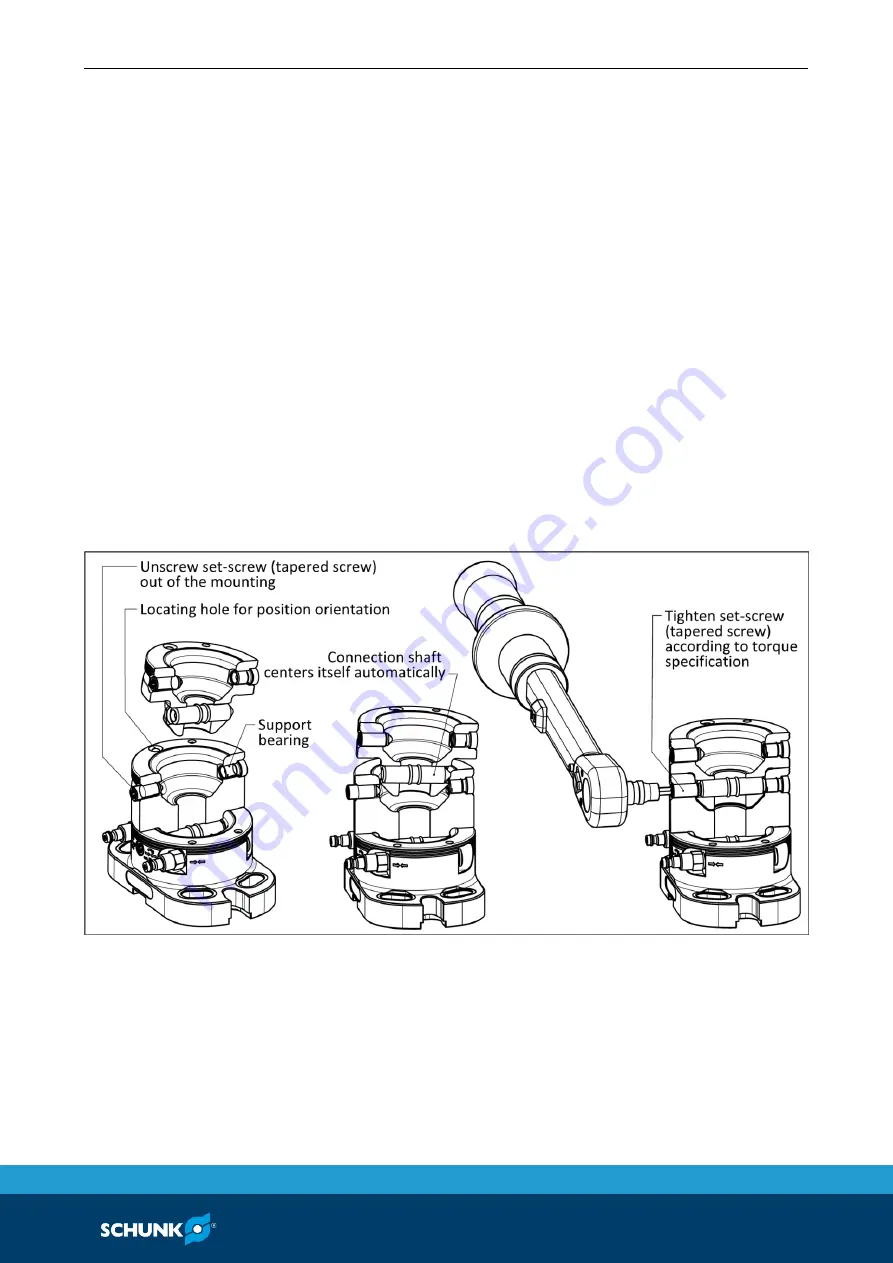
Functional description
03.00|WDP-5X |en
57
When changing an additional modular system component, the
tapered screw at the intake interface of a base module or stacking
module must be turned back clockwise until the tapered tip of the
screw does not protrude into the taper mounting.
The contact surfaces of the clamping systems must be clean and
dry before changing. Make sure that the sealing elements for the
compressed air routing are not damaged. The change components
can now be changed into the unlocked intake interface. In doing
so, ensure that they are installed in the correct direction. A
cylindrical pin is intended as a guide.
The clamping systems can be fixed using the T-handle hexagonal
socket screw driver included. For clamping, the precise screw
tightening torque must be initiated at the clamping area. The
connection point is hereby fixed and positioned.
A tapered screw is included in the scope of delivery as a spare
part.
Sequence when substituting a stacking module into the change
interface