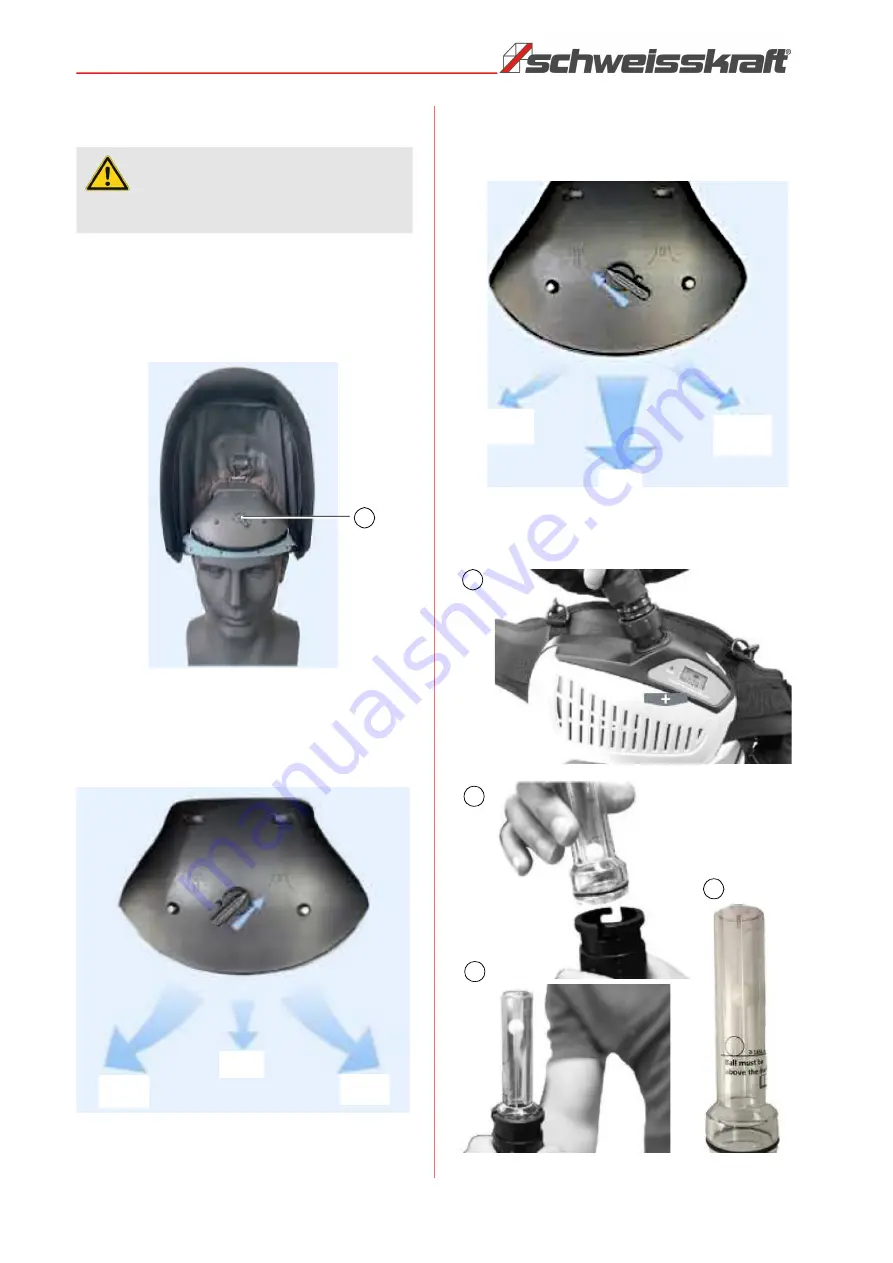
14
VarioProtect XXL-W TC AIR TH3 | Version 1.06 | EN
Utilization
13 Utilization
13.1 Adjustment of the air flow
The air flow can be set in two ways using the switch on
the front of the inner hood (item 1, figure 15).
Fig. 15: Switch to adjust the flow
When the switch is in the right position, distribution takes
place in three zones (Fig. 16). The two outer zones each
receive 40% and the middle zone 20% of the air flow.
Fig. 16: Air distribution 40 %,20 % and 40%
With the switch in the left position, distribution is also car
-
ried out in three zones (Fig.17). The two outer zones each
receive 10% and the middle zone 80% of the air flow.
Fig. 17: Air distribution 10%,80% and 10%
13.2 Air flow test
Fig. 18: Air flow test
ATTENTION!
Never use the welding helmet with the fan switched
off.
1
40 %
20%
40 %
10%
10%
80%
1
2
3
4
Summary of Contents for VarioProtect XXL-W TC AIR TH3
Page 27: ...Notes VarioProtect XXL W TC AIR TH3 Version 1 06 EN 27 22 Notes ...
Page 28: ......