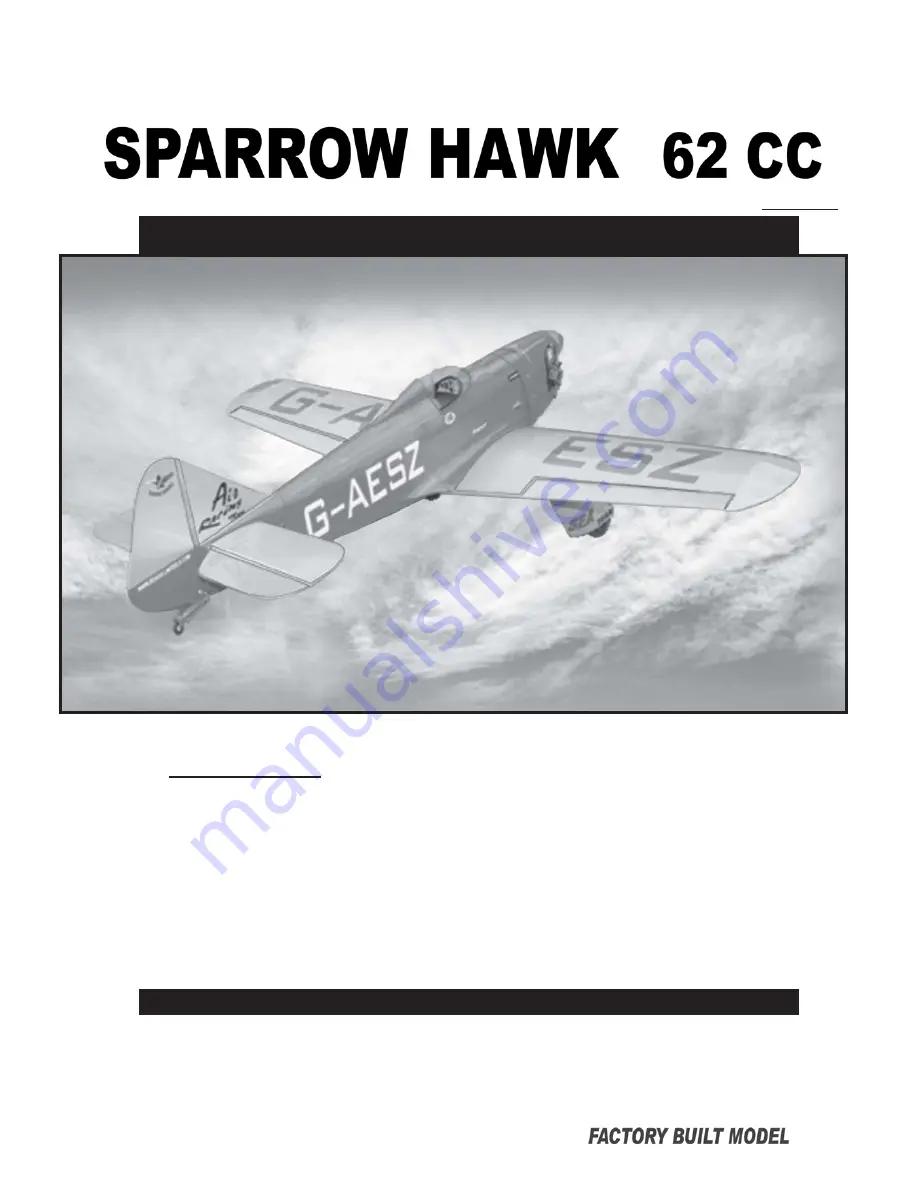
Made in Vietnam.
ASSEMBLY MANUAL
MS: SEA 68
“Graphics and specfications may change without notice”.
Kit features.
•
Ready-made—minimal assembly & finishing required.
•
Ready-covered covering.
•
Photo-illustrated step-by-step Assembly Manual.
Specifications
Wingspan--------------------------------------85.4 in------------------------------ 216cm.
Wing area------------------------------------ 1371 sq.in-------------------- 88.5 sq.dm.
Approximate flying weight---------------- 19 lbs--------------------------------- 8.6kg.
Length----------------------------------- ------ 71.5in------------------------------- 181cm.
Recommended engine size-------------------------------- 62cc Gasoline Engine.
Radio System required 4 channels with 6 digital servos/karbonite or metal
gear.
Flying skill level Intermediate/advanced.
Item code : SEA 68.