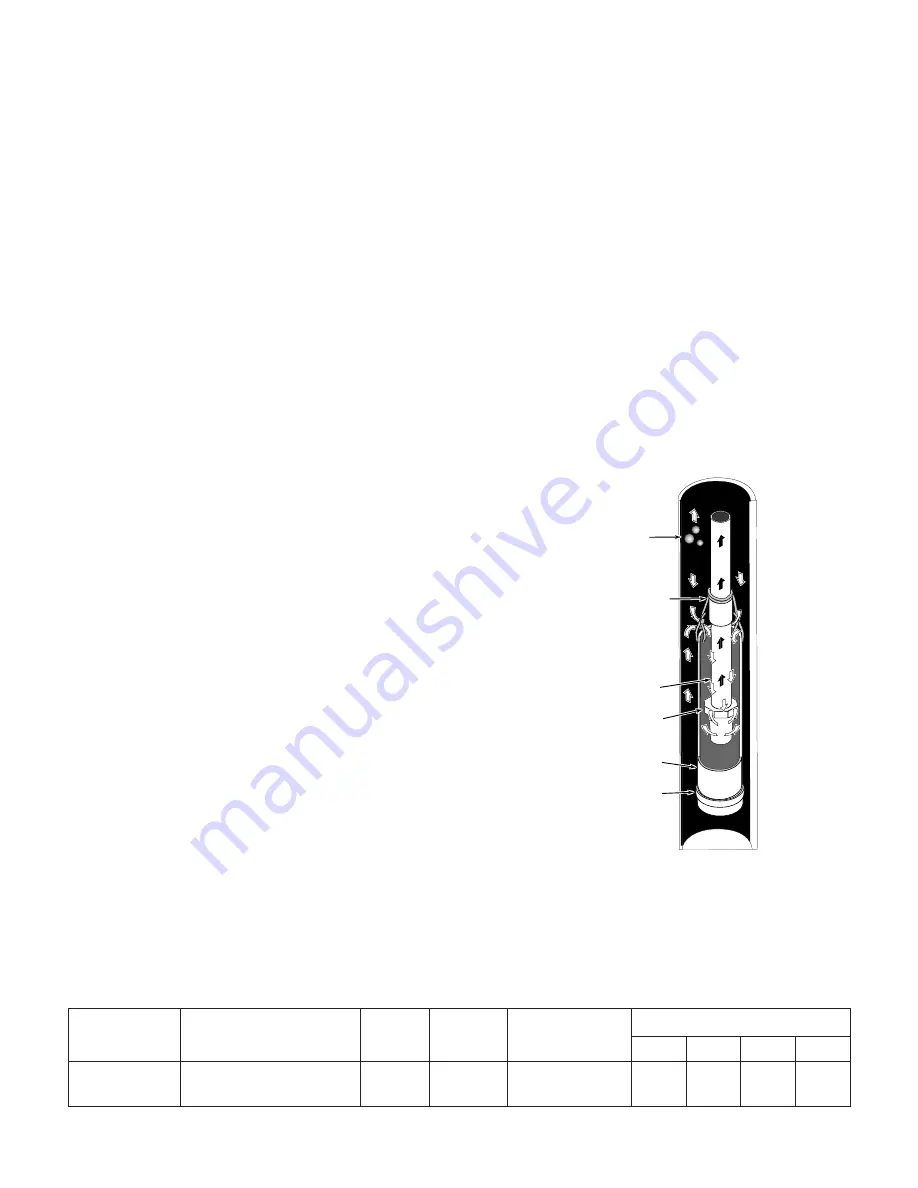
MAINTENANCE
4. Lubricate inside diameter and outer face of rubber
drive ring with soapy water and slide assembly on
motor shaft (sealing face first) until rubber drive
ring hits shaft shoulder.
5. Screw impeller onto the shaft until impeller hub
stops against shaft shoulder. This will automatically
locate seal in place and move the sealing washer
face up against seat facing.
Cleaning Impeller
1. Disconnect power to pump.
2. Remove motor.
(a) Remove motor wiring from pressure switch.
(b) Remove 4 capscrews, Key No. 17, Page 10,
which hold the motor to the pump body.
(c) Remove motor, seal plate, impeller and diffuser,
(Key Nos. 1, 3, 6 and 7), Page 10, as a unit.
Diffuser, Key No. 7, can now be lifted off and the
impeller exposed and cleaned.
Replacing Venturi
Follow Steps 1 and 2 above, for Cleaning
Impeller.
1. Remove venturi, Key No. 9, Page 10, by turning it
counter-clockwise. This will expose the nozzle, Key
No. 10, which can be removed by using a 5/8” hex
socket and turning it counter-clockwise.
2. To replace venturi, turn it clockwise until snug.
3. Replace all parts. Connect motor wiring and turn
on power.
Cleaning Shallow Well Jet
1. Disconnect power to pump.
2. Unscrew cleanout plug (Key No. 15, Page 10) from
pump.
3. Insert an ice pick or other small diameter pointed
tool into the nozzle and dislodge foreign material.
If it is not possible to push the obstruction through
the nozzle or if the nozzle is damaged, follow in-
structions above under “Replacing Venturi”.
4. Replace all parts. Connect motor wiring and turn
on power.
HOW TO HANDLE
A GASEOUS WELL
In some localities well water contains gases which
must be allowed to escape before the water is used.
This can be done as shown in Figure 8.
A good way of delivering gas-free water is to suspend
a pipe, closed at the bottom and open at the top, sur-
rounding the suction pipe, Figure 8. Since the gases
rise in the well casing, the water sucked down through
the pipe and into the suction pipe is free of gas. It is
imperative that this type of well be vented to the out-
side of any enclosure.
Air Control In Flowing Wells
Flowing wells, or wells with little or no drawdown,
could create a special problem in air control in the op-
eration of your water system.
In such cases, it is recommended that you install a
Captive Air
®
Tank, in which an air control mechanism
is not required.
8
Figure 8
Not
to
Scale
Pipe strap or
wire to hold
pipe sleeve
Pipe
sleeve
Pipe
cap
Tail
pipe
Foot
valve
2369 0396
Gases
rise to
surface
Pump
Suction Discharge
Discharge
Pumping Depth in Feet
Model
Description Size
Size
Pressure
PSI
5’
10’
15’
20’
1/2 HP Cast Iron
1-1/4"
1"
40
8.2
7.3
6.2
5.0
390.2505
Shallow Well Jet
Pump Performance (In Gallons per Minute)