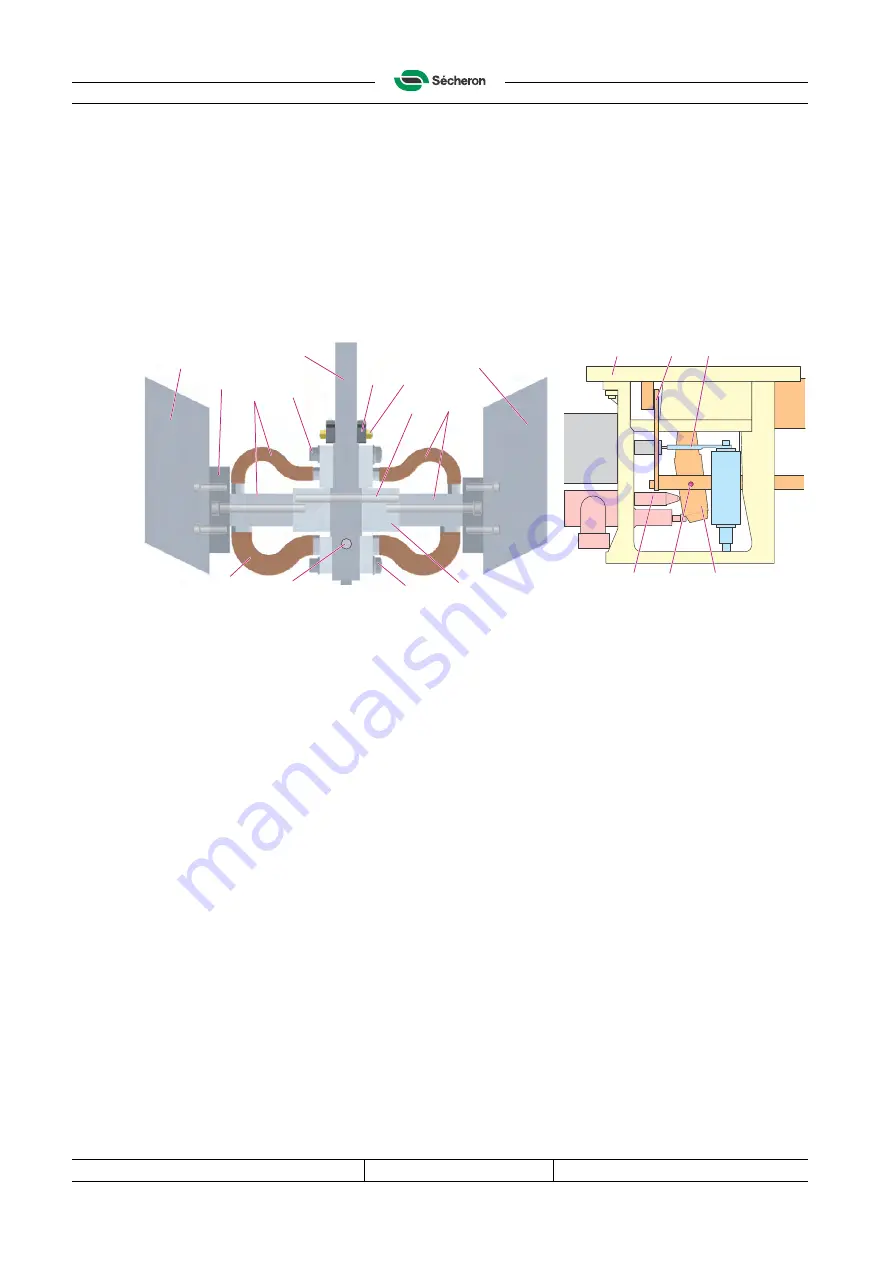
Maintenance
UR46-81/82S
Document number: SG104148TEN
Revision: B01
Issue date: 20.8.2012
Copyright© 2012 Sécheron SA - This document is not contractual and contains information corresponding to the level of technology at the date of release.
D-38
File: d-UR46-8S_maint_en.fm
D.7.2
Replacement of the moving contact
Disassemble
a) Remove the coolers (34) and the plates (35).
b) Remove both flexible connections (15).
c) Remove the catches (18) with the pins and threaded nut rod by unscrewing one of the
nuts (19).
d) Remove the end of the pusher (21) from its seat (22) on the moving contact.
e) Push the pin (23
)
out of the moving contact (17).
f)
Remove the moving contact (17) through the top plate (24).
04628-S
Reassemble
g) Insert the new moving contact (17) through the top plate (24) between both pawls of the
fork (25). Lightly grease the fork and the moving contact catches.
h) Insert the pin (23
)
.
i)
Insert the end of the pusher (21) into its seat (22) on the moving contact.
j)
Reassemble new catches (18) with the pins, threaded nut rod and both nuts (19).
k) Connect the flexible connections (15) with the thicker flexible connections (42) underneath:
first onto the top part, then onto the lower part and finally onto the lower connecting bar (16).
l)
Refit the plates (35) and the coolers (34).
D.7.3
Reassemble the metal strips, the pole and the fixed contact
Refer to both figures above.
Assemble the metal strips
a) Insert new metal strips (30): align the metal strips holes (31) with the top plate (24) holes.
Assemble the pole
b) Insert the blow-out core (13) into the new pole (12).
c) Insert this assembly correctly into the circuit-breaker, hold it against the rib of the frame (24)
to place and tighten the flange (10).
d) Assemble both straight connections (9) onto the connecting plate (11) and the flexible
connections (15).
e) Insert the M8 screw (8) into the frame plate (24) and fasten the pole (12) with the thin M8
nut (3; tightening torque of 17 Nm) and spring washer (4).
f)
Fit the flange (2) and hand tighten the M8 nut and washers.
15
35
34
34
14
17
14
22
42
16
15
19
18
23
17
23
25
24
9
21
Summary of Contents for UR46-81S
Page 68: ...Secheron ...