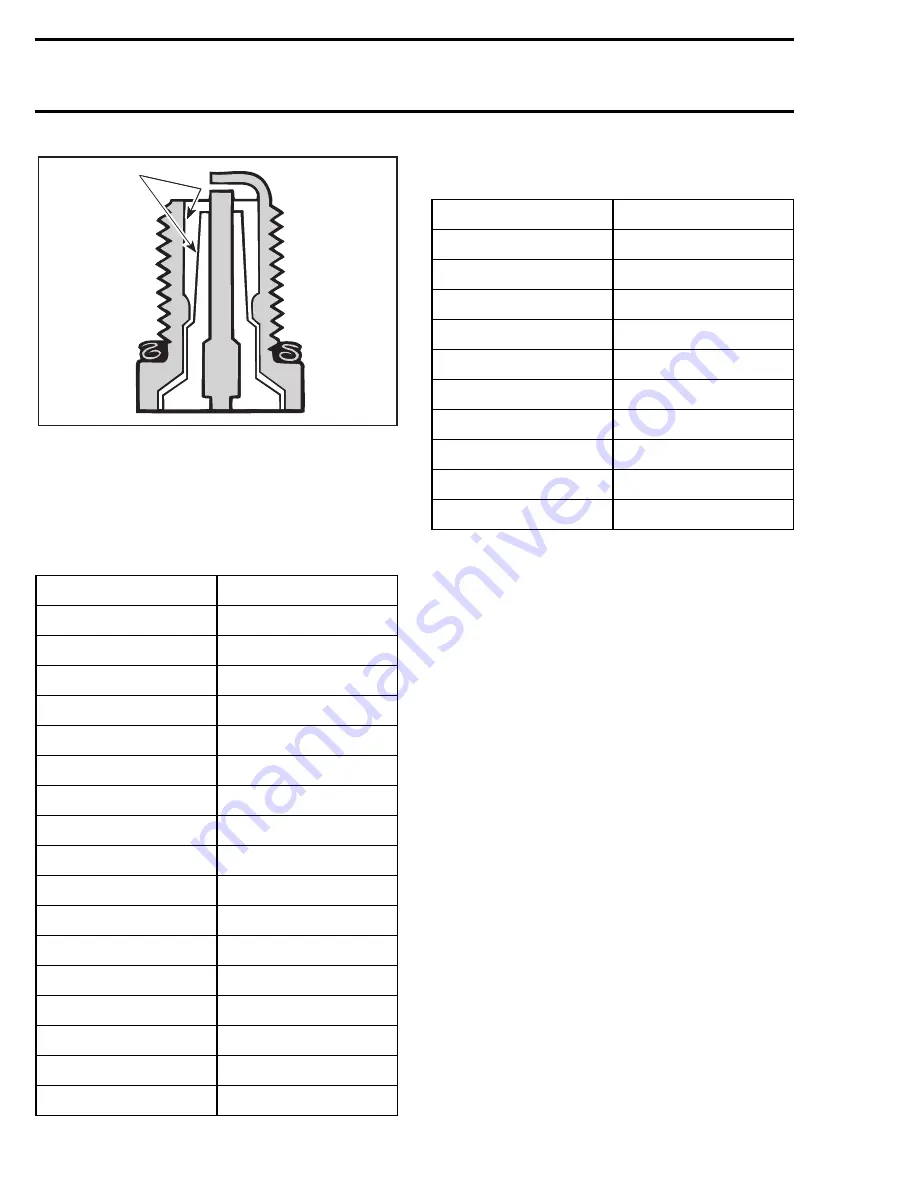
03-72
SECTION 03 - ENGINE PREPARATION
1. Location to check spark plug coloration
Refer to the appropriate
Shop Manual of your wa-
tercraft for instructions on changing carburetor
jetting.
Main Jets for Mikuni Super BN
Carburetors
Pilot Jets for Mikuni Super BN
Carburetors
If in doubt with carburetion jetting, always begin
with a rich setting and work toward a lean adjust-
ment.
NOTE:
It is recommended you always race with
your fuel tank valve on the “reserve” position.
This should eliminate any possibility of air enter-
ing in the fuel system should the fuel tank level be
lower than a quarter full.
RACING ENGINE PREPARATION
SUMMARY
NOTE:
Most machining and/or grinding is illegal in
limited class racing. Keep your watercraft legal:
check the rules.
1. Remove and disassemble the engine according
to appropriate model year
Shop Manual proce-
dures.
2. With the crankshaft resting in the lower half of
the crankcase, set up a dial indicator and check
the runout of the crankshaft at both ends. You
should see no more than 0.05 mm (.002 in)
runout. If you have the capability, adjust the
crankshaft as close to perfect as possible.
MAIN JET SIZE
PART NUMBER
102.5
270 500 157
105
270 500 158
107.5
270 500 116
110
270 500 159
115
270 500 181
120
270 500 160
122.5
270 500 161
125
270 500 162
127.5
270 500 148
130
270 500 163
132.5
270 500 225
135
270 500 174
137.5
270 500 268
140
270 500 251
142.5
270 500 209
147.5
270 500 210
175
270 500 318
F01E1AA
1
PILOT JET SIZE
PART NUMBER
55
270 500 202
57.5
270 500 201
60
270 500 180
62.5
270 500 164
65
270 500 117
67.5
370 500 165
70
270 500 175
72.5
270 500 166
75
270 500 149
77.5
270 500 167
Summary of Contents for Bombardier
Page 1: ......