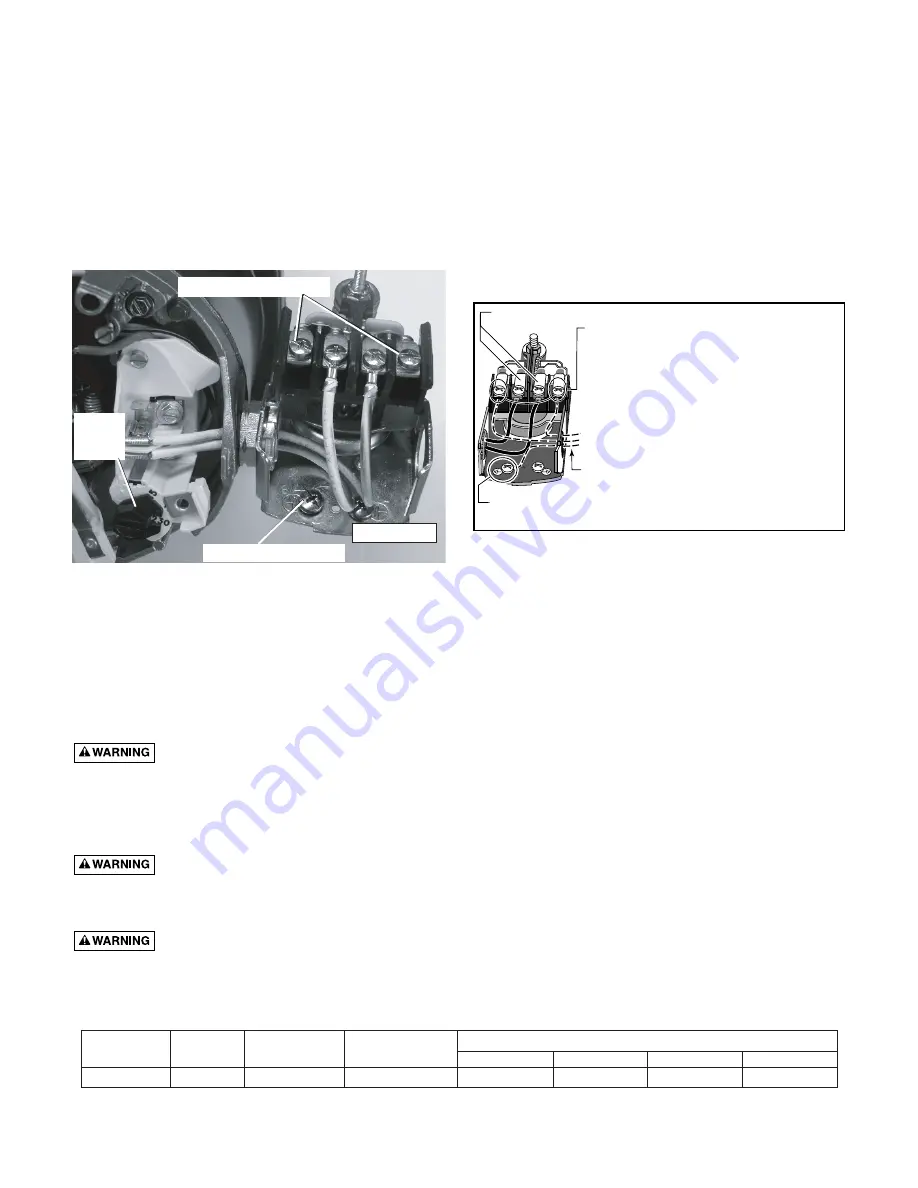
ELECTRICAL
9
To change to 115 volts:
1. Make sure power is off.
2. Pull the plug toward you.
3. Move and attach the plug at the 115 volt position.
The plug will now cover 2 metal tabs.
4. Reinstall the Motor end cover
5. Go to Wiring Connections below.
Dial Type Voltage Selector
To change to 115 volts:
1. Make sure power is off.
2. Turn the dial counter-clockwise until 115 shows in
the dial window.
3. Reinstall the Motor end cover
4. Go to Wiring Connections below.
Hazardous voltage. Can shock, burn,
or kill. Connect ground wire before connecting
power supply wires. Use the wire size (including
the ground wire) specified in the wiring chart.
If
possible, connect the pump to a separate branch cir-
cuit with no other appliances on it.
Explosion hazard. Do not ground to
a gas supply line.
Wiring Connections
Fire hazard.
Incorrect voltage can cause
a fire or seriously damage the motor and voids the war-
ranty. The supply voltage must be within ±10% of the
motor nameplate voltage.
NOTICE:
Dual-voltage motors are factory wired for
230 volts. If necessary, reconnect the motor for 115
volts, as shown. Do not alter the wiring in single volt-
age motors.
Install, ground, wire, and maintain your pump in com-
pliance with the National Electrical Code (NEC) or the
Canadian Electrical Code (CEC), as applicable, and
with all local codes and ordinances that apply. Consult
your local building inspector for code information.
Connection Procedure
1. Connect the ground wire first as shown in Figure 14.
The ground wire must be a solid copper wire at least
as large as the power supply wires.
2. There must be a solid metal connection between the
pressure switch and the motor for motor grounding
protection. If the pressure switch is not connected
to the motor, connect the green ground screw in the
switch to the green ground screw under the motor
end cover. Use a solid copper wire at least as large
as the power supply wires.
3. Connect the ground wire to a grounded lead in a ser-
vice panel, to a metal underground water pipe, to a
metal well casing at least ten feet (3M) long, or to a
ground electrode provided by the power company
or the hydro authority.
4. Connect the power supply wires to the pressure
switch as shown in Figure 17.
Clamp the power cable to prevent strain
on the terminal screws.
Connect the green (or bare copper) ground wire
to the green ground screw.
Motor wires
connect here
.
3187 0398
Power supply wires
connect here.
230 Volt:
Connect 2 hot wires (black and red)
here and cap the white (neutral) wire. It does
not matter which wire goes to which screw.
115 Volt:
Connect one hot wire (black or red)
to one of these screws (it doesn't matter
which one). Connect the white (neutral) wire
to the other screw. Cap any remaining
black or red wires.
Ground Wire Connection
Power Supply Connections
Voltage
Change
Dial
Pressure Switch
Figure 16 – Voltage Set To 230 Volts, Dial Type
Figure 17 – Pressure Switch Wiring
WIRING CHART –
Recommended Wire and Fuse Sizes
(*)Time delay fuse or circuit breakers are recommended in any motor circuit.
MOTOR
MAX. LOAD
BRANCH FUSE*
DISTANCE IN FEET FROM MOTOR TO METER
HP
VOLTS
AMPS
RATING (AMPS)
0 to 50
51 to 100
101 to 200
201 to 300
1
115/230
19.2/9.6
25/15
10/14
10/12
8/10
6/10