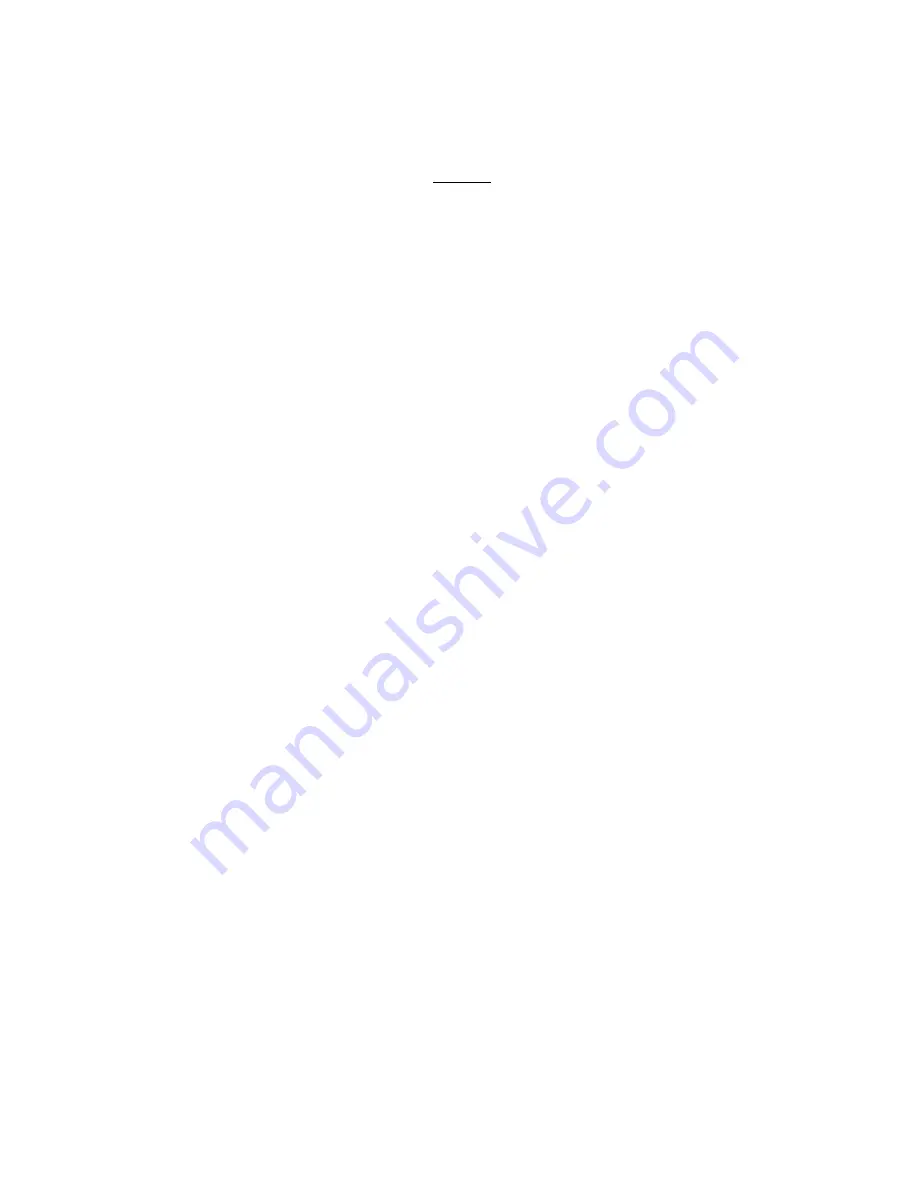
Page 21
Page 21
SECTION III
TESTING
COMPLETE SYSTEM LEAK TESTS
During pressure testing for leaks, keep the
compressor suction service valve and discharge
service valve closed to prevent air and moisture
from entering the compressor. All other valves in
the system must be open.
Sufficient liquid refrigerant shall be charged into
the system to raise the pressure to 2.5 atm. and
dry nitrogen added to obtain the desired test
pressure (20.5 atm is sufficient).
Leak testing shall be performed with an electronic
leak detector, unless the use of a halide torch is
specifically authorized by the owner.
Refrigeration piping will not be acceptable unless
it is gas tight.
If any leaks are found, isolate the defective area,
discharge the gas and repair the leaks and then
repeat the test. When testing has been completed
release all pressure freely to atmosphere.
COMPLETE SYSTEM EVACUATION
The system shall be evacuated with a vacuum
pump specifically manufactured for vacuum duty,
having a capacity of pulling a vacuum of 50
microns or less.
Evacuation of the system must never be done by
the use of the refrigerant compressor. The pump
should be connected to both the low and high
side evacuation valves with vacuum hoses. The
compressor service valves should remain closed.
A high vacuum gauge capable of registering
pressure in microns should be attached to the
system pressure readings.
Never put the compressor in operation. To check
system pressure, a hand valve must be provided
between the pressure gauge and the vacuum
pump which can be closed to isolate the system
and check the pressure.
Evacuate the system to an absolute pressure not
exceeding 1,500 microns. Creak the vacuum to
excess pressure of 0,15 atm (1 psig) with the
refrigerant to be used in the system.
Repeat the evacuation process again breaking
the vacuum with refrigerant. Install a definitive
drier of the required size in the liquid, open the
compressor suction and discharge valves and
evacuate to an absolute pressure not exceeding
500 microns. Leave the vacuum pump running
for not less than two hours without interruption.
Raise the system pressure to 0,15 atm (1 psig)
with refrigerant and remove the vacuum pump.
COMPLETE SYSTEM - CHARGING
Refrigerant shall be charged directly from original
drums through a combination filter drier.
Charge the system by means of a charging fitting
in the liquid line.
Wheigh the refrigerant drum before charging so
that an accurate record can be kept of the weight
of refrigerant put in the system. It refrigerant is
added to the system through the suction side on
the compressor, charge in vapor form only. The
process used most often to determine correct
refrigerant charge is to observe the refrigerant
flow in the sight glass in the liquid line.
As steady supply of liquid is necessary for proper
functioning of expansion valves; it can be
assumed that the system has been correctly
charged when a clear flow of liquid refrigerant is
visible.
Bubbles or foam usually indicate insufficient
refrigerant, even if there could be other reason
for the bubbles or foam to appear in the sight
glass. So, the practice to relay on the sight glass
only to determine whether the systems is correctly
charged is certainly good but not fully positive.
After the final leak test, refrigerant lines exposed
high ambient conditions should be insulated to
reduce heat pick-up and prevent the formation of
flash gas in the liquid lines.
Suction line should be insulated if exposed, to
prevent condensation.
START-UP - CHECK-OUT
Compressor and condensing unit will normally
be delivered to the job with sufficient oil for
average installation.
Check compressor for proper oil level and, if
necessary, add sufficient oil to bring the level to
the center of the cranckase sight glass.
Use only refrigeration oil recommended by the
compressor manufacturer.
Remove or loosen shipping retainers under
motor-compressor. Make sure hold down nuts
on spring mounted compressor are not touching
the compressor feet.
Check electrical connections. Be sure they are
all tight. Check high and low pressure control,
water valves, pressure regulating valves, safety
controls and adjust if necessary.
OPERATION CHECK-OUT
After system has been charged and checked-out
make sure to correctly position, attached to the
unit ice spout, the require chute (not supplied).
Perform a through re-check of entire system as
per following steps.
1. Make sure to open the water supply line shut-
off valve and that water flows freely from float
valve into float reservoir and from this to the
drum basin.