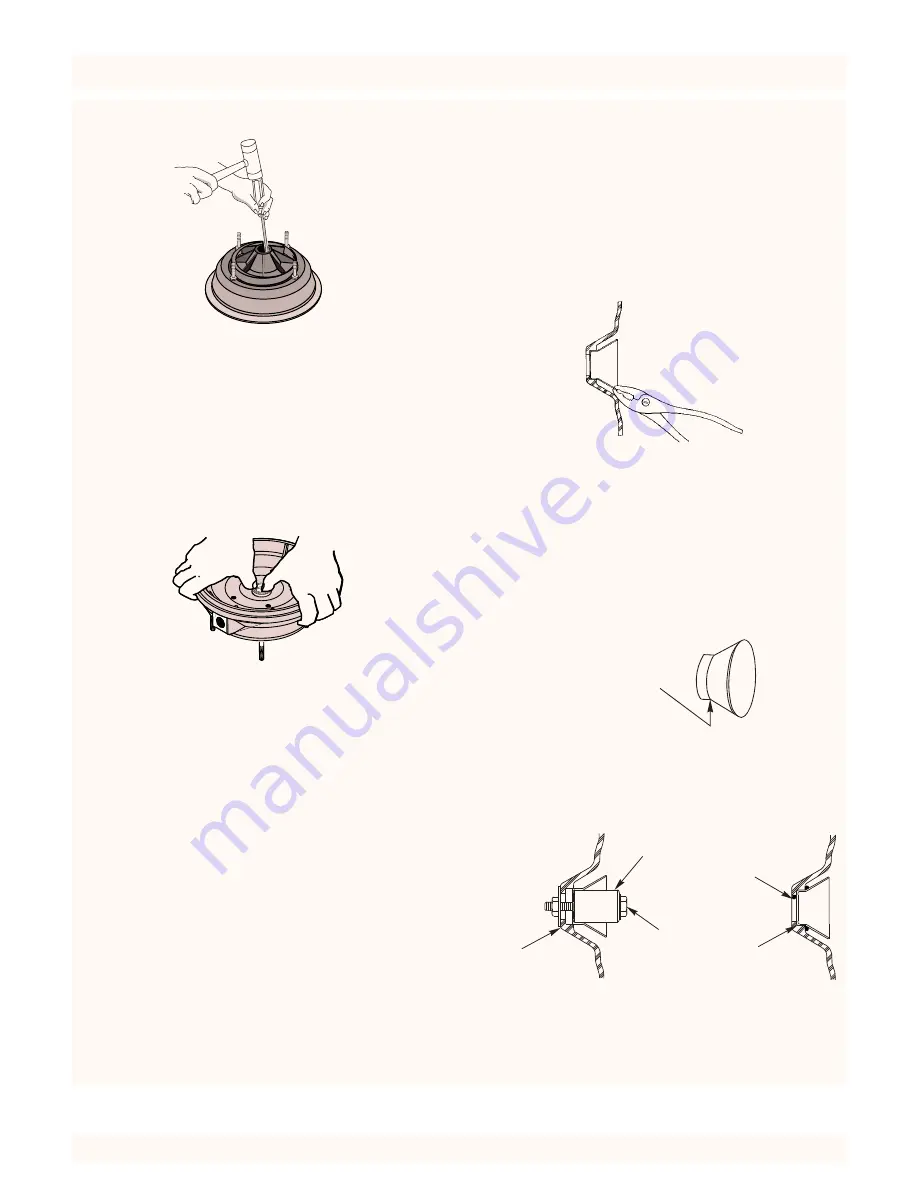
MAINTENANCE (Continued)
4. Place pump body half face down on flat surface and tap
out stationary half of seal (see Figure 16).
INSTALLING NEW SEAL
1. Wet outer edge of Rubber Cup on ceramic seat with liq-
uid soap. Be sparing!
2. Put clean cardboard washer on seal face. With thumb
pressure, press ceramic seal half firmly and squarely into
seal cavity in seal plate (see Figure 17). Polished face of
ceramic seat is up. If seal will not seat correctly, remove,
placing seal
face up
on bench. Reclean cavity. Seal should
now seat correctly.
3. If seal does not seat correctly after recleaning cavity, place
cardboard washer over polished seal face and
carefully
press into place using a piece of standard 3/4” pipe as a
press.
NOTICE:
Be sure you do not scratch seal face.
4. Dispose of cardboard washer and recheck seal face to be
sure it is free of dirt, foreign particles, scratches and
grease.
5. Inspect shaft to be sure it is free of nicks and scratches.
6. Reassemble pump body half to motor flange.
BE SURE
it
is right side up.
7. Apply liquid soap sparingly (one drop is sufficient) to in-
side diameter of rotating seal member.
8. Slide rotating seal member (carbon face first) onto shaft
until rubber drive ring hits shaft shoulder.
NOTICE:
Be sure not to nick or scratch carbon face of seal
when passing it over threaded shaft end or shaft shoulder.
The carbon surface must remain clean or short seal life will
result.
9. Hold motor shaft with 7/16” open end wrench on shaft
flats (Figure 14, Page 8) and screw impeller onto shaft.
Be
sure you do not touch capacitor terminals with
body or any metal object.
Tightening impeller will au-
tomatically locate seal in correct position.
10. Remount diffuser on pump body half with five screws.
INSTALLING COPPER INSERT -
2 HP ONLY
NOTE:
If the copper insert moves or shifts during seal re-
moval, it should be removed and reinstalled.
1. Remove copper insert as shown in Figure 18. Do not de-
form.
2. Replace copper insert:
A. Clean off all surplus Permatex from around insert cav-
ity. Be careful not to scratch or mark the machined
bore. It is important that this area be clean so no old
Permatex lodges behind the new insert and causes im-
proper seating.
B. Place small amount of No. 2 non-hardening Permatex
on surface of insert as shown. Smooth out with finger.
See Figure 19.
C. Pull insert into cavity as shown in Figure 20.
D.Clean out any surplus Permatex from insert cavity
where new seal will be located. See Figure 21.
9
477 0194
Figure 17 – Press in New Seal
Figure 18
Figure 19
479 0194
Figure 16 – Tap Out Seal
To Disassemble
Wipe on small amount of
non-hardening Permatex
on this surface
Remove
Surplus
Permatex
Properly
Seated
Figure 21
Figure 20
7/8" Socket
Bolt
1-3/8" O.D.
Washer
038 0893