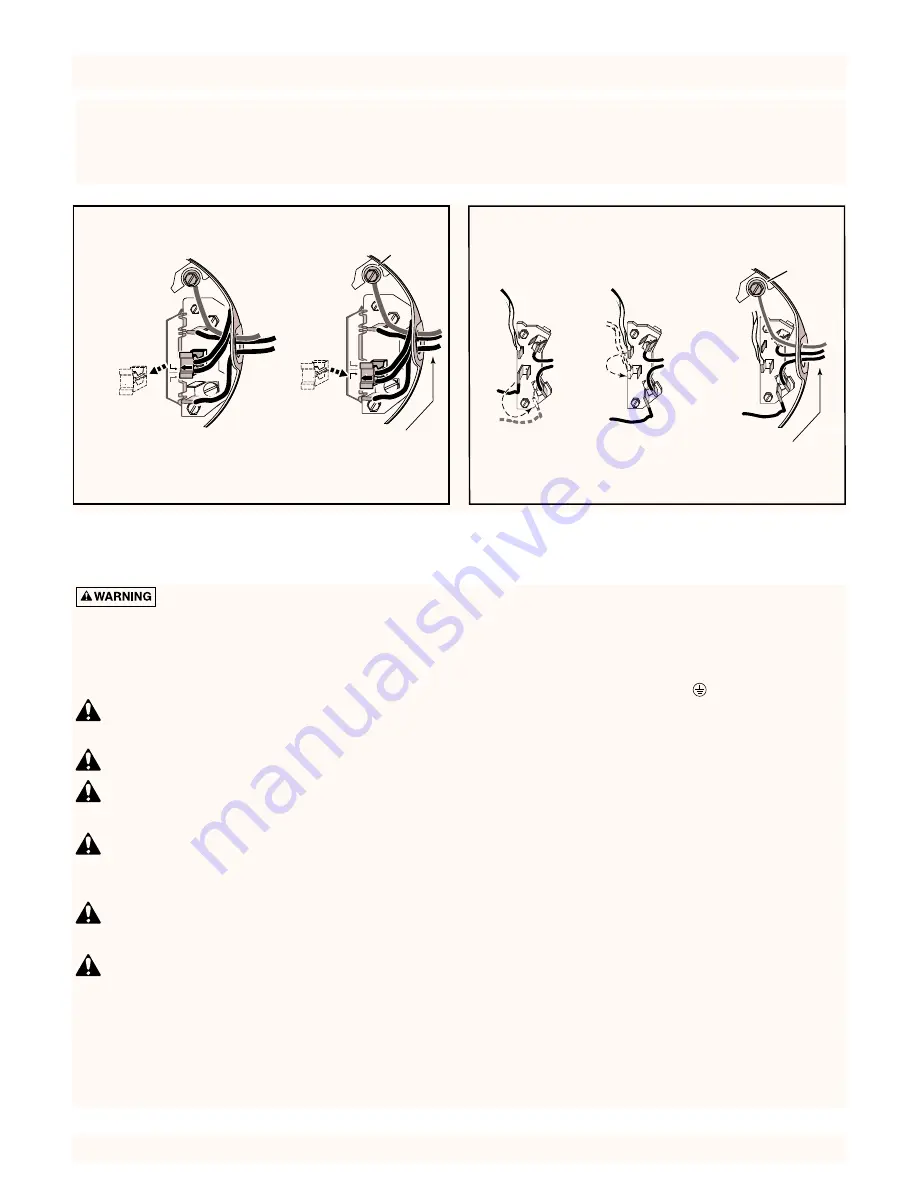
ELECTRICAL
Hazardous voltage.
Can shock, burn, or
cause death. Disconnect power to motor before working on
pump or motor. Ground motor before connecting to power
supply.
WIRING
Ground motor before connecting to electrical
power supply. Failure to ground motor can cause
severe or fatal electrical shock hazard.
Do not ground to a gas supply line.
To avoid dangerous or fatal electrical shock, turn
OFF power to motor before working on electri-
cal connections.
Supply voltage must be within ±10% of name-
plate voltage. Incorrect voltage can cause fire or
damage motor and voids warranty. If in doubt consult
a licensed electrician.
Use wire size specified in Wiring Chart (Page 5).
If possible, connect pump to a separate branch
circuit with no other appliances on it.
Wire motor according to diagram on motor
nameplate. If nameplate diagram differs from
diagrams above, follow nameplate diagram.
1. Install, ground, wire and maintain this pump in accor-
dance with electrical code requirements. Consult your
local building inspector for information about codes.
2. Provide a correctly fused disconnect switch for protec-
tion while working on motor. Consult local or national
electrical codes for switch requirements.
3. Disconnect power before servicing motor or pump. If the
disconnect switch is out of sight of pump, lock it open
and tag it to prevent unexpected power application.
4. Ground the pump permanently using a wire of the same
size as that specified in wiring chart (Page 5). Make
ground connection to green grounding terminal under
motor canopy marked GRD. or
.
5. Connect ground wire to a grounded lead in the service
panel or to a metal underground water pipe or well cas-
ing at least 10 feet long. Do not connect to plastic pipe or
insulated fittings.
6. Protect current carrying and grounding conductors from
cuts, grease, heat, oil, and chemicals.
7. Connect current carrying conductors to terminals L1 and
L2 under motor canopy. When replacing motor, check
wiring diagram on motor nameplate against Figure 6. If
the motor wiring diagram does not match either diagram
in Figure 6, follow the diagram on the motor.
IMPORTANT:
115/230 Volt single phase models are
shipped from factory with motor wired for 230 volts. If
power supply is 115 volts, remove motor canopy and re-
connect motor as shown in Figure 6. Do not try to run motor
as received on 115 volt current.
8. Motor has automatic internal thermal overload protec-
tion. If motor has stopped for unknown reasons, thermal
overload may restart it unexpectedly, which could cause
injury or property damage. Disconnect power before ser-
vicing motor.
9. If this procedure or the wiring diagrams are confusing,
consult a licensed electrician.
6
A
B
L2
L1
A
B
L2
L1
A
B
L2
L1
A
B
L2
L1
230 Volt to 115 Volt Conversion, Spade Connector Type
Move black wire
from A to L1
1.
1.
2.
2.
3.
3.
A
B
L2
L1
A
B
L2
L1
Ground
Screw
Move white wire
with black tracer
from B to A
Change Complete
Clamp the power cable to prevent
strain on the terminal screws
Connect the green (or bare copper) ground
wire to the green ground screw
A
L1
2
3
0
V
o
lt
s
1
1
5
V
o
lt
s
230 Volt to 115 Volt Conversion, Plug-in Type
Pull plug
straight
out from
terminal
board
1.
1.
2.
2.
Plug in again
with arrow
on plug
pointing to
'115 Volts'
Ground
Screw
A
L1
2
3
0
V
o
lt
s
1
1
5
V
o
lt
s
Clamp the power cable to prevent
strain on the terminal screws
Connect the green (or bare copper) ground
wire to the green ground screw
Connection diagram for dual voltage, single-phase motors.
Your dual-voltage motor’s terminal board (under the motor
end cover) will match one of the diagrams below. Follow
that diagram if necesary to convert motor to 115 Volt
power.
Connect power supply wires to L1 and L2. For 3-phase mo-
tors, or if motor does not match these pictures, follow the
connection diagram on the motor nameplate.
Figure 6 – 115/230V Dual Voltage Single Phase Wiring Diagram