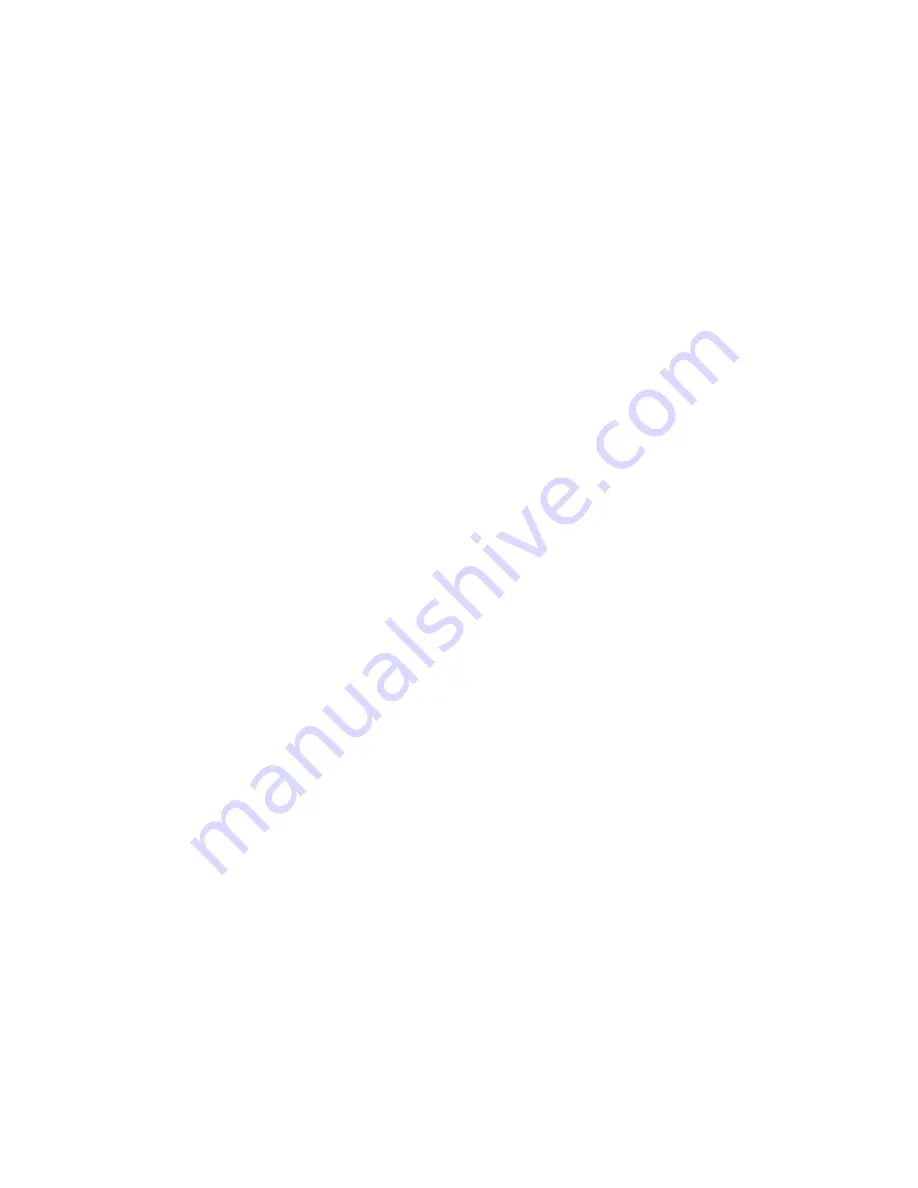
Page 28
Page 28
9. Check to see the surface conditions of cylinder
shaft journal. It is of extreme importance that
this surface be clean, smooth and polished.
In case of scored surface it is necessary to
stroke on it a very fine sand paper stripe.
Check to see that washer (5) be properly clean
and positioned with keyway to match the key.
10. If necessary replace the 0 rings of the S.S.
ring that houses the graphitic ring.
11. Proceed attentively to examine the graphitic
sulface of the seal ring. If this surface is no
more perfect and optically flat, proceed to
replace the seal ring in the following way.
Lubricate the outer surface of the new seal
ring with compressor oil and place it at the
inferior of the housing ring.
12. Place on drum shaft the steel ring housing
the graphite ring.
13. Mount on drum shaft journal the remaining
portion of seal mechanism (S.S. ring and
spring) (9) then the seal mechanism ring (10).
14. Fit the screw of 4 MA with its nut in one of the
three threaded holes then screw down the
nut in order to compress the spring.
15. When the seal mechanism spring has been
partially compressed fit the other two screws
and full compress the spring by screwing
down gradually the three tightening point.
16. After have tightened the screws unloose the
tie rod screw and replace it with the third one.
17. Clean carefully the inner surface of refrigerant
manifold. Check to see the good condition of
the seal ring (8) and fit it in its seat inside the
refrigerant manifold. Fit on shaft end the
washer (12) which keeps in place the seal
ring (13) inside the refrigerant manifold and
fit inside the manifold the gasket.
18. Position the manifold on the six monting
studs, fit the six mounting nuts and washers
and tighten all them down by means of a 10
mm. wrench.
19. Connect the outlet refrigerant line to the
corresponding port of the manifold and tighten
it with the four head necessed screw.
20. Connect the refrigerant inlet line on its
manifold fitting and tighten the fitting flarenut.
3
REMOVAL AND REPLACEMENT OF
THE DRIVE MOTOR
A. To remove the drive motor assembly:
1) Remove screws and front, top and right side
panels.
2) Slid-off V belt from motor pulley.
3) Unloose and remove hex head screw
securing the pulley to motor shaft.
4) Disconnect wire leads to motor.
5) Remove two hex head bolts, lockwashers
and washer, and nut which attach the sleigh
support plate of motor to the side frame of
evaporator drum basin.
6) Lift the sleigh plate with the drive motor out
of the Chassis.
7) Unloose and remove 4 Nuts securing the
motor to the sleigh plate.
B. To replace the Drive Motor Assembly reverse
the removal procedure.
4. REMOVAL AND REPLACEMENT OF
GEAR BOX
A. Remove screws and front, top and right side
panels.
1) Slid-odd V Belt from gear box pulley.
2) Remove screw securing pulley on gear box
input shaft.
3) Remove four nuts and washers which secure
the gear box to the evaporator basin side
frame.
4) With a mallet hit a bit the gear box to create
some looseness.
5) With the help to two screw driver inserted
between basin wall and flanged end of gear
box, force the gear box to clear away from
basin wall if you encounter an excessive
resistance in this. If better to use a 2-jaws
Puller.
6) When gear box is cleared away from the wall
where it is mounted, pull it out from cylinder
shaft.
A. To install the Gear Box Assembly reverse
the removal procedure taking care to center
keyway of gear box bore to keys on cylinder
shaft.
5. REPLACEMENT OF FIBER KEYS
A. The replacement of fiber keys is necessary
only when the keys are broken, so that they
do not engage the gear motor with the
evaporator drum drive shaft.
In practical terms, the gear box does not
drive the evaporator drum.
B. To reach the fiber keys to be replaced it is
necessary to remove the complete gear box.
For this operation perform all steps at point
12.