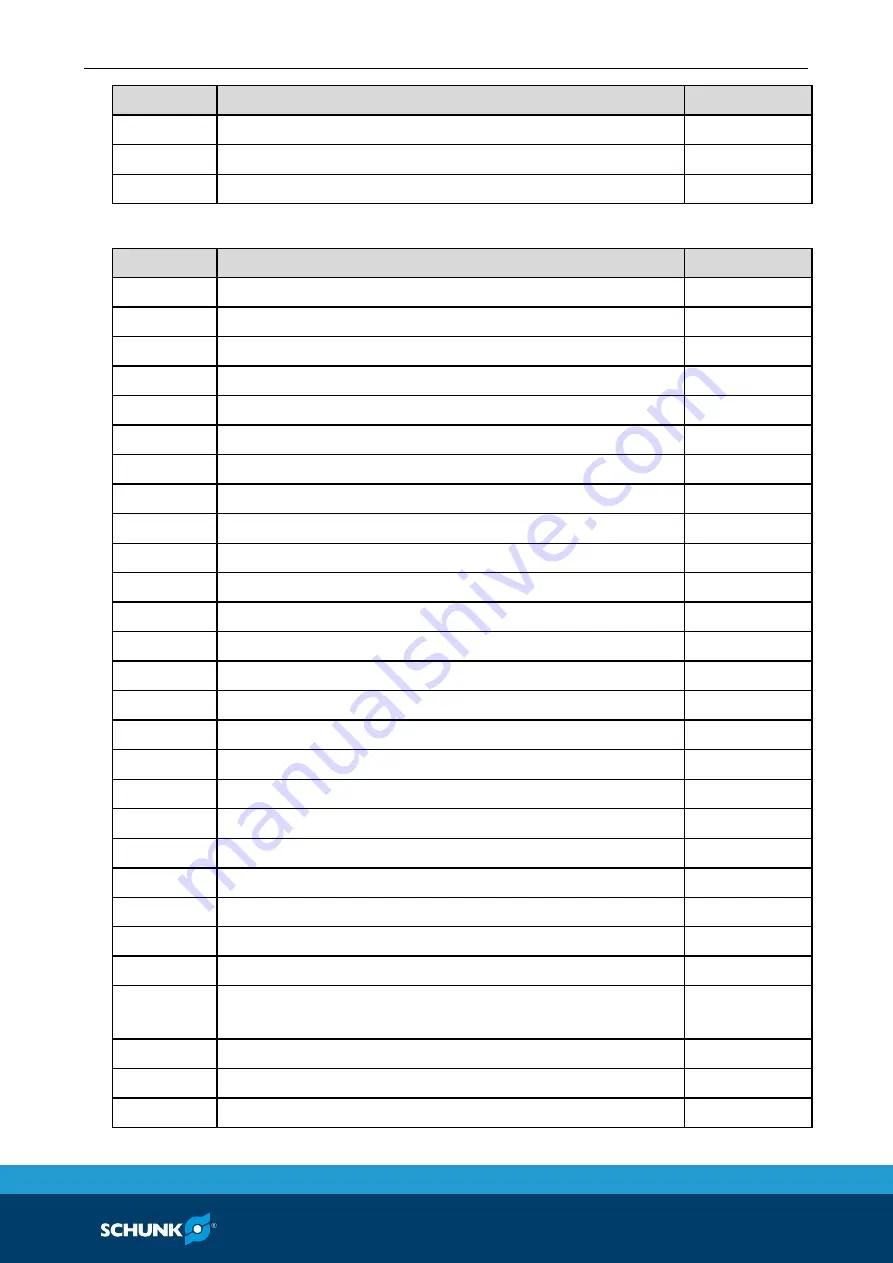
Seal Kit and Parts List
04.00|1151449 KSPplus-BWM, KSP-LHplus-BWM |en
47
Item
Designation
Quantity
34
Compression spring
2
35
Cylindrical pin, DIN 7979 - 5 m6 x 24 mm
1
45
O-ring DIN 3771 5.5 x 1.50
2
KSP-LH plus 160-BWM
Item
Designation
Quantity
1*
Body
1
2*
Base jaw
2
3*
Chuck piston
1
4
Cylinder piston
1
5
Cover
1
6
Covering strip
2
7
Covering strip
1
8***
Plug
4
9***
Fitting screw 12f7/M10
2
10
Lubrication nipple
4
11
Locking screw
2
12**
Quad-ring 126.59 x 3.53
1
13
Sound absorber
1
14
Screw DEI 4762/10.9 M10 x 25 mm
1
15**
Combined sealing element
1
16
Countersunk screw, DIN EN ISO 4026 M3 x 6 mm
4
17**
O-ring DIN 3771 150 x 2.00
1
18***
O-ring DIN 3771 12 x 2.00
4
19***
Screw DEI 4762/10.9 M10 x 40 mm
4
20**
Flat seal
17
21
Countersunk screw, DIN EN ISO 10642/10.9 M5 x 20 mm 15
22**
Flat seal
2
23
Set-screw, similar to DIN EN ISO 4026/45H M5 x 4 mm
4
25
Countersunk screw, DIN EN ISO 10642/10.9 M5 x 10 mm 2
26
Set-screw, similar to DIN EN ISO 4026/45H M4 x 4 mm
IN6RD/VZ/PA
1
27***
Clamping sleeve, DIN EN ISO 13337 DRM. 13 x 18
2
31
Locking bolt
2
32
Unlocking bolt
4