more comprehensive ad-hoc cooling solutions, which also keeps
onfiguration (industrial or commercial
grade).