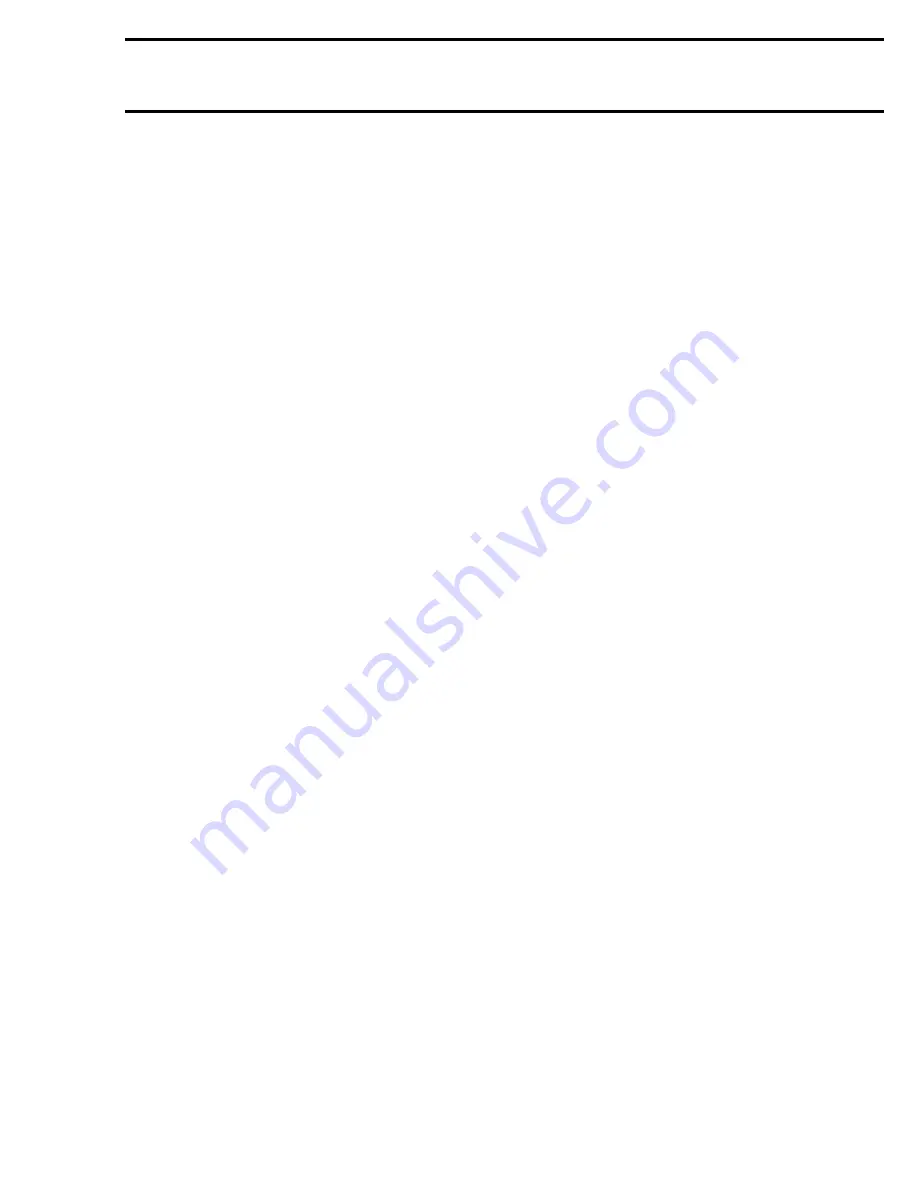
02-3
SECTION 02 - HULL PREPARATION
e. Measure the low area and mix up enough filler
material to fill the area in. Follow the manufac-
turers mixing instructions. Fill low area and
blend in evenly with bondo spreader. Try to
leave your filler a little high so you have material
to sand. Allow proper curing time.
f. Using the pneumatic long sander, sand the area
until you accomplish a flat surface. Remember
to finish edges, radius and flat sections of
strakes as well. Using the straight edge, check
the area which was just finished. Verify flatness
and if the area still has a low spot, start your
filling steps again.
g. At the rear of the watercraft, where the tran-
som meets the hull, there is a radius (approxi-
mately 4 mm) that should be covered with
epoxy fairing compound and sanded to a
square edge.
h. For refinish, we recommend using PPG prod-
ucts. PPG high build K-36 primer can be used
for fine finishing small hull irregularities after
application of fairing compound.
PAINTING
General
The following was prepared in conjunction with
PPG Industries Inc. It contains 2 painting proce-
dures, CONCEPT
TM
the most commonly used,
and DELTA
TM
(with low VOC) mainly used in Cali-
fornia.
If more information is needed, contact a PPG deal-
er or a Sea-Doo watercraft authorized dealer.
CONCEPT
TM
PAINTING
PROCEDURE
For additional information refer to
PPG P-Bulletin
no.168.
Surface Preparation
Prepare and clean surface consistent with good
painting practices.
Primer
DP Epoxy Primer/DP 401 Catalyst; DX 1791/1792
(prime before topcoating).
Primer Surfacer
K36/K201, K200/K201 or DZ KONDAR
®
Primer
Surfacers.
NOTE:
KONDAR
®
must be sealed before apply-
ing CONCEPT color.
Sealer
KTS30 2K Sealer, DP Epoxy Primer reduced as a
sealer or DAS 1980 or DAS 1987.
Direct Gloss Color
How to Mix
Standard Air Dry: Mix CONCEPT Color 2:1:1 – 2
parts color with 1 part DT Reducer best suited to
shop temperatures and 1 part DU 4 below 29°C
(85°F) or DU 5 above 29°C (85°F) Hardener.
Standard Force Dry: Mix CONCEPT Color 2:1:1 –
Application temperatures below 29°C (85°F) use
DU 5 Hardener, above 29°C (85°F) use DU 6.
Medium Solids (MS) Application: For faster film
build, when using solid colors, mix 2 parts CON-
CEPT color with half part DT Reducer and 1 part
DU 5 or DU 6 Hardener. Select the DT Reducer
appropriate for shop temperature.
Pot Life
Pot Life of ready-to-spray CONCEPT color is 6 to
8 hours at 21°C (70°F). Medium solids option is 2
to 4 hours at 21°C (70°F).
Full Panel and Overall Repairs
Application
Apply 1 medium wet coat and give 5-10 minutes
flash, followed by 2 wet coats with 15 minutes
flash time between each coat. Adjust metallic on
the last full wet coat. If necessary, apply a mist
coat. For medium solids option apply 2 full wet
coats.
Air Pressure
275-345 kPa (40-50 PSI) at the gun.
Dry Time
– dust free: 30 minutes
– tack free: 2 to 3 hours
– tape print free: 6 hours
– dry to handle: 6 to 8 hours at 21°C (70°F)
– force dry: 40 minutes at 60°C (140°F)
Faster dry times may be obtained by using 15 mL
(1/2 oz) of DXR 81 Accelerator per sprayable 1.2 L
(quart), however, the pot life is reduced to 2
hours.
Summary of Contents for Bombardier
Page 1: ......